RISD sustainable ski exploration
Moderators: Head Monkey, kelvin, bigKam, skidesmond, chrismp
RISD sustainable ski exploration
Hey guys new to posting old to the forum. All the information here is extremely helpful thank you all.
We are two students in the Industrial Design department at Rhode Island School of Design and recently started an independent study on sustainable ski manufacturing. Our goal is to make a sustainable ski that still reflects the quality of a typical production ski. We have finished our first run of skis and hope our advancements are just the tip of the iceberg. We would love as much feed back as possible on both sustainable ideas and methods to improve our ski quality as well as general comments. We based this first pair off of the K2 Pontoons which have the following dimensions 179 long 160-130-120, rockered tip and tail with reverse side cut and flat camber underfoot with regular side cut.
Materials:
4001 base material - Hope to find an alternative
Standard edges
p-tex tip spacer
basalt fiber - Want to go even more sustainable (hemp fibers?)
end grain balsa core with maple side walls - Looking into paulownia
natural wood veneer top sheet
West Systems epoxy- Need other options
finished with 100% Tung Oil
We are two students in the Industrial Design department at Rhode Island School of Design and recently started an independent study on sustainable ski manufacturing. Our goal is to make a sustainable ski that still reflects the quality of a typical production ski. We have finished our first run of skis and hope our advancements are just the tip of the iceberg. We would love as much feed back as possible on both sustainable ideas and methods to improve our ski quality as well as general comments. We based this first pair off of the K2 Pontoons which have the following dimensions 179 long 160-130-120, rockered tip and tail with reverse side cut and flat camber underfoot with regular side cut.
Materials:
4001 base material - Hope to find an alternative
Standard edges
p-tex tip spacer
basalt fiber - Want to go even more sustainable (hemp fibers?)
end grain balsa core with maple side walls - Looking into paulownia
natural wood veneer top sheet
West Systems epoxy- Need other options
finished with 100% Tung Oil
We have now started making a positive to our mold and a fire hose style press. We were unhappy with the pressure achieved in the bag.
We struggled with the final edge cleanup. Used a router with a 25 degree chamfer and ended up cutting into the side of the practice ski. We ended up making an angle jig for the horizontal sander. It worked fine but would like a more accurate system. How do you guys clean up the bases?
We struggled with the final edge cleanup. Used a router with a 25 degree chamfer and ended up cutting into the side of the practice ski. We ended up making an angle jig for the horizontal sander. It worked fine but would like a more accurate system. How do you guys clean up the bases?
So here is a overview of our process
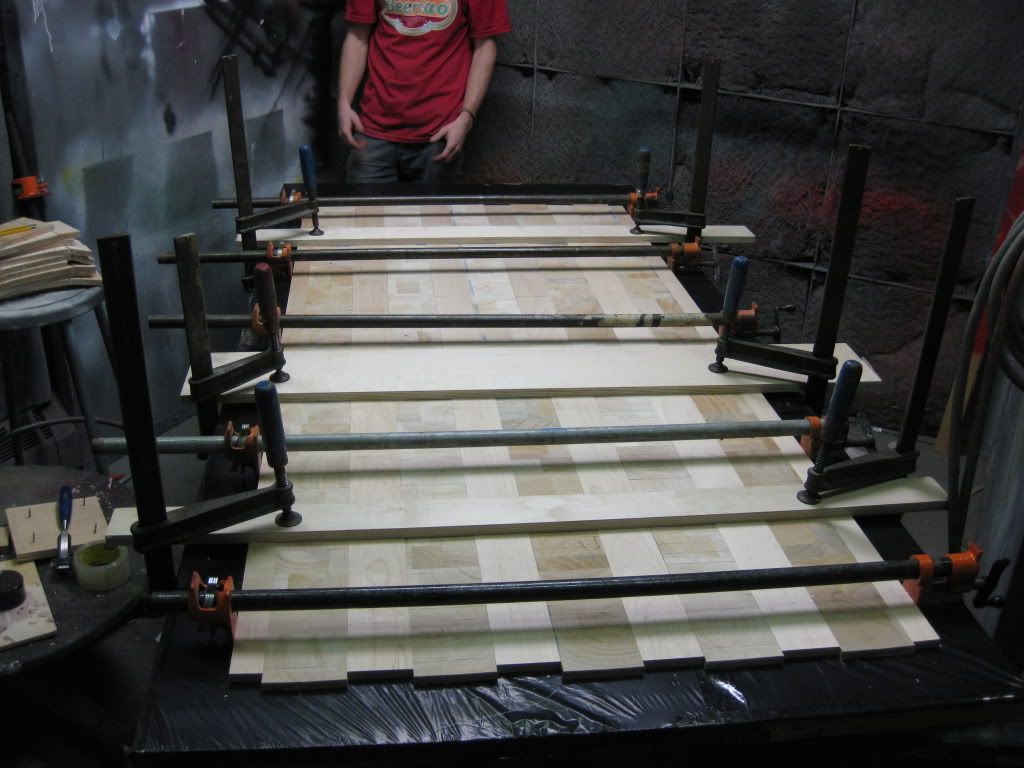
5 Cores Being glued up. 1 practice ski, 2 pairs. End grain balsa core with maple side walls. Balsa is one of the fastest grown plantation plants and has an extremely high compression resistance for its weight.
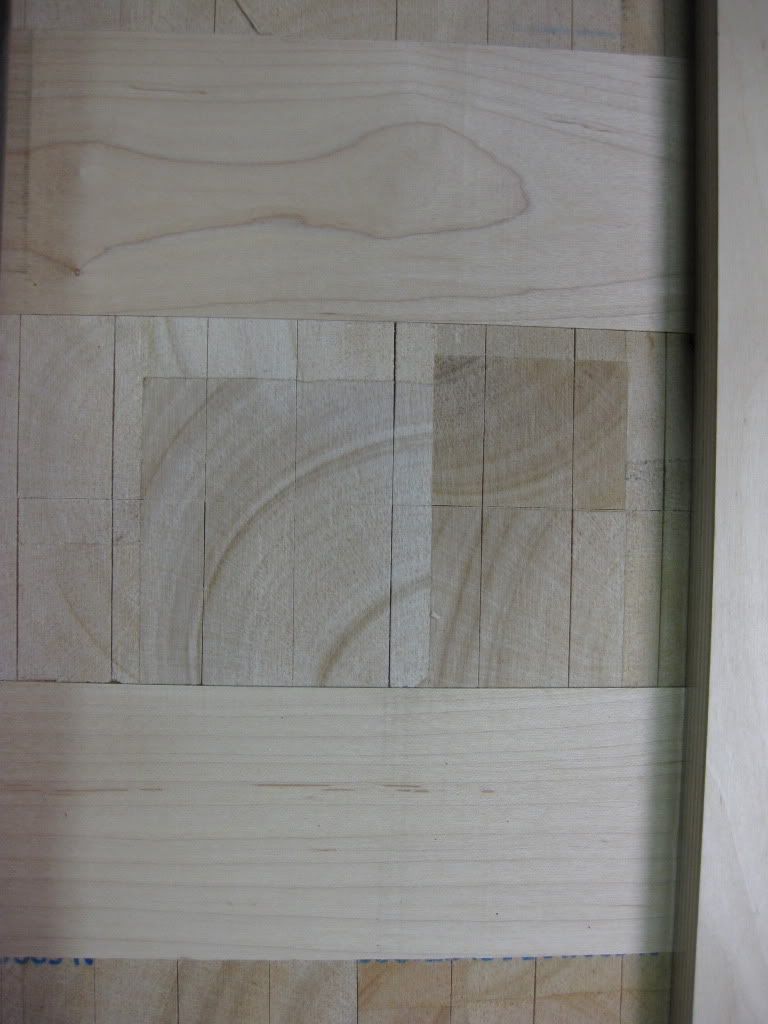
Detail shot
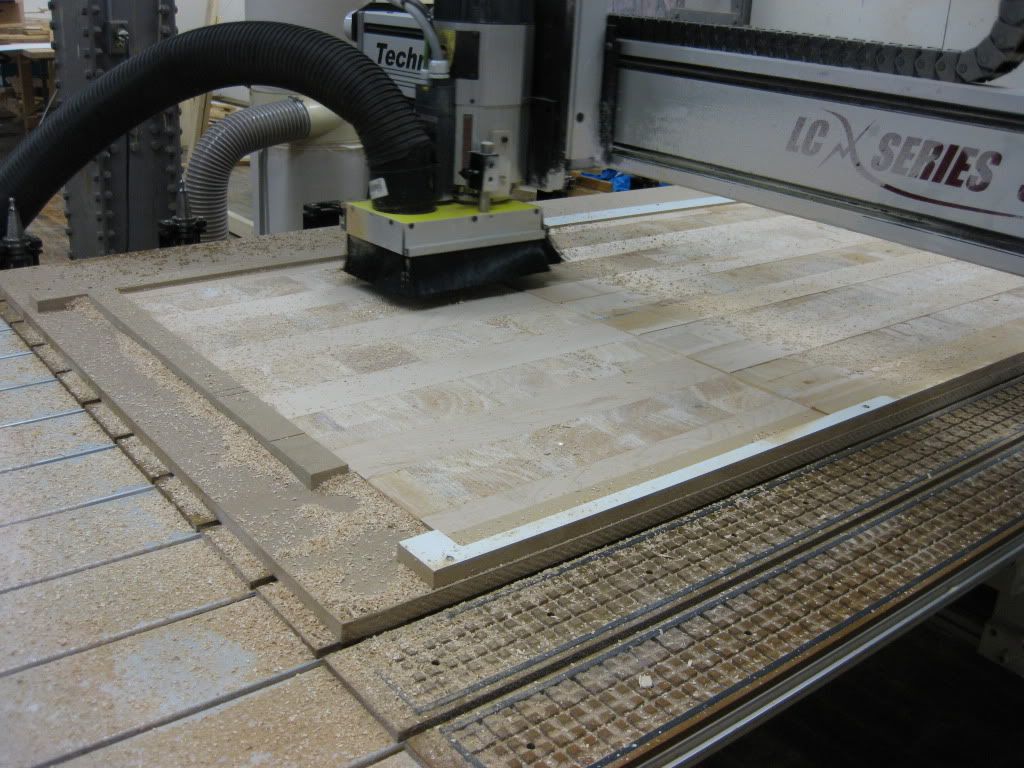
CNC;d the cores. Wont be doing that again! We hope to make a planer jig.
