Doing a bit of research - not so interested in the product, well its a maybe. The results regarding pre-treatment are interesting. Presume they are only valid for the product in question:
http://www.epoxyworks.com/26/pdf/Gluing ... _Gflex.pdf
This is interesting:
http://www.adhesives.org/Portals/0/adhe ... es.org.pdf
UHMW Bonding
Moderators: Head Monkey, kelvin, bigKam, skidesmond, chrismp
-
- Posts: 132
- Joined: Fri Sep 11, 2009 6:13 am
- Location: germany
hey,
i did some research but could nt really find what im looking for...
there s a lot about the chemical aspect of bonding sidewalls but i m just looking for a good solution to attach them to the core.
my method:
im trimming the core planks to 15mm thickness and cut the sidecut of the core with a stencil and a router (flush trim cutter). after that i attach the abs sidewalls (also 15mm thickness)with clamps on the core.
i use a combination of five 4 way clamps (pictur below) and two or three normal F-clamps on a core of 120-135cm
Problems: the 4 way clamps are best applicaple for 18mm thickness upward, the f-clamps are difficult to adjust on a 15mm plank...
when everything is dried well, i profile the core/sidewall plank via router bridge. using the router i sometimes hit the sidewall from the side facing the wood, thats connected with a lot of work re-attaching the splitters or a new peace of abs.
4-way clamp:

how do you attch sidewalls even shaped to 2mm tip/tail thickness??
i did some research but could nt really find what im looking for...
there s a lot about the chemical aspect of bonding sidewalls but i m just looking for a good solution to attach them to the core.
my method:
im trimming the core planks to 15mm thickness and cut the sidecut of the core with a stencil and a router (flush trim cutter). after that i attach the abs sidewalls (also 15mm thickness)with clamps on the core.
i use a combination of five 4 way clamps (pictur below) and two or three normal F-clamps on a core of 120-135cm
Problems: the 4 way clamps are best applicaple for 18mm thickness upward, the f-clamps are difficult to adjust on a 15mm plank...
when everything is dried well, i profile the core/sidewall plank via router bridge. using the router i sometimes hit the sidewall from the side facing the wood, thats connected with a lot of work re-attaching the splitters or a new peace of abs.
4-way clamp:

how do you attch sidewalls even shaped to 2mm tip/tail thickness??
-
- Posts: 191
- Joined: Thu Mar 22, 2007 8:00 am
I use a 4 way clamping system for cores and sidewalls, but not anything fancy like those clamps.
I use about 5-6 F clamps for a core of about 180cm as horizontal pressure with alternating home made vertical compression clamps.
I basically took some full 1 inch thick pine boards and cut them about 7 inches long by ~2 inches wide and drilled out holes to put carriage bolt in, 1 in each end. I then use a small section of rubber tubing that gets placed under the top section of the clamp. This ensures that each individual piece of material gets pressure in case there are small variances in material thickness. These clamps cost me about 5 dollars to make to buy the hardware. The wood was scrap I had and the tubing was left over window weather stripping. The stuff sticking out is press and seal food wrap to prevent the wood glue from sticking to the clamps.
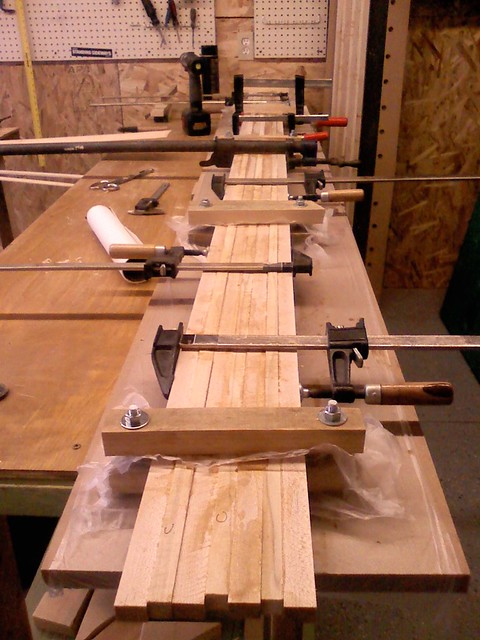
I precut the sidewalls to match the core thickness but running them though the planer. then I attach the sidewalls at full thickness after cutting the horizontal dimensions into the core.
The base side gets flattened in the planer and then edge channels get routed in. Then everything goes onto the jig and run though the planer for final profiling.
I use about 5-6 F clamps for a core of about 180cm as horizontal pressure with alternating home made vertical compression clamps.
I basically took some full 1 inch thick pine boards and cut them about 7 inches long by ~2 inches wide and drilled out holes to put carriage bolt in, 1 in each end. I then use a small section of rubber tubing that gets placed under the top section of the clamp. This ensures that each individual piece of material gets pressure in case there are small variances in material thickness. These clamps cost me about 5 dollars to make to buy the hardware. The wood was scrap I had and the tubing was left over window weather stripping. The stuff sticking out is press and seal food wrap to prevent the wood glue from sticking to the clamps.
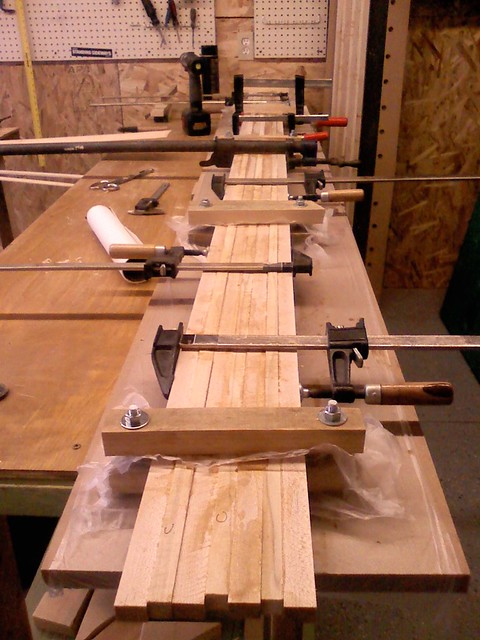
I precut the sidewalls to match the core thickness but running them though the planer. then I attach the sidewalls at full thickness after cutting the horizontal dimensions into the core.
The base side gets flattened in the planer and then edge channels get routed in. Then everything goes onto the jig and run though the planer for final profiling.
Fighting gravity on a daily basis
www.Whiteroomcustomskis.com
www.Whiteroomcustomskis.com