when you finally get one, I'll be more than willing to come over and help you out. :-) i did 9oz CF top and bottom in the srewed up pair and and I love the flex!skidesmond wrote: I'm not ready to attempt CNC yet. Kudos to you for taking a crack at it.
It's amazing how much stiffer CF will make a ski. I've only played around with 9.4 oz uni and it's really really stiff. I used CF in my daughters skis and I'm worried it will be too stiff for her to bend the ski and that was a 3in strip the length of the ski. We'll see...
Bent Green Things 13/14
Moderators: Head Monkey, kelvin, bigKam, skidesmond, chrismp
YESSSS!!!!!
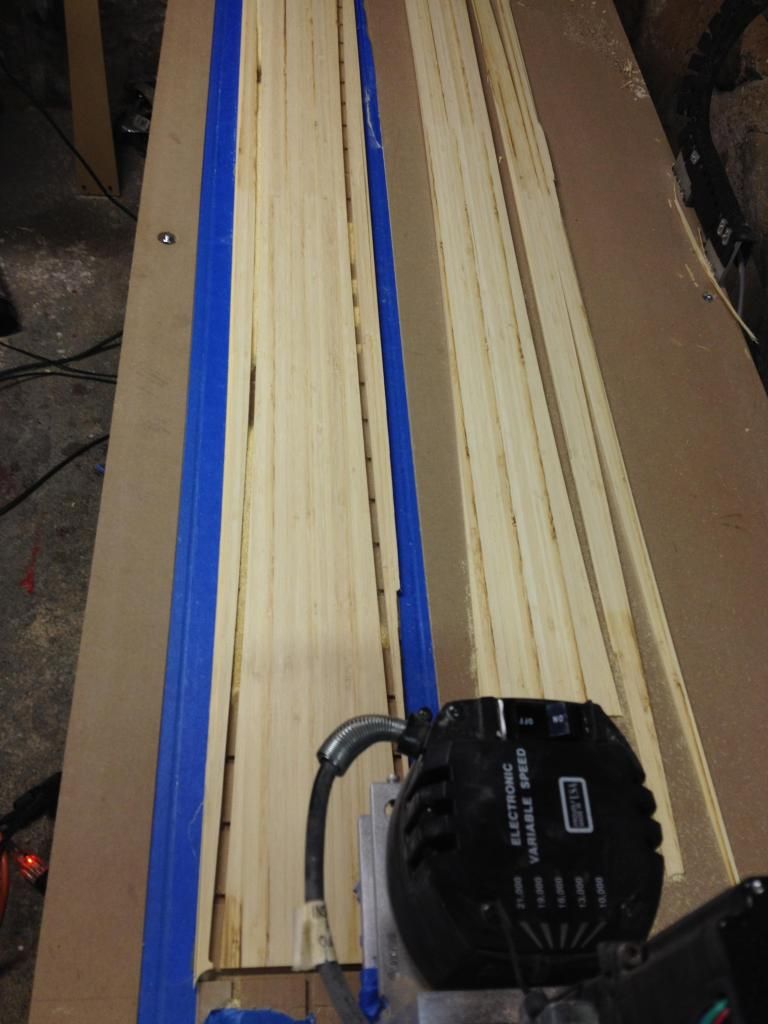
I have figured it out finally... There is some things i need to figure out but mostly it's licked.
1.) how to figure out home. it seems to change every time I shut the computer down. then I would like to save multiple homes depending on the bit that I have in the router. maybe that's the wrong way to do it...
2.) Figure out why when you do an 2D part out side of line why its "off" half the router bit.
okay, anyone want to guess why I have two different profiles here? Free beer to the one that guesses correct ;-)
well I guess I have a core maybe for my wife?