It was incredibly time consuming with lack luster results.
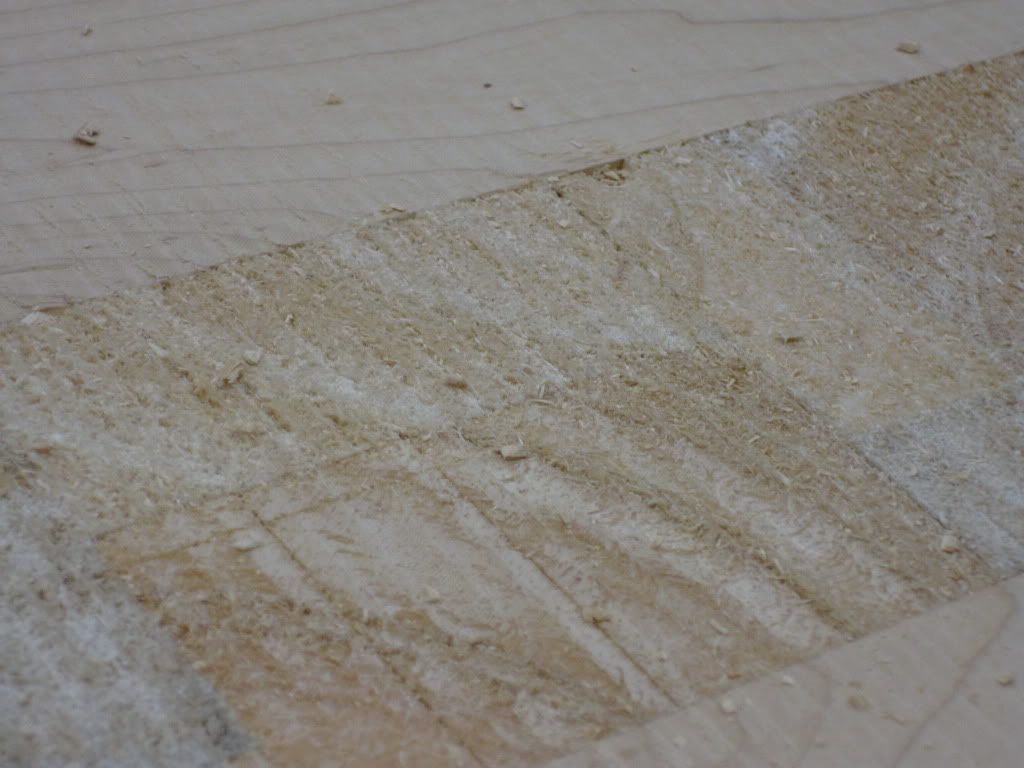
Finish Cut Detail
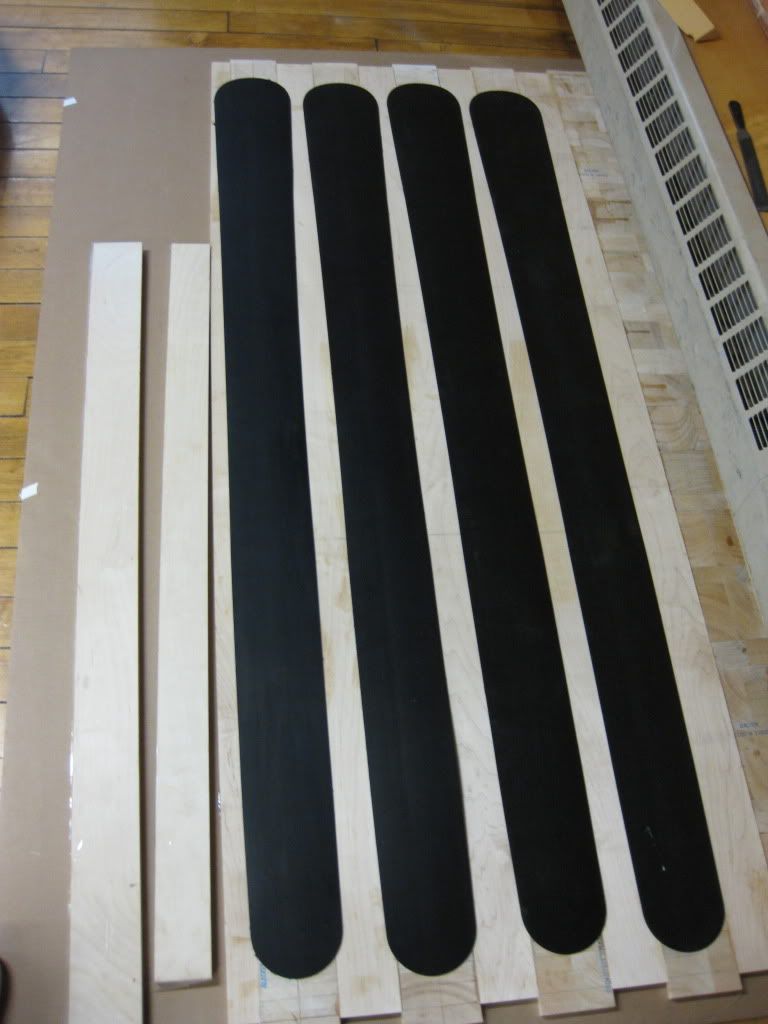
Bases were CNC'd as well, but in the future we will use a router template.

Cutting individual cores.
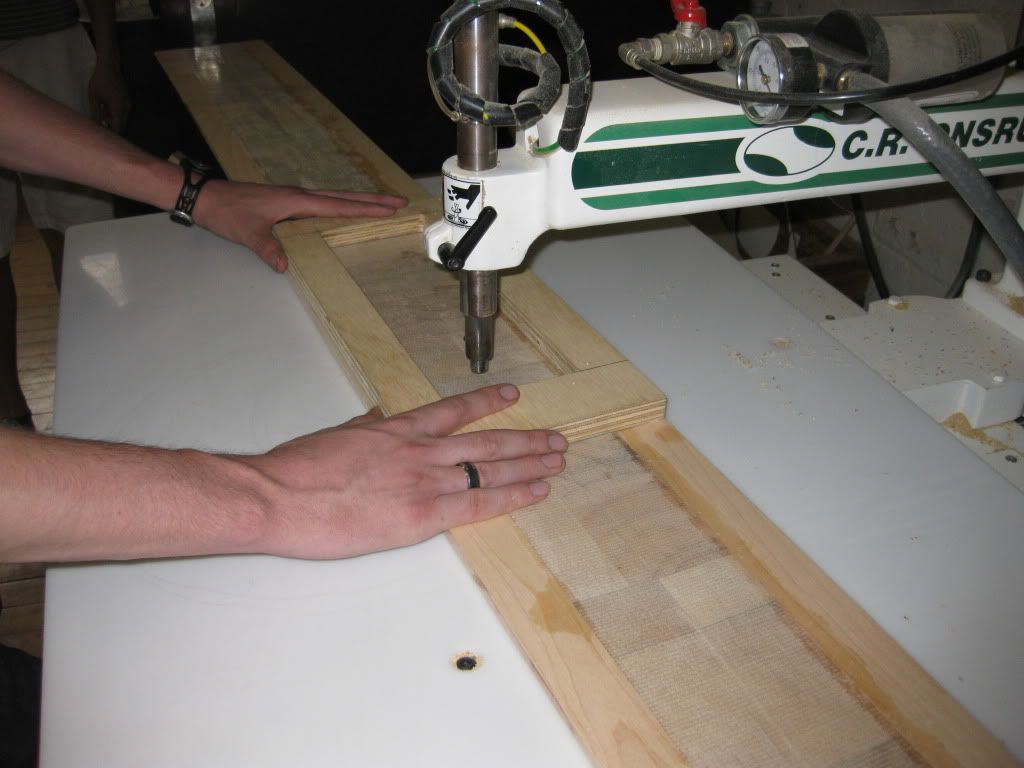
Because the Balsa has no pull out strength we had to rout out an area to place basalt fiber for the bindings to screw into.
