Page 10 of 12
Posted: Wed Sep 30, 2015 2:38 am
by falls
Great work!
Who is EARL?
Posted: Wed Sep 30, 2015 12:41 pm
by iggyskier
chrismp wrote:Great workspace! I still remember your first batch of skis posted in the journals here...you've come a long way!
Why do you anneal the edges if you don't do full wraps? Still too hard and time consuming to bend on a production basis?
I believe the edge anneal is far more important in regards to proper edge bonding within the curvature of the tip shape than shaping the edge to fit the tip. That is the primary reason we anneal our edges.
That said, we bend our edges within the annealing process at this time. We anneal, then bend a straight edge into shape, then sandblast. The edge still requires minor tweaking before it goes on a base, but this process has proven to be the fastest so far.
Basing & edging remains one of the more labor-intensive processes in the whole production line.
Posted: Wed Sep 30, 2015 12:48 pm
by iggyskier
chrislandy wrote:Nice! It looks like you have a good layout and flow to the space too. How many sqft is the factory?
One of the biggest thing we have been (and continue) to work on is production flow/efficiency and lean manufacturing. We've made a lot of improvements there, but still some improvements to go. Everything flows really nicely now, which makes a big improvement on the production end.
Right now our factory is around 8000 sf (including office).
Posted: Wed Sep 30, 2015 1:29 pm
by iggyskier
skidesmond wrote:Wow!! You've come so far. I can only imagine what the trip has been like. Serious machinery. Kudos! Noticed the kegerator, nice! What's your capacity?
Thanks!
We have a few more additions coming soon - one more double bay press (bringing us to 8 bays total), considering a second CNC, maybe a few other items. We're in pretty good shape on equipment at this time, but a few more things would really help bring that over the top.
Right now, with our current personnel, we average around 60 pairs/week. That said, if we wanted to bring on another 3-4 people, we have the ability to increase that number quite a bit. Right now, our focus is really on maintaining/improving quality, which means trying to manage growth at a reasonable pace.
Posted: Wed Sep 30, 2015 1:43 pm
by iggyskier
falls wrote:Great work!
Who is EARL?
Earl is a mini-press used for pressing test samples. It is actually normally tucked away (the location in those photos is where the newest double bay press will go).
We've been doing tons of peel tests recently (mostly as we brought all of our sidewall manufacturing in-house, so testing both texture and flame, but also to test a number of different epoxies), so that little press definitely helped make that process more efficient.
Posted: Wed Sep 30, 2015 3:55 pm
by MadRussian
nice shop well thought-out.
I surprise in you wood shop you don't use cyclone dust collector attachment. Cyclone substantially increase dust collector efficiency.
Posted: Wed Sep 30, 2015 5:40 pm
by iggyskier
MadRussian wrote:nice shop well thought-out.
I surprise in you wood shop you don't use cyclone dust collector attachment. Cyclone substantially increase dust collector efficiency.
A cyclone DC for the wood room is on the want list, but a few other tools/machines are ahead of it at this time. We run a cyclone in finishing (band saw, router, deflash) and much prefer it, but this was just a much cheaper option to start once the CNC came in. Also, because it only covers 1 machine (CNC), and we run 7" hose the entire length, we don't really have too many DC issues on the CNC.
Right now, wood production upgrades are sort of in a holding pattern until we decide if we think another CNC is going to be required in the coming year or so. If so, we'll definitely need to upgrade to a larger system.
Posted: Wed Sep 30, 2015 5:54 pm
by twizzstyle
Hey Scott, who makes that sandblast cabinet you've got? I'm going to be buying one for my shop at home, the one I'm looking at is a Grizzly but it's red. I'm trying to get as many white tools as I can (for brightness in the shop).
Factory is looking REAL good. Always awesome to see you guys still growing!