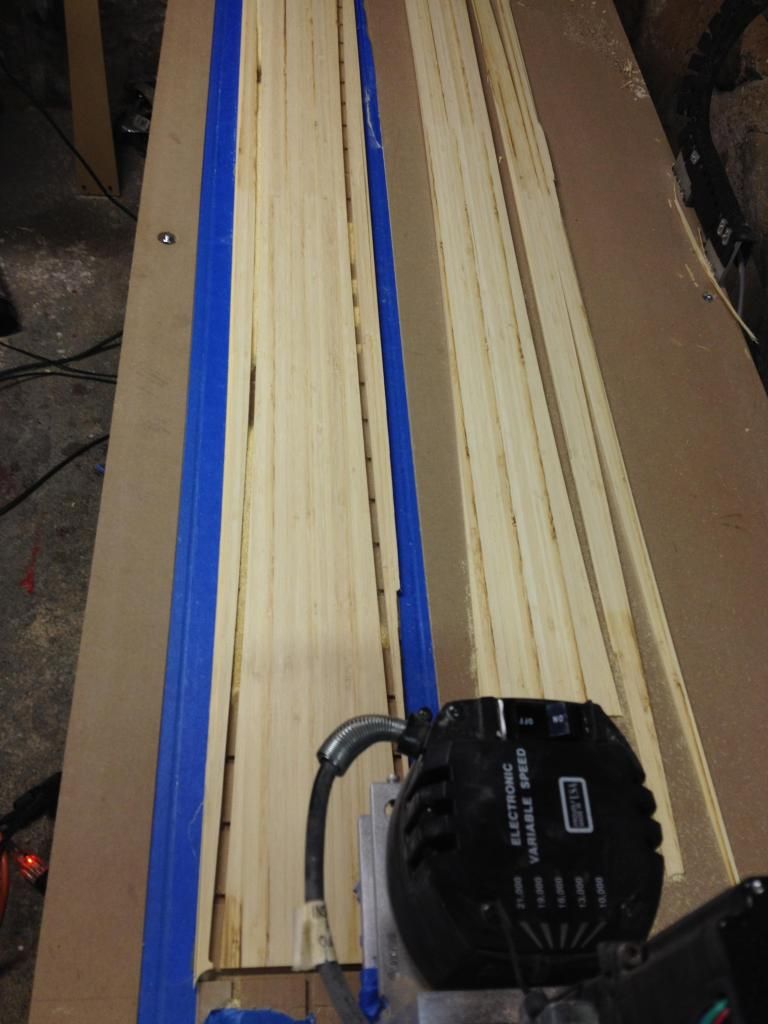
I have figured it out finally... There is some things i need to figure out but mostly it's licked.
1.) how to figure out home. it seems to change every time I shut the computer down. then I would like to save multiple homes depending on the bit that I have in the router. maybe that's the wrong way to do it...
2.) Figure out why when you do an 2D part out side of line why its "off" half the router bit.
okay, anyone want to guess why I have two different profiles here? Free beer to the one that guesses correct ;-)
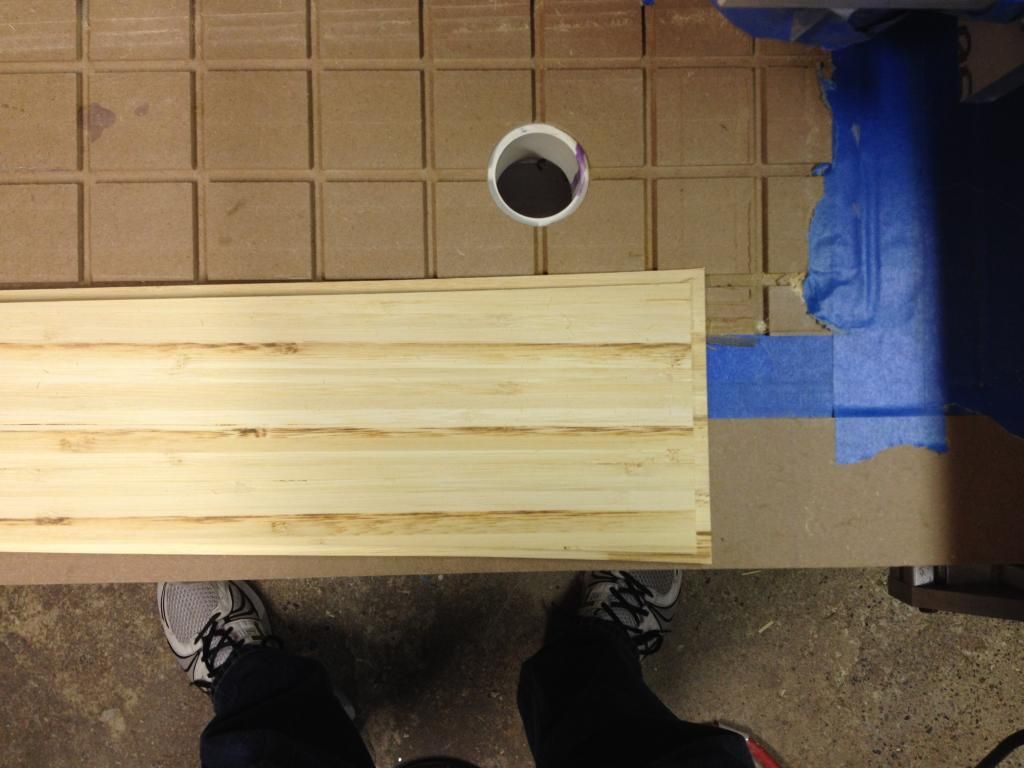
well I guess I have a core maybe for my wife?