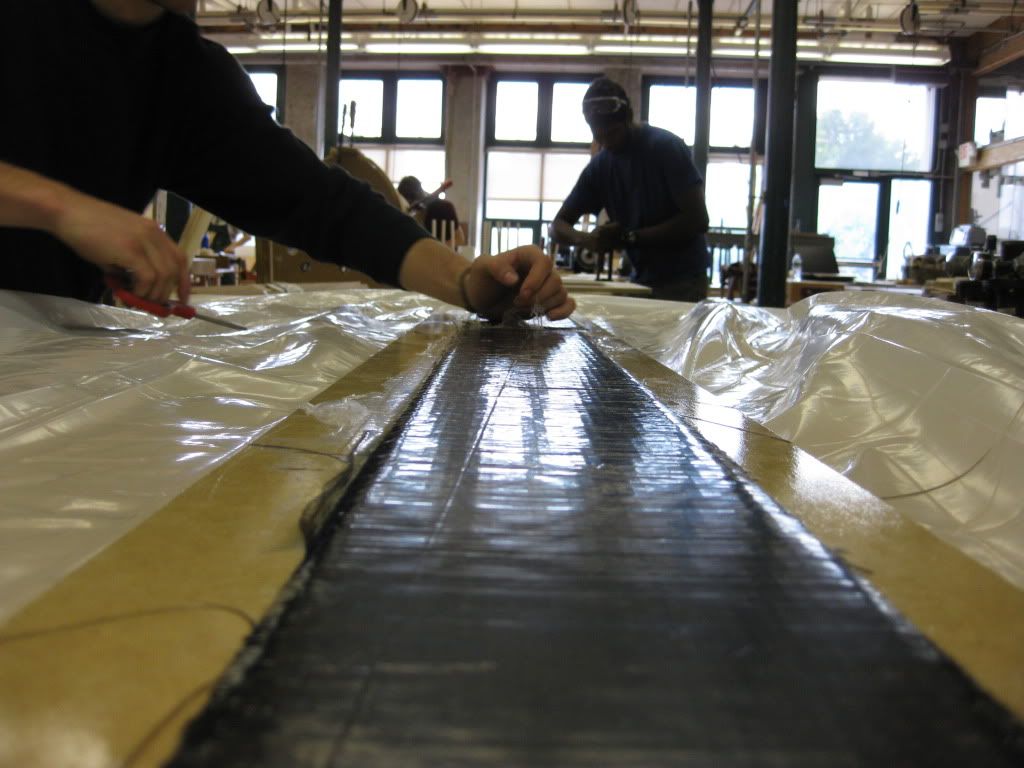
Basalt binding insert
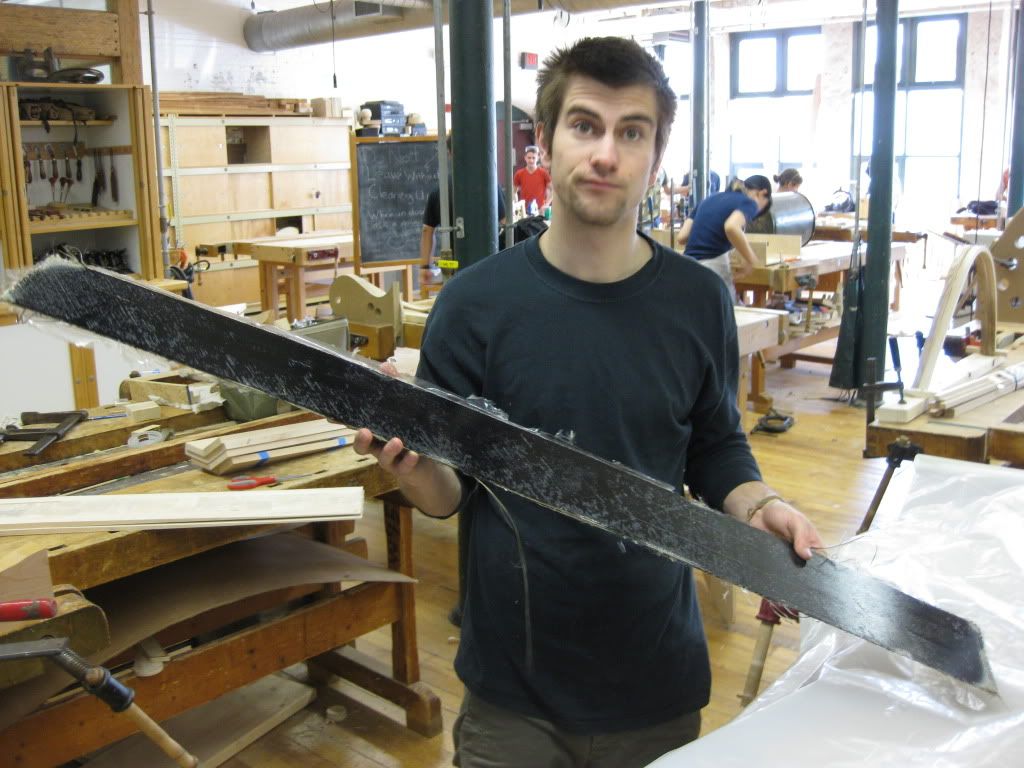
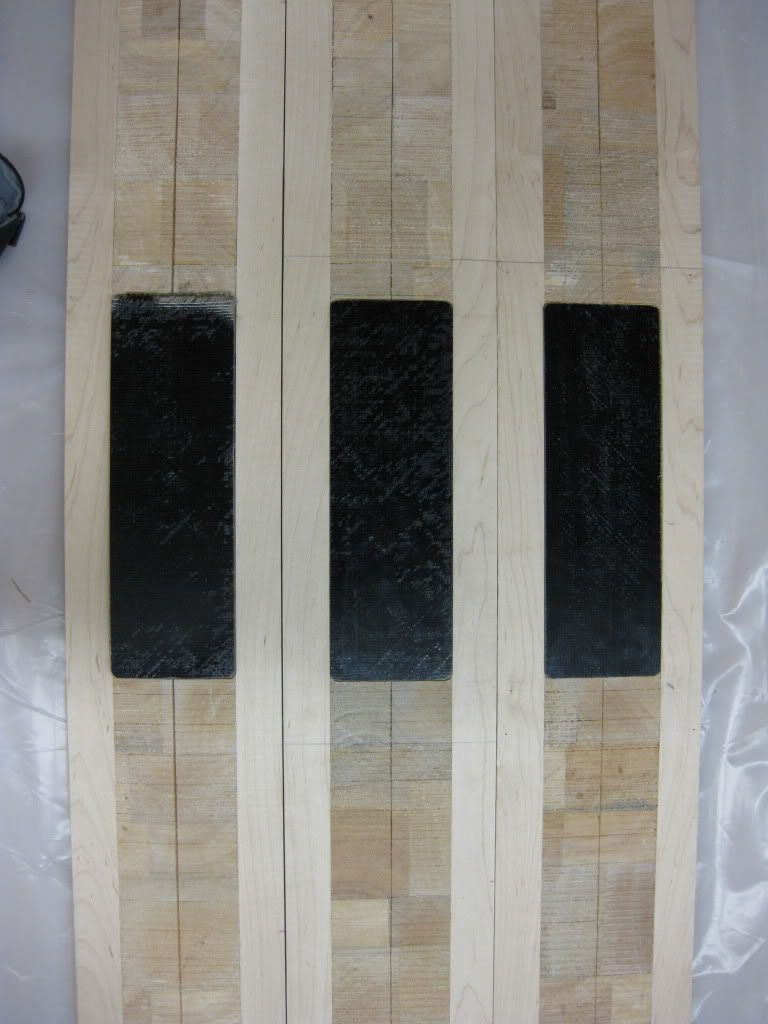
Core with Basalt insert
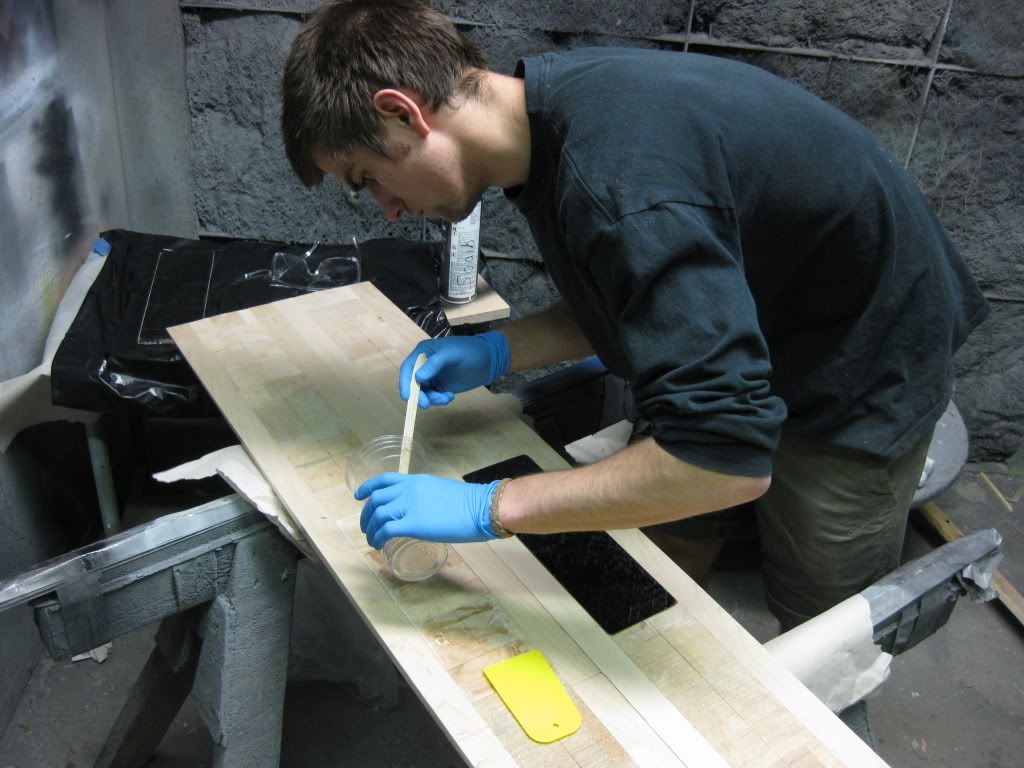
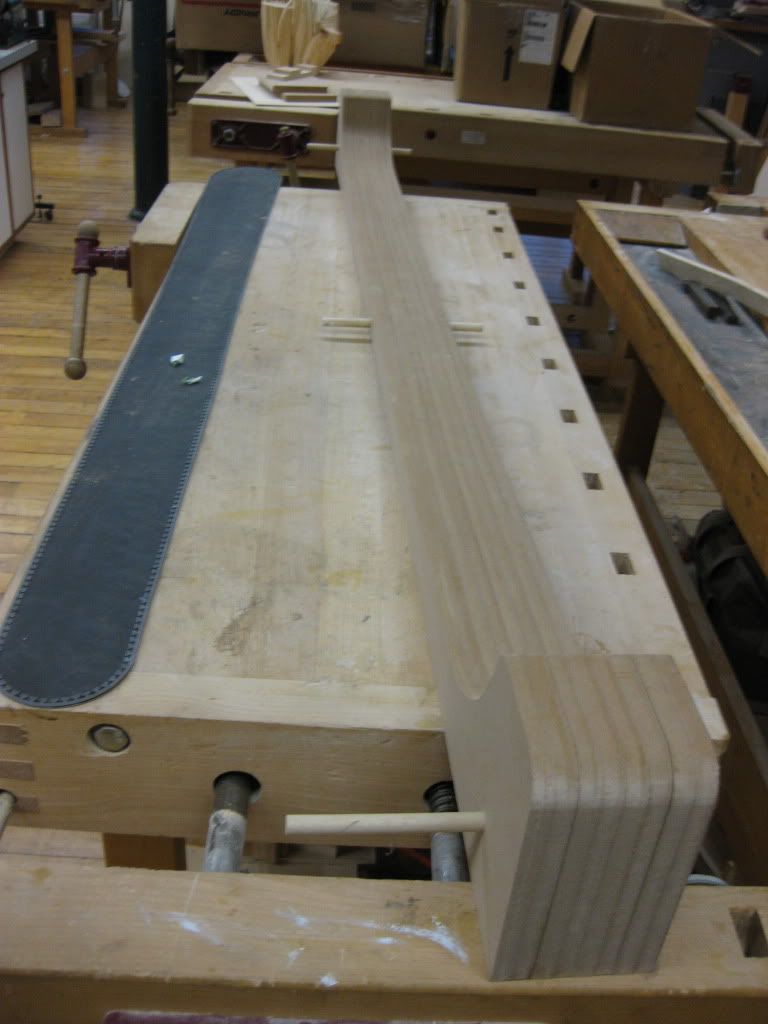
