Accurate, replicable method of measuring ski flex (long)
Moderators: Head Monkey, kelvin, bigKam, skidesmond, chrismp
- White Thrash Wednesday
- Posts: 30
- Joined: Wed Dec 15, 2010 1:42 pm
- Location: Stockholm, Sweden
- White Thrash Wednesday
- Posts: 30
- Joined: Wed Dec 15, 2010 1:42 pm
- Location: Stockholm, Sweden
- White Thrash Wednesday
- Posts: 30
- Joined: Wed Dec 15, 2010 1:42 pm
- Location: Stockholm, Sweden
Hi JP!jpelentrides123 wrote:hi there
i am a 3rd engineer at Exeter university and am interested in measuring stiffness in snowboards and ski's.
This forum seems to be the best i have found.
Can anyone give me some advice about where to start?
Cheers JP
Here is how I did it: Two types of tests. One for bending stiffness and one for torsional stiffness. The testing methods are quite simple but really effective (at least according to me) and good for comparing skis. The results can also be used to model the core thickness and lay ups for a concept ski in a FE program such as Abaqus or Ansys. So if you have a ski you like, you can build one with silmular/same flex pattern and torsion. Sounds good? Here´s a short explanation:
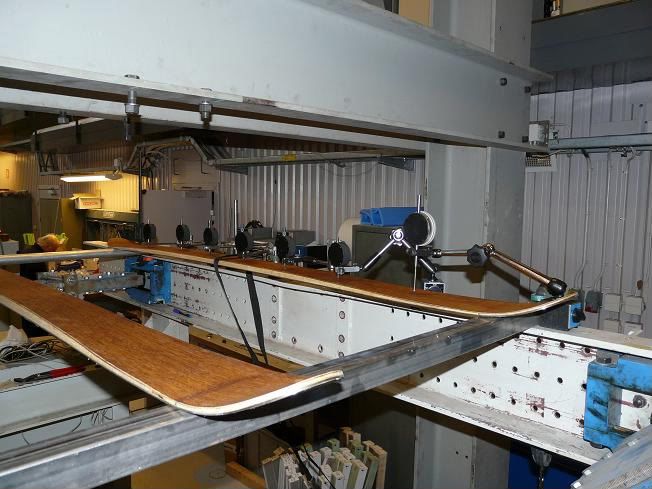
Picture of the three point bending rig. The ski is thought of as a simply supported beam. The supports are located just at the beginning of the curvature of the tip and tail. The distance between the supports is the same as the running length (1.615 m in my case) . Seven digital gauges measure the deflection along the running base at evenly spaced intervals (0.2 m) beginning from the support at the tail. The last interval at the nose support was 0.215 m. A lashing strap with a weight was used for loading at the boot center ( 36 N). It can be seen at the middle of the right ski. The gauges are reset when the ski is at rest, thus eliminating the influence of camber when compared to the result after loading.
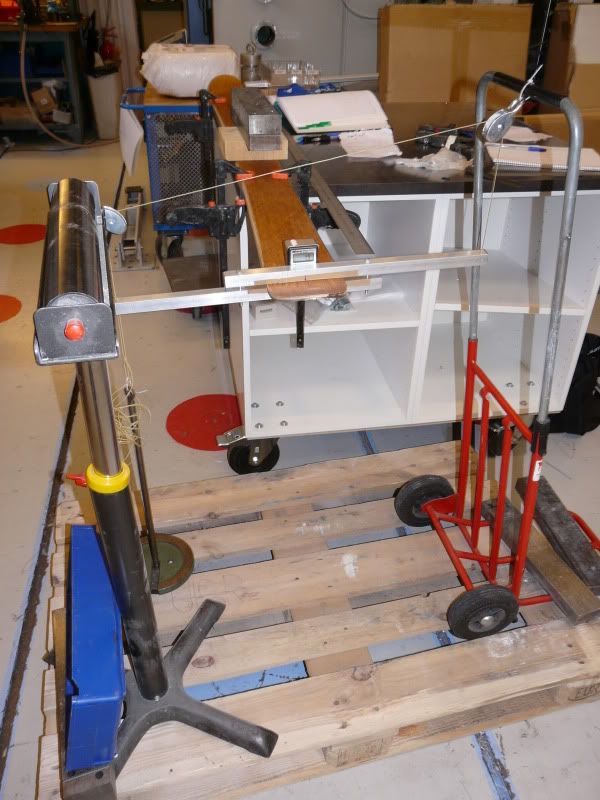
Clamped ski in the torsion rig. The digital angle gauge is seen at the tip of the ski. The ski is clamped where the front binding is usually mounted. The angle after loading are measured at 0.1 m intervals until the curvature of the tip. The loading was the sam as for the deflection (36 N) and the lever arms are 0.3 m on each side from the center of the ski.