Posted: Wed Sep 30, 2015 6:00 pm
by MadRussian
Around here on the craigslist decent size usedcyclone system with patience can be bought under $500. However decent size cyclone attachment to existent system (that's what I have) can be billed probably under $150 in supplies. Mine have 4 inch inlet and 6 inch outlet .....I don't need to run multiple machines at the same time
Not fancy looking but work well
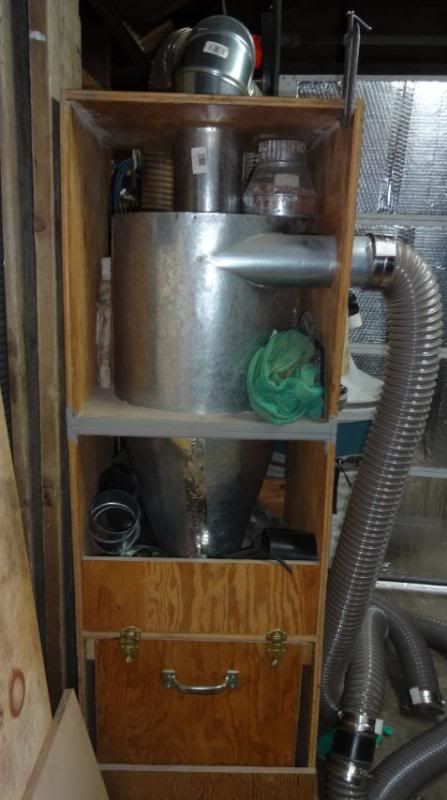
Posted: Thu Oct 01, 2015 12:46 am
by chrislandy
iggyskier wrote:chrislandy wrote:Nice! It looks like you have a good layout and flow to the space too. How many sqft is the factory?
One of the biggest thing we have been (and continue) to work on is production flow/efficiency and lean manufacturing. We've made a lot of improvements there, but still some improvements to go. Everything flows really nicely now, which makes a big improvement on the production end.
Right now our factory is around 8000 sf (including office).
Have you thought about a manufacturing bias business coach? I use one for my main business and it's helped a lot having an impartial overview how things are done, mine has looked at (and reviews frequently) all processes from first contact through to production flow and even marketing
Posted: Thu Oct 01, 2015 7:57 am
by Dream
Sweet Baby Jesus!! That's an amazing space. I just pushed out 35 pairs in my 1 car garage "factory" by myself...what a shit ton of work, took me 2 months...would have been like a few days in your space. Super slick, looks like a ton of thought went into this, nice work!
Posted: Fri Oct 02, 2015 10:25 am
by skidesmond
Kind of as a side note, there's a TV show called 'The Profit' that I've seen a few times. One episode he saved a custom drum making business... That aside, one of the things this drum making shop needed was organization (not implying yours does at all, look awesome!). They set up a 10 step process to produce drums from receiving materials to shipping it out the door. Made a HUGE difference in work flow and production, it was totally organized, some what of Kaizen approach. Even though I'm still working in my very small basement I try to use that approach as much as possible. Great to see you guys making it!
Posted: Mon Oct 05, 2015 8:28 pm
by falls
Hi iggy
Had you thought about adding a second spindle to your current CNC and doing 2 things the same at once?
(rather than a whole extra CNC)
Posted: Wed Oct 07, 2015 4:16 pm
by iggyskier
twizzstyle wrote:Hey Scott, who makes that sandblast cabinet you've got? I'm going to be buying one for my shop at home, the one I'm looking at is a Grizzly but it's red. I'm trying to get as many white tools as I can (for brightness in the shop).
Factory is looking REAL good. Always awesome to see you guys still growing!
Email me and I will track the name down for you. It was expensive (it is a recycling cabinet), but if you want the info just shoot me an email and I will track down the supplier for you.
Posted: Wed Oct 07, 2015 4:18 pm
by iggyskier
chrislandy wrote:
Have you thought about a manufacturing bias business coach? I use one for my main business and it's helped a lot having an impartial overview how things are done, mine has looked at (and reviews frequently) all processes from first contact through to production flow and even marketing
We've had two groups of lean manufacturing consultants come in, which has been really helpful. I've never heard of a manufacturing bias business coach, but I will look into it. It definitely helps to have outsiders come in to review your process from time to time. I'll check it out. Thanks!