Start of the mold
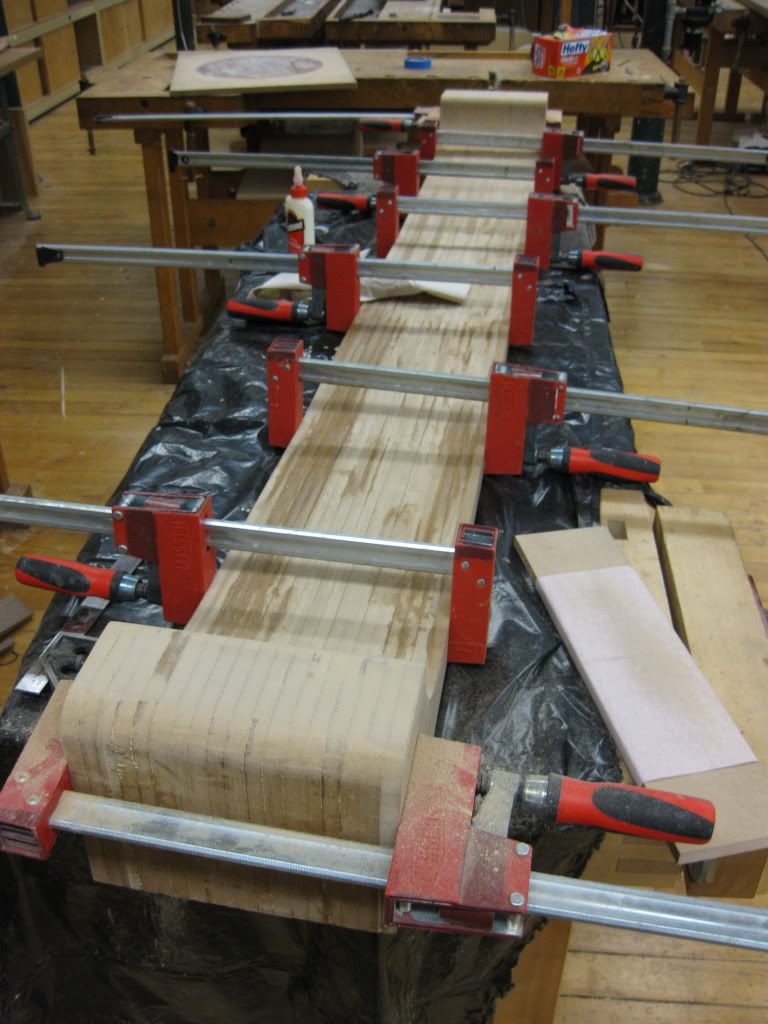
Mold Glued Up
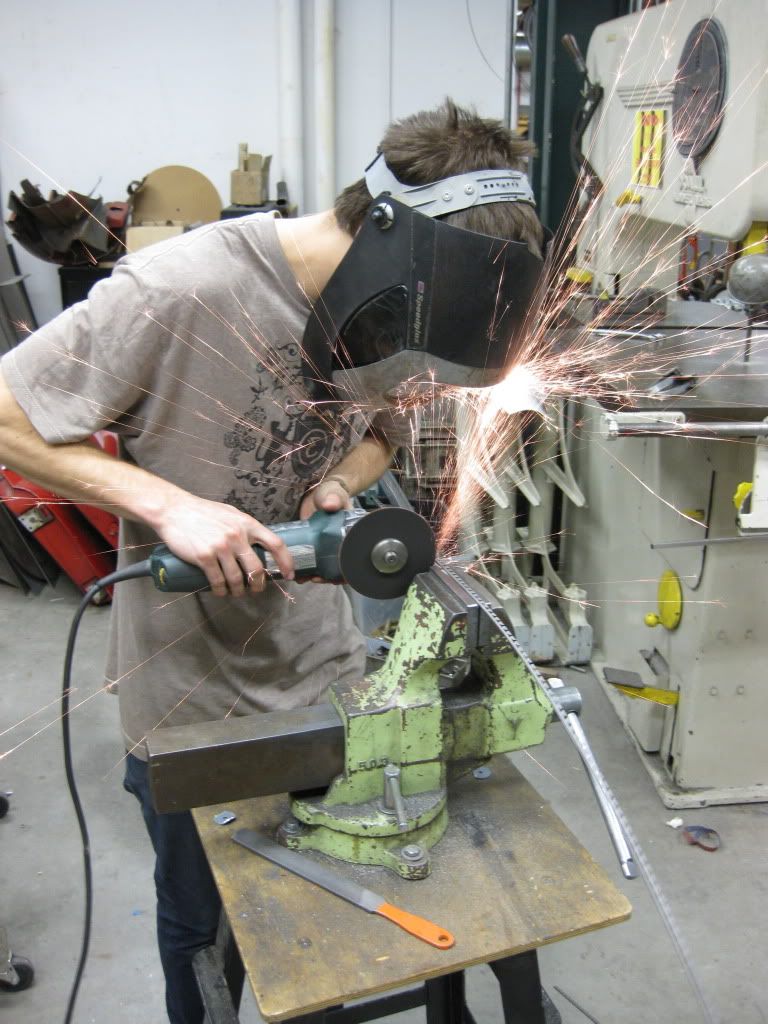
This is how not to clean up the edges
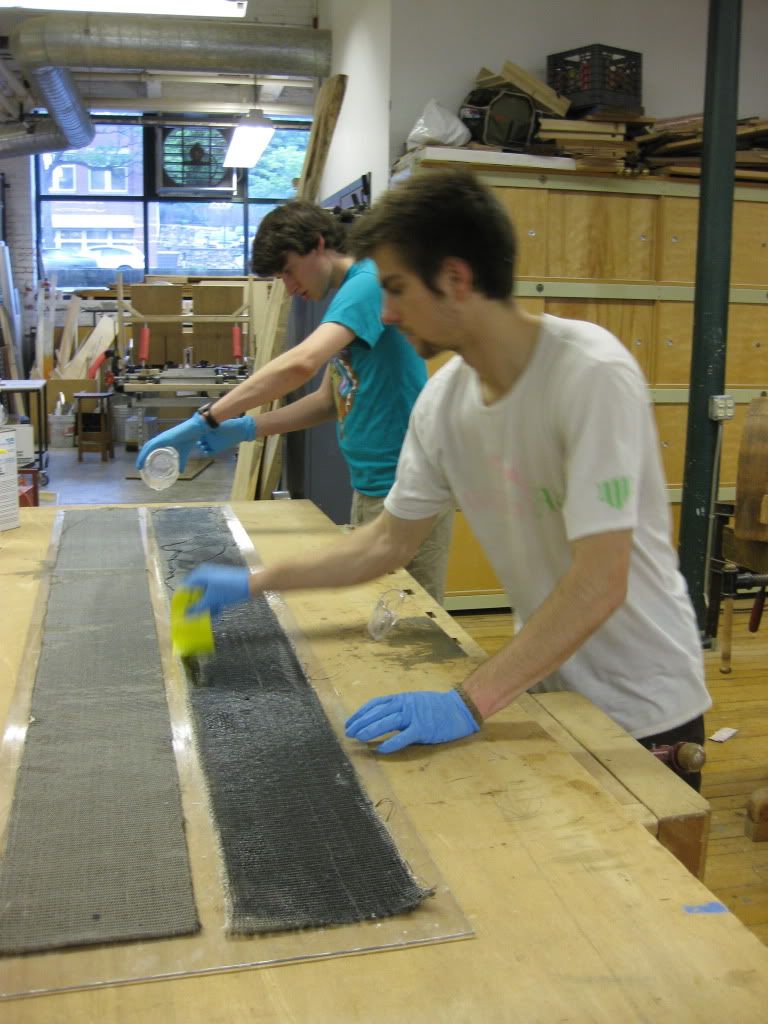
Lay up
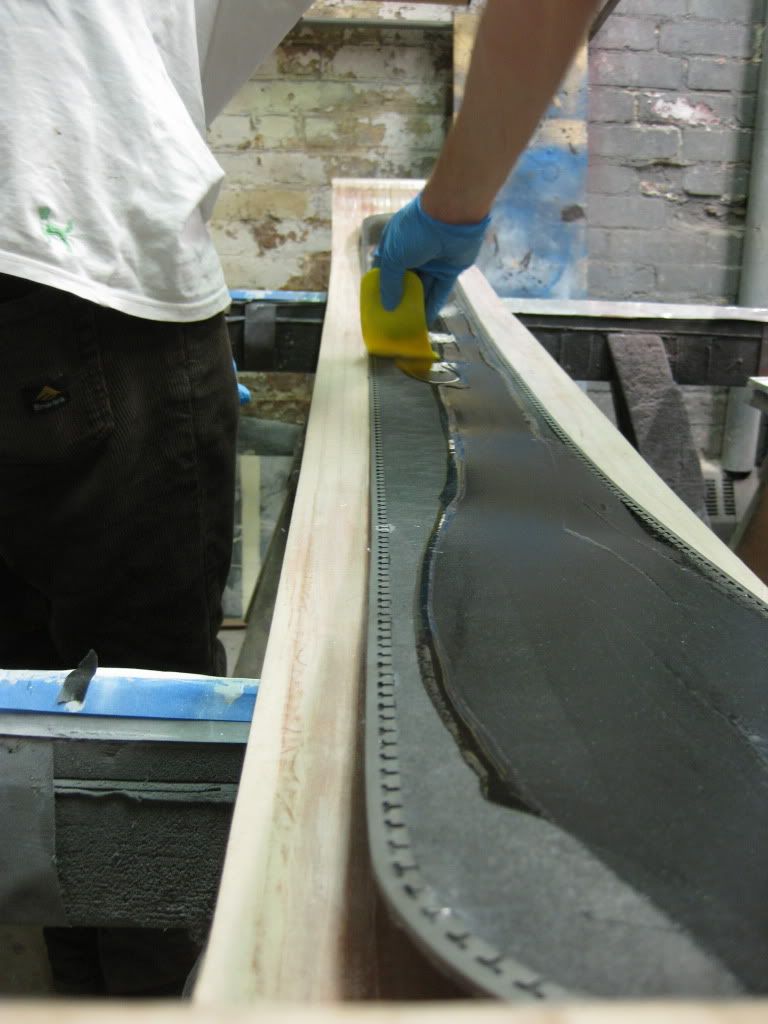