The results can then be plotted, and looks something like this:
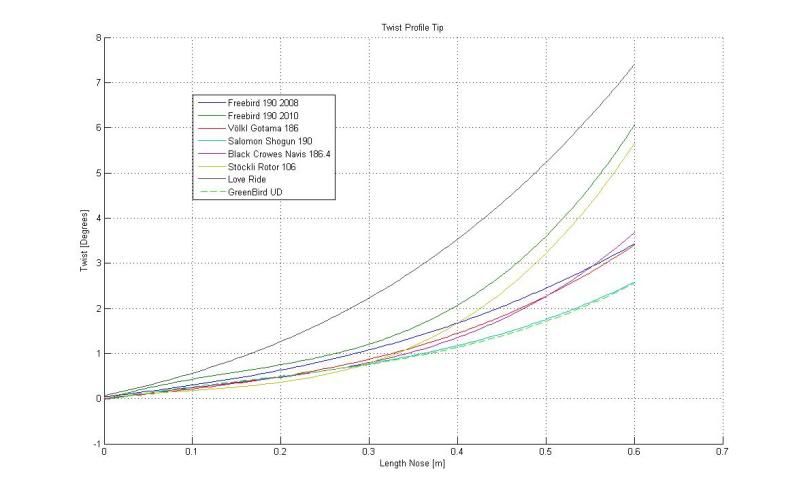
For the twisting profile
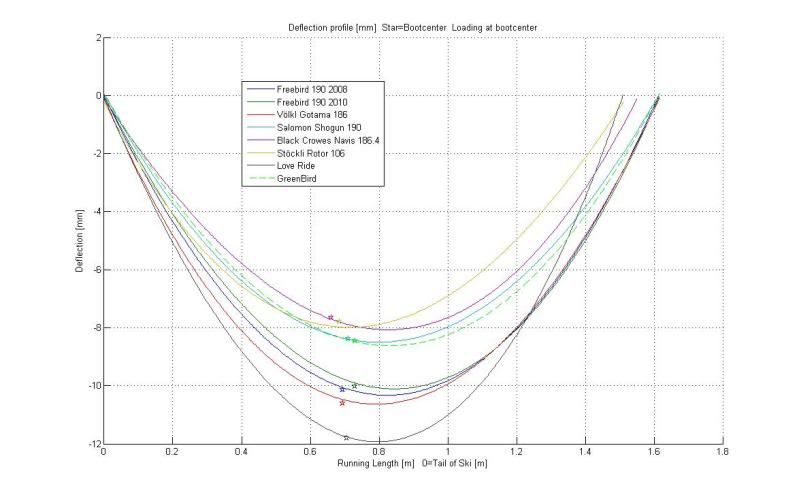
For the bending profile.
The "GreenBird" is the ski I built from the results from the other skis. I overshot the bending stiffnes a bit due to having a little to low E1 modulus for the bamboo core during FE modeling. According to the charts it ended up being a Salomon Shogun instead of a Völkl Gotama which was intended ;-) It still turned out to be a great ski!
Hope this helps!
/Johan
Making skiing Green.