Hey gang,
I tried cutting out my base on the CNC with a 1/4" bit and it melted the plastic more than cut it. Have any of you seen this? do I need to go with a larger diameter bit? slower feed rate? slower RPM? Usually when I've cut the base out I get little "chips" of base material.
thinking if I can't get this dialed then I'll cut a MDF template and go back to the old way. I'd rater not go this route.
I tried cutting out my base on the CNC with a 1/4" bit and it melted the plastic more than cut it. Have any of you seen this? do I need to go with a larger diameter bit? slower feed rate? slower RPM? Usually when I've cut the base out I get little "chips" of base material.
thinking if I can't get this dialed then I'll cut a MDF template and go back to the old way. I'd rater not go this route.
-
- Posts: 2204
- Joined: Tue Mar 07, 2006 8:25 pm
- Location: Kenmore, Wa USA
Or you didn't compensate for bit radius? Had the tool path follow the edge of the core exactly, instead of offset by the radius of the bit?
For bases, make yourself a drag knife. Easy, and no mess to clean up when it's done.
As for home... I manually set my home location on every single thing I do, every single time. It's a pain, but it allows more flexibility. If I'm only cutting something small (I use my router for more than just ski stuff), I might do it on the side of the table... or just closer to wherever the spindle happens to be, so I don't have to wait the few seconds it takes to drive it back to center
(lazy) Also with different length bits/endmills/dragknife, I would have to manually set my Z zero anyways, so it's not too much work to do X and Y as well. Also means my parts don't have to be clamped down exactly in the right spot, as long as they are parallel to the table.
For bases, make yourself a drag knife. Easy, and no mess to clean up when it's done.
As for home... I manually set my home location on every single thing I do, every single time. It's a pain, but it allows more flexibility. If I'm only cutting something small (I use my router for more than just ski stuff), I might do it on the side of the table... or just closer to wherever the spindle happens to be, so I don't have to wait the few seconds it takes to drive it back to center

I guess making a drag knife like Twizz suggests is a good idea. Unfortunately I can't figure out how to get the spindle of my CNC not to turn, so I can't use a drag knife (what is it with those huge CNCs and their quirky interfaces?!). I'm still getting great results by using something like this: http://www.toolstoday.com/p-5879-solid- ... -bits.aspx
Twiz and Cornice, close. I did inside of line instead of outside of line... crap-ola. Great explanation on home, this means i'm actually doing something "normal" with mine.
I have made a drag knife just like Donek. However, I have yet to figure out how to do the turns. I found this: http://donektools.com/free-cnc-router-software/links-2/ but I have not tried it yet because I have a MAC (or i'm lazy?).
Chrismp: the spindle of the cnc only turns by friction of the knife. take a look at donek's videos. there is a few videos on there that explain how it works. I too thought the spindle was turning at first, nope. Thanks for the info on the suggested bit. I'll give it a good look.
I have made a drag knife just like Donek. However, I have yet to figure out how to do the turns. I found this: http://donektools.com/free-cnc-router-software/links-2/ but I have not tried it yet because I have a MAC (or i'm lazy?).
Chrismp: the spindle of the cnc only turns by friction of the knife. take a look at donek's videos. there is a few videos on there that explain how it works. I too thought the spindle was turning at first, nope. Thanks for the info on the suggested bit. I'll give it a good look.
Chris -» Can you edit the g-code on your machine ? if yes then just remove the "M3 S-someting" command at the begining of the code (any M3 command for that matter).
the M3 basically says "start the spindle", S sets the spindle RPM.
Another option would be to add the command "M5" (= stop the spindle") to make sure it's not ON.
Skimann 20 -» Tool offsets would have been my first guess. What CAM software do you use ? Is it possible you machined your 2 cores side-to-side, from 2 shapes side-to-side in you CAD ? If so it's possible you had a discrepency between the settings for the 2 shapes. either for tool offsets/machining settings or for the CAD lines themselves, sometime the line "direction" can be the problem -» even with the same CAM settings, one cut will be on the outside, the other on the outside....
To prevent that, what I do is prepare all my machining operations for 1 ski only, then apply a "nesting" operation so the 2nd ski is just a copy of the machining operations, at a different spot on my table. everything is cut exactly the same, just not at the same position.
Regarding the Zeroing (Homing) on the machine, I find it pretty essential. When I start my machine it first "zero" the X and Y axis (machine coordinates). I use DIY proximity switches, about 50 cent each to make them... First adavantage of that is now I can trust the "soft limits" in Mach3 since the machine knows where it is along X and Y axis.
Then I use work coordinates (G54 to G59), or set work-zeros manually depending on the job. With that method I use dowel pins to position my materials on the table, I basically re-use the vacuum holes to position the dowel pins on the table. I can switch between job, change tools, all kind of stuff but wil accurately resume on virtually any job even if I have to remove the stock from the table between 2 operations.