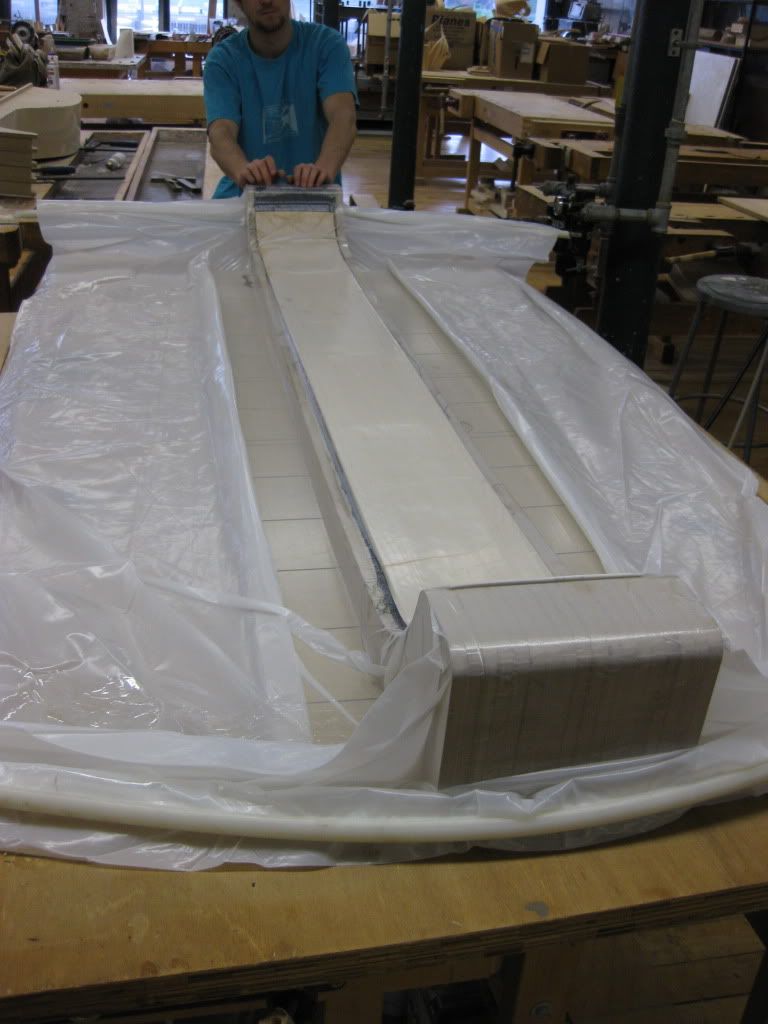
In the Bag
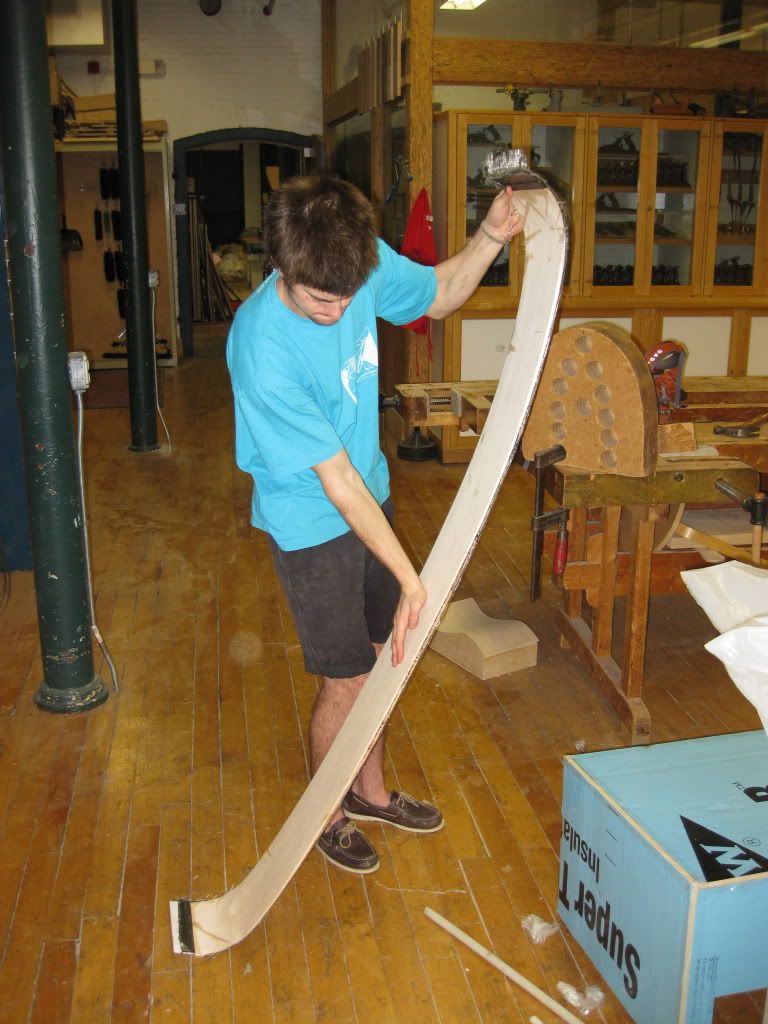
They flex pretty well
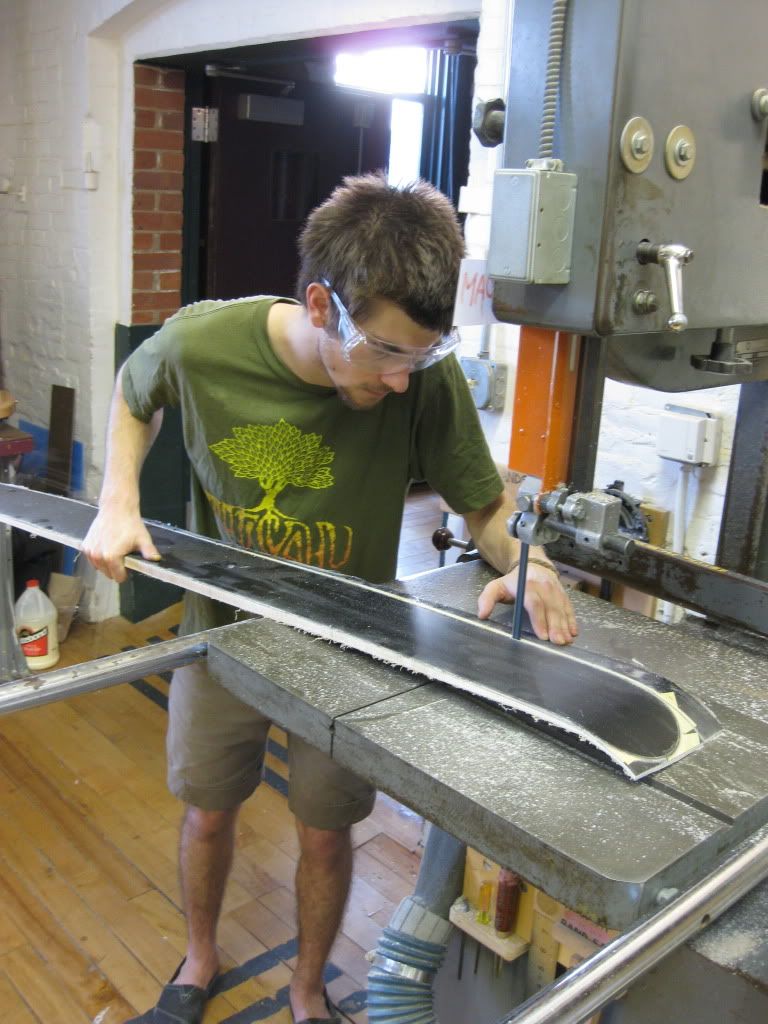
Cleaning up the skis
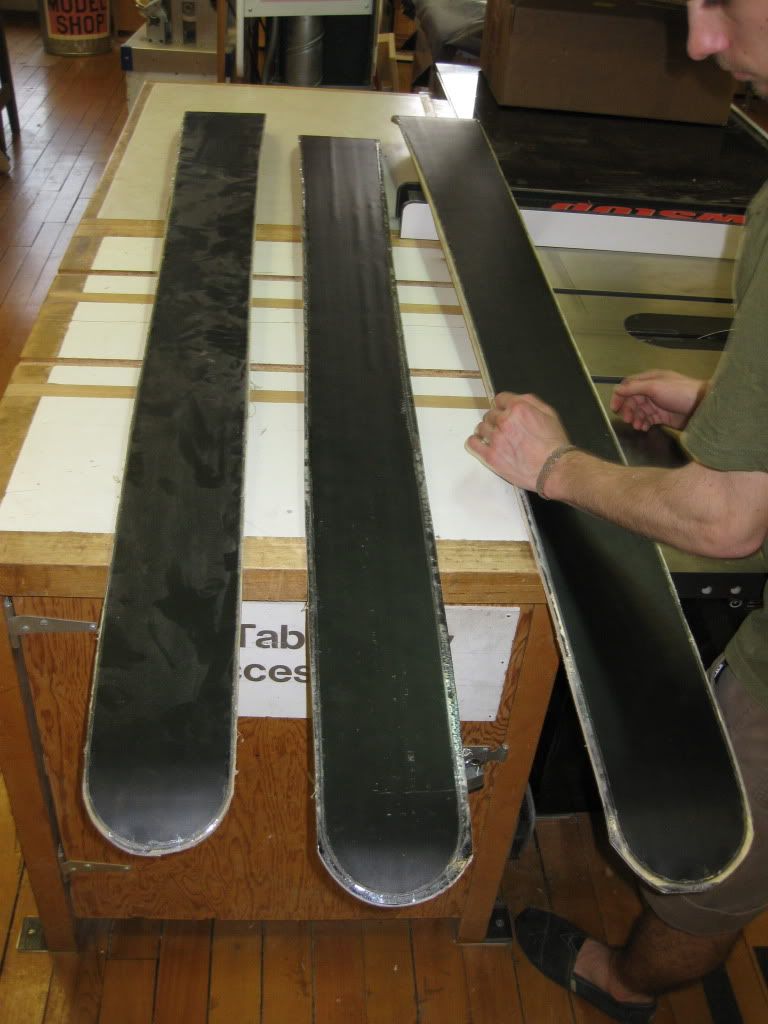
First Glimpse