-
- Posts: 53
- Joined: Tue Nov 09, 2010 11:47 am
nice!
Did you test the skis on the slopes as well as in the test bench? how do you feel that the torsional flex compares to the ski performance?
Do you use ANSYS? I use ANSYS, but i strugle to reproduce the results from my tests in ANSYS. have you found a good way of measuring flex in ANSYS /ABAQUS?, I ended up just exporting the cordinates to an excel model i made, and then compare with other skis there.
Great to see other nordic builders here, with a scientific approach!
Did you test the skis on the slopes as well as in the test bench? how do you feel that the torsional flex compares to the ski performance?
Do you use ANSYS? I use ANSYS, but i strugle to reproduce the results from my tests in ANSYS. have you found a good way of measuring flex in ANSYS /ABAQUS?, I ended up just exporting the cordinates to an excel model i made, and then compare with other skis there.
Great to see other nordic builders here, with a scientific approach!
- White Thrash Wednesday
- Posts: 30
- Joined: Wed Dec 15, 2010 1:42 pm
- Location: Stockholm, Sweden
Hej Eirik!
Actually I have not tested the other skis in the slopes, all benchmarking were done in september/october :-s. I have tested the "GreenBird" ski and as I percieved it, it had VERY good acceleraton out of the turns and really good edge grip. I thought of it as a bit stiff in bending (I am 100 kg!) and you need to have good technique, but if you put in the work it rewards you with a super fun ski to ride. I made another GreenBird with the same lay-up and only making the core slightly thinner in some places. It ended up being really easy to ride, sort of "surfish" but lacked the kick/acc out of the turns.
Testing skis in the slopes is very subjective I think, with a lot of parameters you cant measure/control such as snow quality, temperature, rider technique, rider weight.... By doing controlled lab benchmarking you get some numbers to compare the skis among each other. It is also not so easy as to say that a stiffer ski will have better grip than a soft. All parameters are linked such as dampening, stiffness, weight, torsion and so forth which makes ski design quite difficult, but thats the fun part! :-)
In general (and simplyfied) from a scientific approach these are the results from a doctoral thesis of sports equipment/human interaction:
The experiment only looked at bending stiffnes and torsional stiffnes as parameters:
If we have four pair of identical looking skis (s/s),( s/h) ,(h/s) ,(h/h)
were s=soft, h=hard/high and (s/h) means (soft bending/high torsion) We let a group of advanced and expert (semi pro racers) skiers do blind tests of all of the skis. Which combo of flex/torsion will they prefer when they dont now what they are skiing?
The conclusion was that the skiers prefered a ski soft in bending with high torsional regidity (s/h). Torsional rigidity was coupled to good edge grip. So the 1000$ question? How soft is soft and how high is high? From what I read the Gotama has goot really good reviews in skiing magazines around the world, so it seem to be a good start. The Head Johnny 94 another ski I have tested that have gotten good reviews in Sweden. It has a maximum deflection of 11.25mm (Gotama~10.60mm) and max twist of the tip 6.6 deg (Gotama~3.4 deg)
The skis in the charts called "FreeBird" are built by friends of mine, three ex-ski bums. They have designed their skis from a "trial and error" approach: first building, then testing them in the slopes. Re-design, build, ride... It took them a few years and a lot of prototypes to find the lay-up and core profile that made up a ski they really liked. I guess this is why ski building is not the most inexpensive hobby? ;-) The result? A ski (FreeBird 2008) that measured really close to the Völkl Gotama which happened to be one of their favorite skis!
I used Abaqus (used by my school) for all my modeling. I hope to be able to get HyperMesh in the near future. Eirik, for the Ansys modeling what are your objectives? To calculate core thickness for a certain lay-up? I don´t really understand Endres work but are you considering that the ski is a sandwich construction where the regular I=(widthxheight^3)/12 don´t apply? This may be a stupid question, in that case, Sorry!