For the Z-Zero, DIY touch plate is the easiest and most useful thing you ca add to your machine !
the M3 basically says "start the spindle", S sets the spindle RPM.
Another option would be to add the command "M5" (= stop the spindle") to make sure it's not ON.
Skimann 20 -» Tool offsets would have been my first guess. What CAM software do you use ? Is it possible you machined your 2 cores side-to-side, from 2 shapes side-to-side in you CAD ? If so it's possible you had a discrepency between the settings for the 2 shapes. either for tool offsets/machining settings or for the CAD lines themselves, sometime the line "direction" can be the problem -» even with the same CAM settings, one cut will be on the outside, the other on the outside....
To prevent that, what I do is prepare all my machining operations for 1 ski only, then apply a "nesting" operation so the 2nd ski is just a copy of the machining operations, at a different spot on my table. everything is cut exactly the same, just not at the same position.
Regarding the Zeroing (Homing) on the machine, I find it pretty essential. When I start my machine it first "zero" the X and Y axis (machine coordinates). I use DIY proximity switches, about 50 cent each to make them... First adavantage of that is now I can trust the "soft limits" in Mach3 since the machine knows where it is along X and Y axis.
Then I use work coordinates (G54 to G59), or set work-zeros manually depending on the job. With that method I use dowel pins to position my materials on the table, I basically re-use the vacuum holes to position the dowel pins on the table. I can switch between job, change tools, all kind of stuff but wil accurately resume on virtually any job even if I have to remove the stock from the table between 2 operations.
For the Z-Zero, DIY touch plate is the easiest and most useful thing you ca add to your machine !
A bad day skiing is always better than a good one at work...
-
- Posts: 2204
- Joined: Tue Mar 07, 2006 8:25 pm
- Location: Kenmore, Wa USA
You want the spindle to turn! My drag knife is nothing more than a carbide drill blank I ground into a blade shape, i stick it in a collet in my spindle, and then let the machine run with the spindle turned off, so it's free to spin. No extra bearings or blade holders needed.chrismp wrote:Unfortunately I can't figure out how to get the spindle of my CNC not to turn
Skimann - I don't do any compensation with my blade, if you're just doing base outlines I don't think you need to. if you start doing multiple colored bases you'll probably want to, although you can get around if if you put a radius on every corner.
-
- Posts: 80
- Joined: Wed Dec 19, 2012 11:00 am
- Location: Kelowna BC
What CAM software are you running? Could maybe try a hard stop after the initialization lines and 'run from here' once the spindle stops, ignoring the check spindle message. Or open the gcode file in text editor and hand bomb out the M03 lines. Should be pretty easy with find/replace, there may be more than the one at the start of the program.
-
- Posts: 2204
- Joined: Tue Mar 07, 2006 8:25 pm
- Location: Kenmore, Wa USA
-
- Posts: 2337
- Joined: Tue Apr 07, 2009 3:26 pm
- Location: Western Mass, USA
- Contact:
Thanks! I'll keep you in mind. If it happens it wont be until after the season. Need to find a home for it.skimann20 wrote:when you finally get one, I'll be more than willing to come over and help you out. :-) i did 9oz CF top and bottom in the srewed up pair and and I love the flex!skidesmond wrote: I'm not ready to attempt CNC yet. Kudos to you for taking a crack at it.
It's amazing how much stiffer CF will make a ski. I've only played around with 9.4 oz uni and it's really really stiff. I used CF in my daughters skis and I'm worried it will be too stiff for her to bend the ski and that was a 3in strip the length of the ski. We'll see...
The software is called twincam and is an interface for the Siemens Sinumerik driver/cam package. I already tried a hard stop...the spindle just starts spinning again. I also tried letting it run without a tool loaded, but that won't work either. There are no M3 lines in the code itself, it gets all the spindle speeds from the tool manager. Unplugging the spindle won't work either. I would have to reprogram or rewire the interface to avoid an error message. I think I'll have to call the support and see if they have a solution.
Hum that's weird.. could you try to mount the drag knife NOT in the spindle collet ? in a sleeve on your Z axis for example. then you leave the spindle running with no tool at minimum speed so there's not much noise...
You'd have to make you "zero" manually but for base cutting with a drag knife the zero precision is not mandatory since the cut is done in one pass with no material repositionning, and your material is almost always quite wider and longer than the final cut product.
Just throwing a random idea !
You'd have to make you "zero" manually but for base cutting with a drag knife the zero precision is not mandatory since the cut is done in one pass with no material repositionning, and your material is almost always quite wider and longer than the final cut product.
Just throwing a random idea !
A bad day skiing is always better than a good one at work...