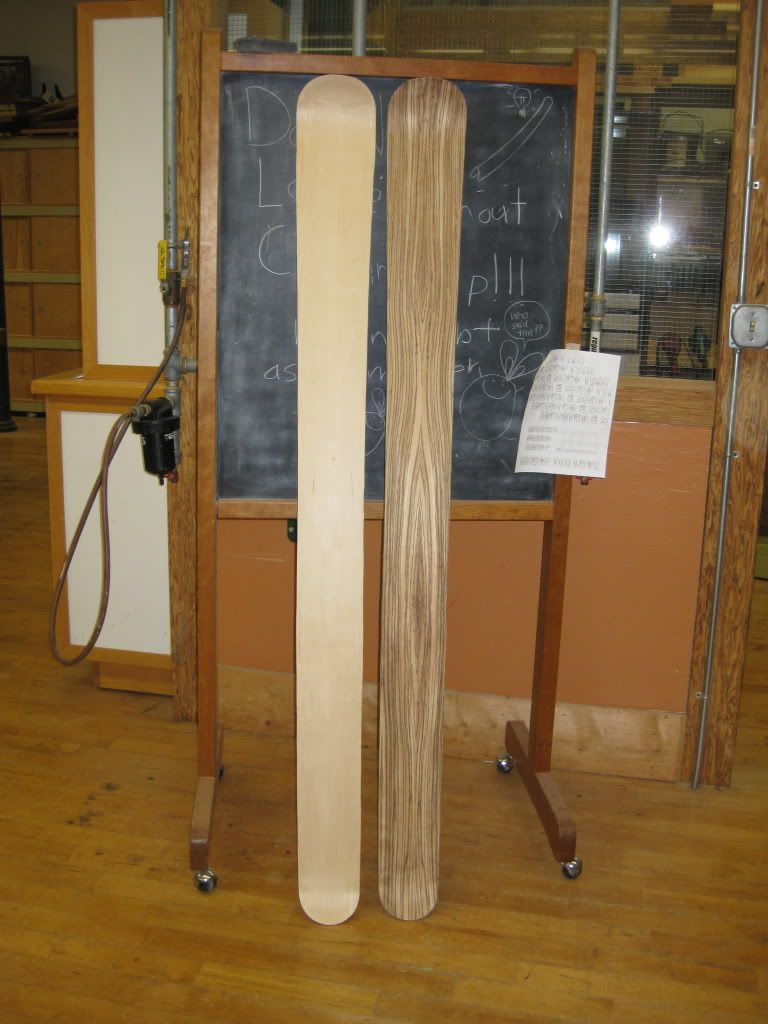
Zebra wood and Maple top sheets
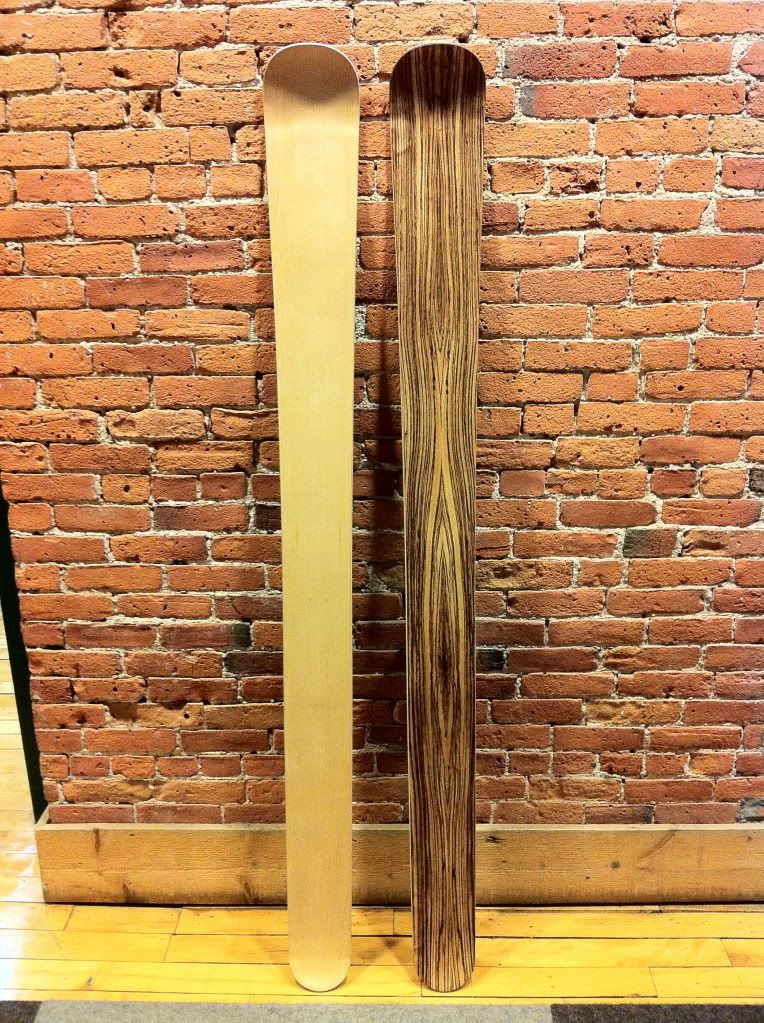
After clean up and Tung Oil application
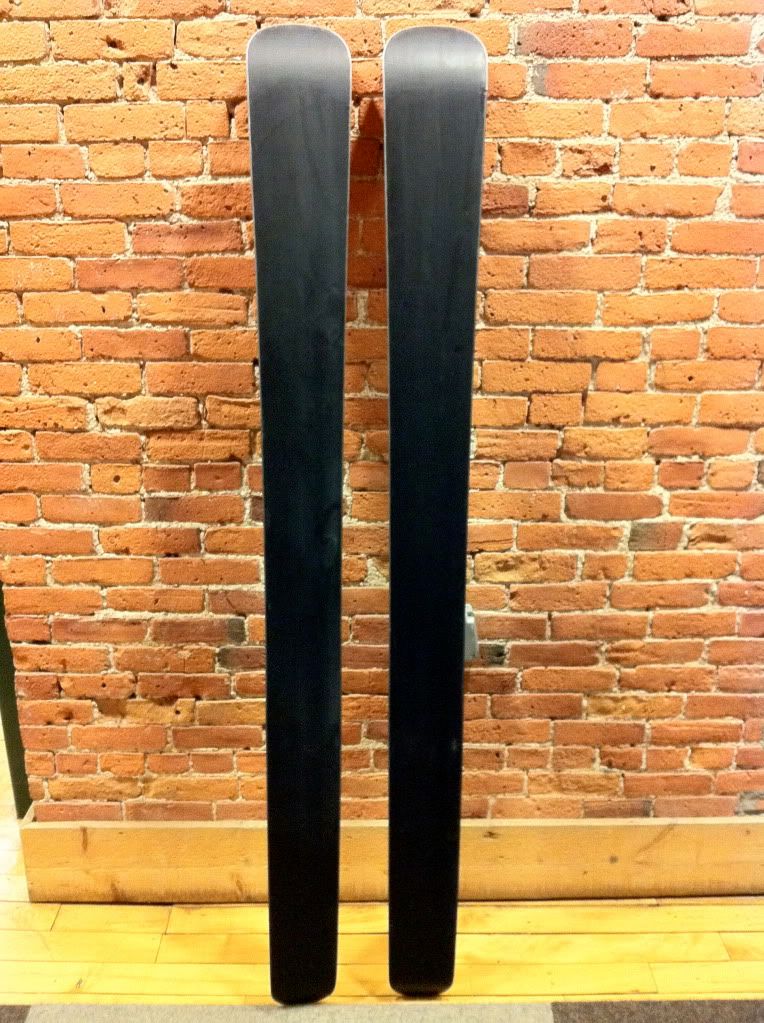
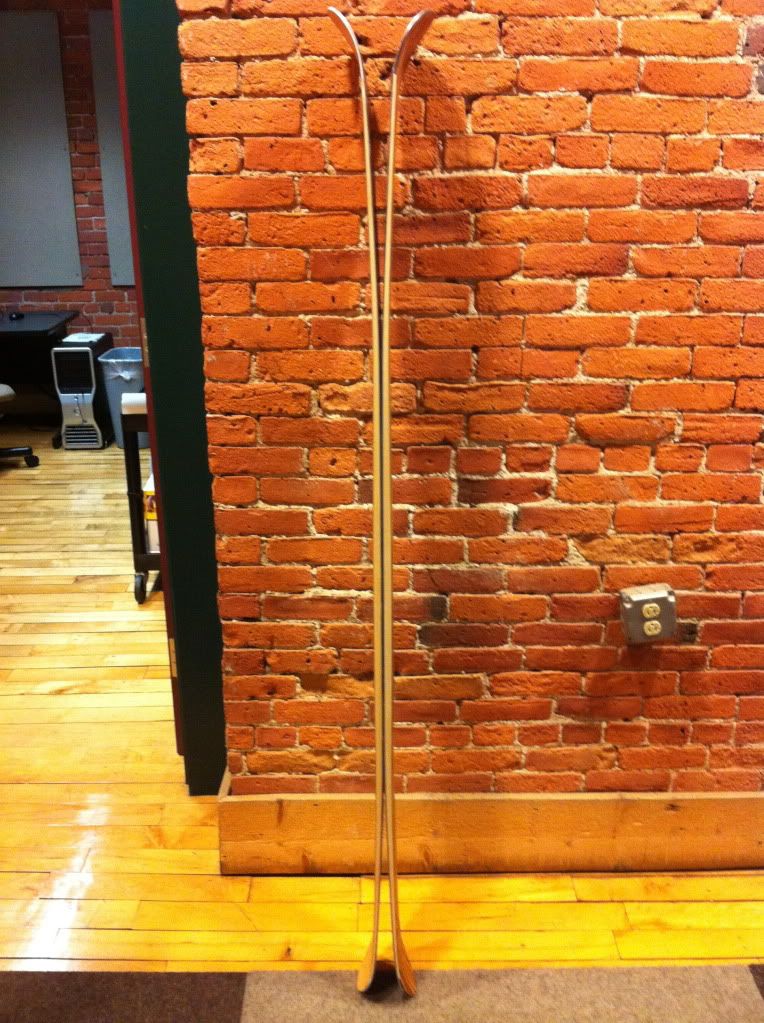