/Johan
Actually I have not tested the other skis in the slopes, all benchmarking were done in september/october :-s. I have tested the "GreenBird" ski and as I percieved it, it had VERY good acceleraton out of the turns and really good edge grip. I thought of it as a bit stiff in bending (I am 100 kg!) and you need to have good technique, but if you put in the work it rewards you with a super fun ski to ride. I made another GreenBird with the same lay-up and only making the core slightly thinner in some places. It ended up being really easy to ride, sort of "surfish" but lacked the kick/acc out of the turns.
Testing skis in the slopes is very subjective I think, with a lot of parameters you cant measure/control such as snow quality, temperature, rider technique, rider weight.... By doing controlled lab benchmarking you get some numbers to compare the skis among each other. It is also not so easy as to say that a stiffer ski will have better grip than a soft. All parameters are linked such as dampening, stiffness, weight, torsion and so forth which makes ski design quite difficult, but thats the fun part! :-)
In general (and simplyfied) from a scientific approach these are the results from a doctoral thesis of sports equipment/human interaction:
The experiment only looked at bending stiffnes and torsional stiffnes as parameters:
If we have four pair of identical looking skis (s/s),( s/h) ,(h/s) ,(h/h)
were s=soft, h=hard/high and (s/h) means (soft bending/high torsion) We let a group of advanced and expert (semi pro racers) skiers do blind tests of all of the skis. Which combo of flex/torsion will they prefer when they dont now what they are skiing?
The conclusion was that the skiers prefered a ski soft in bending with high torsional regidity (s/h). Torsional rigidity was coupled to good edge grip. So the 1000$ question? How soft is soft and how high is high? From what I read the Gotama has goot really good reviews in skiing magazines around the world, so it seem to be a good start. The Head Johnny 94 another ski I have tested that have gotten good reviews in Sweden. It has a maximum deflection of 11.25mm (Gotama~10.60mm) and max twist of the tip 6.6 deg (Gotama~3.4 deg)
The skis in the charts called "FreeBird" are built by friends of mine, three ex-ski bums. They have designed their skis from a "trial and error" approach: first building, then testing them in the slopes. Re-design, build, ride... It took them a few years and a lot of prototypes to find the lay-up and core profile that made up a ski they really liked. I guess this is why ski building is not the most inexpensive hobby? ;-) The result? A ski (FreeBird 2008) that measured really close to the Völkl Gotama which happened to be one of their favorite skis!
I used Abaqus (used by my school) for all my modeling. I hope to be able to get HyperMesh in the near future. Eirik, for the Ansys modeling what are your objectives? To calculate core thickness for a certain lay-up? I don´t really understand Endres work but are you considering that the ski is a sandwich construction where the regular I=(widthxheight^3)/12 don´t apply? This may be a stupid question, in that case, Sorry!
/Johan
Making skiing Green.
-
- Posts: 2337
- Joined: Tue Apr 07, 2009 3:26 pm
- Location: Western Mass, USA
- Contact:
WTW - great job on the technical data. I totally agree about the subjectivity of testing skis.... It all depends who's on them and their skiing ability. I also agree on with the s/h type of ski, a ski that will bend (and pop back) to accelerate out of turns but torsionally stiff for that edge bite when needed. To me that makes a great (USA) east coast ski and is the type of ski I'm striving for. Great job!
- White Thrash Wednesday
- Posts: 30
- Joined: Wed Dec 15, 2010 1:42 pm
- Location: Stockholm, Sweden
Hej!
OAC - Actually I am a M.Sc student in Vehicle Engineering, specializing in Lightweight Structures at KTH (Royal Institute of Technology) in Stockholm, Sweden. My master thesis was on Applied Biobased Composite Design in Sports Applications. In English: Designing and building skis made from vegetables ;-) The "GreenBird" in the charts above was one of the bastard children of this madness. Hopefully I´ll start doing some skis this winter, trying to start my own little company building Eco-friendly and Green skis that kicks every "Eco Ski" on the markets ass... The goal is a ski of at least 90% by weight of renewable resources, the GreenBird is something like 80% so the quest continues!
skidesmond- It just hit me... WTW=Weight Watchers. Didn´t think of that. It´s kind of funny since I study Light Weight Structures
I´m not exactly skinny either (100 kg), so maybe WTW needs some WTW
I´m already an Airhead so not to much weight to save there...