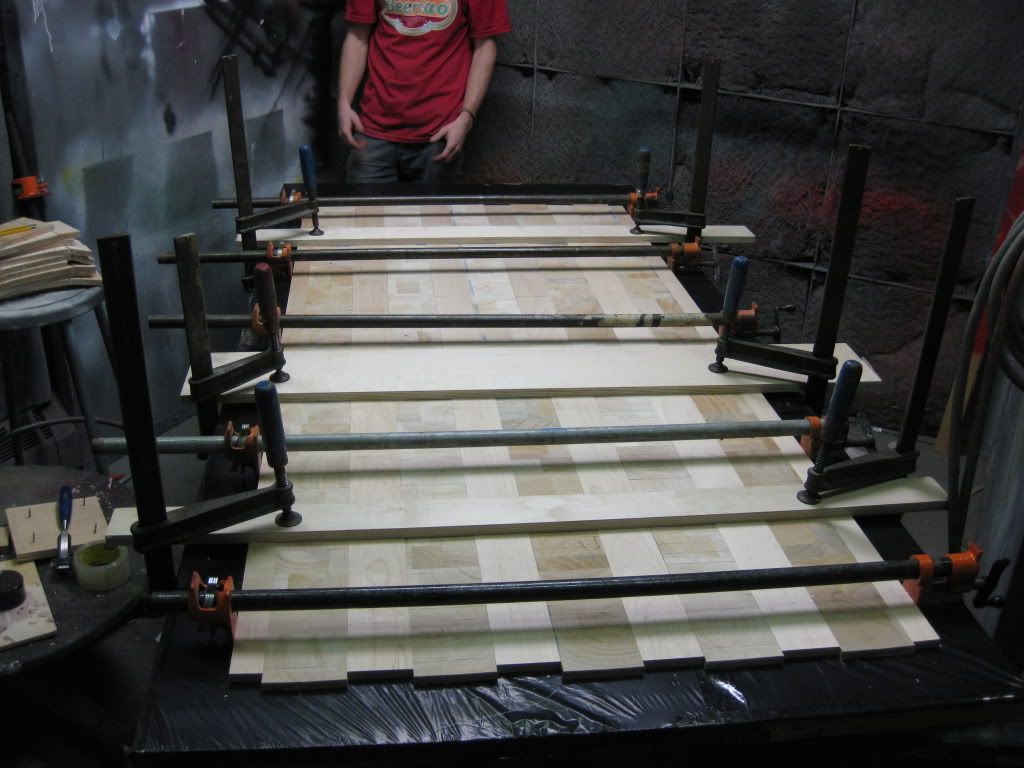
5 Cores Being glued up. 1 practice ski, 2 pairs. End grain balsa core with maple side walls. Balsa is one of the fastest grown plantation plants and has an extremely high compression resistance for its weight.