/Johan
OAC - Actually I am a M.Sc student in Vehicle Engineering, specializing in Lightweight Structures at KTH (Royal Institute of Technology) in Stockholm, Sweden. My master thesis was on Applied Biobased Composite Design in Sports Applications. In English: Designing and building skis made from vegetables ;-) The "GreenBird" in the charts above was one of the bastard children of this madness. Hopefully I´ll start doing some skis this winter, trying to start my own little company building Eco-friendly and Green skis that kicks every "Eco Ski" on the markets ass... The goal is a ski of at least 90% by weight of renewable resources, the GreenBird is something like 80% so the quest continues!
skidesmond- It just hit me... WTW=Weight Watchers. Didn´t think of that. It´s kind of funny since I study Light Weight Structures


/Johan
Making skiing Green.
-
- Posts: 53
- Joined: Tue Nov 09, 2010 11:47 am
Johan,
Really interesting info. Do you have that PHD thesis? would be interesting to read. Could you maybe send it to me (eirik_lh (at) hotmail.com )?
Regarding ANSYS, first i was just trying to verify my my test results, which i got when breaking a bunch of samples. I got pretty good coherence with "hand calculations" (for deformation, +- 10 % maybe) but the ANSYS model was way of on deformation. so i kind of have to work a little bit more on that model. I tried using different solid, shell and Solid-shell elements specifically developed for composites. And i figured i would get about the same results with all of them, but for one of the element types i actually got twice the deformation. I think I really have to look into the theory behind these element types. The ultimate goal is to make an accurate FEM model so that one can optimize material use in skis. So far I've used two models, one micro mechanics model, simulating each fiber in the matrix material, to find the laminate properties( longitudal, and transverse modulus, Poisons ratio and shear modulus), and then a meso scale model (simulating the orthotropic laminates and core material).
For practical design my Excel spread sheet seem to work fine now, i just got the first pair out of the press and it seem to fit with the designed stiffness. I made a conversion from the N/mm numbers Endre has measured (see the tread First Ski design here, look at it and see if you agree...), I dont think it is possble to convert the SFI uless Endre tells us how he calculates the SFI numbers, I am thinking its just a statistical formula based on his "database".
I also just wrote a thesis about ski building and i am happy to share it with anyone that understands Norwegian. ( I am a 5th year student at UMB out side Oslo studying mechanical engineering/product development)
Really interesting info. Do you have that PHD thesis? would be interesting to read. Could you maybe send it to me (eirik_lh (at) hotmail.com )?
Regarding ANSYS, first i was just trying to verify my my test results, which i got when breaking a bunch of samples. I got pretty good coherence with "hand calculations" (for deformation, +- 10 % maybe) but the ANSYS model was way of on deformation. so i kind of have to work a little bit more on that model. I tried using different solid, shell and Solid-shell elements specifically developed for composites. And i figured i would get about the same results with all of them, but for one of the element types i actually got twice the deformation. I think I really have to look into the theory behind these element types. The ultimate goal is to make an accurate FEM model so that one can optimize material use in skis. So far I've used two models, one micro mechanics model, simulating each fiber in the matrix material, to find the laminate properties( longitudal, and transverse modulus, Poisons ratio and shear modulus), and then a meso scale model (simulating the orthotropic laminates and core material).
For practical design my Excel spread sheet seem to work fine now, i just got the first pair out of the press and it seem to fit with the designed stiffness. I made a conversion from the N/mm numbers Endre has measured (see the tread First Ski design here, look at it and see if you agree...), I dont think it is possble to convert the SFI uless Endre tells us how he calculates the SFI numbers, I am thinking its just a statistical formula based on his "database".
I also just wrote a thesis about ski building and i am happy to share it with anyone that understands Norwegian. ( I am a 5th year student at UMB out side Oslo studying mechanical engineering/product development)
-
- Posts: 2337
- Joined: Tue Apr 07, 2009 3:26 pm
- Location: Western Mass, USA
- Contact:
White Thrash Wednesday wrote:......
skidesmond- It just hit me... WTW=Weight Watchers. Didn´t think of that. It´s kind of funny since I study Light Weight StructuresI´m not exactly skinny either (100 kg), so maybe WTW needs some WTW
I´m already an Airhead so not to much weight to save there...
/Johan

SFI is a statistically based flex index. SFI can be calculated from a row of 14 or 16 measured N/mm numbers in linked 10cm segments. The formula is the result of years of work and not a thing i could paste in a forum. But if you give me the length of your ski and 16 N/mm figures i will give you the SFI.Eirik Hanes wrote:I dont think it is possble to convert the SFI uless Endre tells us how he calculates the SFI numbers, I am thinking its just a statistical formula based on his "database".
and what does "database" suggest? do you question my work Eirik?
-
- Posts: 53
- Joined: Tue Nov 09, 2010 11:47 am
Not at all, sorry if it came out that way. I guess it just felt weird to use the word database in this context :P
your data has been very useful for me in my ski design process. Just got my first pair out of the press and it seems like the skis came out as predicted, thanks to your data.
Regarding SFI, I was just trying to figure how it works out so that i can calculate the SFI for my own skis and compare it to tests in ski magazines. And then i don't have to ask you everytime i design a new ski
. But i understand that some things are not appropriate to post in forums.
/Eirik
your data has been very useful for me in my ski design process. Just got my first pair out of the press and it seems like the skis came out as predicted, thanks to your data.
Regarding SFI, I was just trying to figure how it works out so that i can calculate the SFI for my own skis and compare it to tests in ski magazines. And then i don't have to ask you everytime i design a new ski

/Eirik
- White Thrash Wednesday
- Posts: 30
- Joined: Wed Dec 15, 2010 1:42 pm
- Location: Stockholm, Sweden
@Eirik
Sorry for my late reply, I have been away on a well needed vacation :-)
My paper was a Master thesis, not a Ph D thesis, but thanks for the interest anyway :-) I don´t think the paper is "officially published" yet, since I just got it cleared by my supervisor. But as soon as it is published, I think it would be OK to send it. The following comments are based on my Abaqus experience: When modelling a ski ("a sandwich structure") you need to take into consideration the different type of elements. If I remember correct some elements don`t support shear forces for example. Also the number of elements through the thickness is important as well as the length/width/height ratio of the elements. I used brick shaped elements. One major issue for me in the beginning of the modelling was getting the right reference system for the composite lay-up. Another pain in the a** that caused some head ache was the reference surface for the composite face sheet. If you are not careful the composite facesheets will end up "inside" the core instead of "on top" of the core. If the composite ends up inside the core, it could explain the large deflection.
If your excel gives you good comparison with the actual skis I say congrats! If it aint broke... Even if you do a perfect model, the output is going to depend on the input values. It´s not that easy to get the proper Youngs modulus for wood or bamboo since it is a living material with large variations in mechanical properties for every piece of wood... When I changed Youngs modulus for bamboo in my model from something like 12.5 GPa (mean test value) to 14 GPa (highest test value) the deflection of the finished ski increased with 50% as shown in the graphs i posted before. You also need to figure out the volume fraction of you composite so you can get the right thickness of the face sheets as input, top sheet, base and steel edges will also affect the bending stiffness... And also of great importance: the boundary conditions... Quite a lot to think about :-)
I can recommend the books by Dan Zenkert: "Foundations of fibre composites" and "An introduction to sandwich structures", (you could probably get them from KTH in Stockholm) Hope this is of some help...
/Johan
Sorry for my late reply, I have been away on a well needed vacation :-)
My paper was a Master thesis, not a Ph D thesis, but thanks for the interest anyway :-) I don´t think the paper is "officially published" yet, since I just got it cleared by my supervisor. But as soon as it is published, I think it would be OK to send it. The following comments are based on my Abaqus experience: When modelling a ski ("a sandwich structure") you need to take into consideration the different type of elements. If I remember correct some elements don`t support shear forces for example. Also the number of elements through the thickness is important as well as the length/width/height ratio of the elements. I used brick shaped elements. One major issue for me in the beginning of the modelling was getting the right reference system for the composite lay-up. Another pain in the a** that caused some head ache was the reference surface for the composite face sheet. If you are not careful the composite facesheets will end up "inside" the core instead of "on top" of the core. If the composite ends up inside the core, it could explain the large deflection.
If your excel gives you good comparison with the actual skis I say congrats! If it aint broke... Even if you do a perfect model, the output is going to depend on the input values. It´s not that easy to get the proper Youngs modulus for wood or bamboo since it is a living material with large variations in mechanical properties for every piece of wood... When I changed Youngs modulus for bamboo in my model from something like 12.5 GPa (mean test value) to 14 GPa (highest test value) the deflection of the finished ski increased with 50% as shown in the graphs i posted before. You also need to figure out the volume fraction of you composite so you can get the right thickness of the face sheets as input, top sheet, base and steel edges will also affect the bending stiffness... And also of great importance: the boundary conditions... Quite a lot to think about :-)
I can recommend the books by Dan Zenkert: "Foundations of fibre composites" and "An introduction to sandwich structures", (you could probably get them from KTH in Stockholm) Hope this is of some help...
/Johan
Making skiing Green.
-
- Posts: 53
- Joined: Tue Nov 09, 2010 11:47 am
Sounds like we've been encountering just about the same problems regarding the finite element model. I think i have worked around the challenges you mention. I think one of my problems is/was that i tried to make a complete model of the Test bench:
http://www.facebook.com/photo.php?pid=1 ... 756470724
http://www.facebook.com/photo.php?pid=1 ... =756470724
with a cylinder pressing down on the composite sandwich. This cylinder lead to problems in both the experiment (the relatively small diameter of the cylinder r=10 mm lead to crushing of the core material) and in the finite element model. In the finite element model i tried to model that the cylinder was actually pressing down on the laminate, but this just lead to singularities and all kind of crap and no convergence in stress. (I got good stiffness data from the experiments, but not for strength). Thanks for mentioning the steel edge as a stiffness contributor, i haven't incorporated that in my spread sheet yet.
I used a micro mechanics model to find the properties of the composite laminates, based on fiber content from my experiments. How did you measure the fiber content? I got quite some variance in the results for fiber volume fraction.
Looking forward to read your paper, and as i said, I'll be happy to shear mine. I'll also look up those books. (I used some good ones to, but cant remember the exact name:P)
Maybe I'll even start looking at the ANSYS model again...
http://www.facebook.com/photo.php?pid=1 ... 756470724
http://www.facebook.com/photo.php?pid=1 ... =756470724
with a cylinder pressing down on the composite sandwich. This cylinder lead to problems in both the experiment (the relatively small diameter of the cylinder r=10 mm lead to crushing of the core material) and in the finite element model. In the finite element model i tried to model that the cylinder was actually pressing down on the laminate, but this just lead to singularities and all kind of crap and no convergence in stress. (I got good stiffness data from the experiments, but not for strength). Thanks for mentioning the steel edge as a stiffness contributor, i haven't incorporated that in my spread sheet yet.
I used a micro mechanics model to find the properties of the composite laminates, based on fiber content from my experiments. How did you measure the fiber content? I got quite some variance in the results for fiber volume fraction.
Looking forward to read your paper, and as i said, I'll be happy to shear mine. I'll also look up those books. (I used some good ones to, but cant remember the exact name:P)
Maybe I'll even start looking at the ANSYS model again...