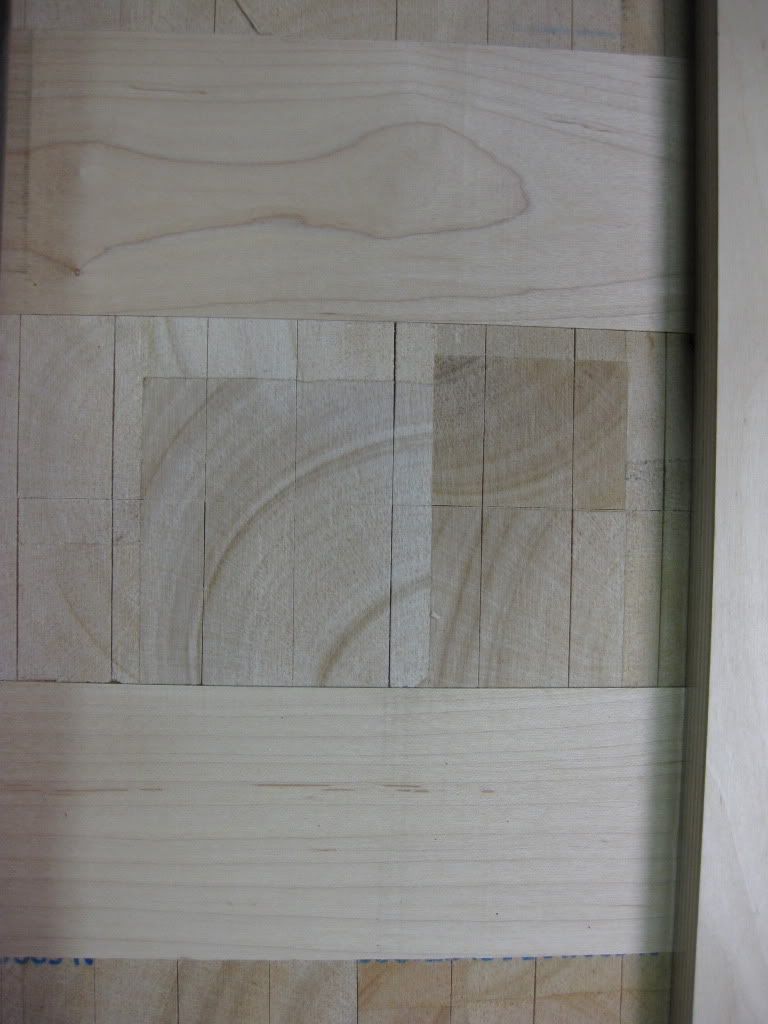
Detail shot
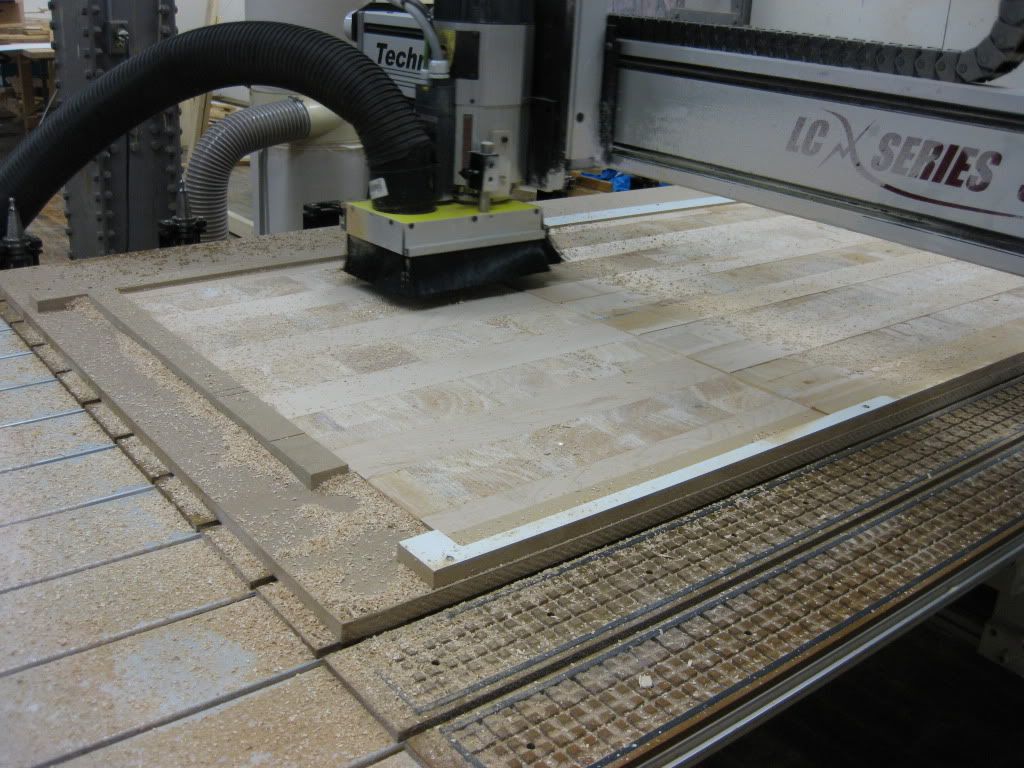
CNC;d the cores. Wont be doing that again! We hope to make a planer jig.
It was incredibly time consuming with lack luster results.
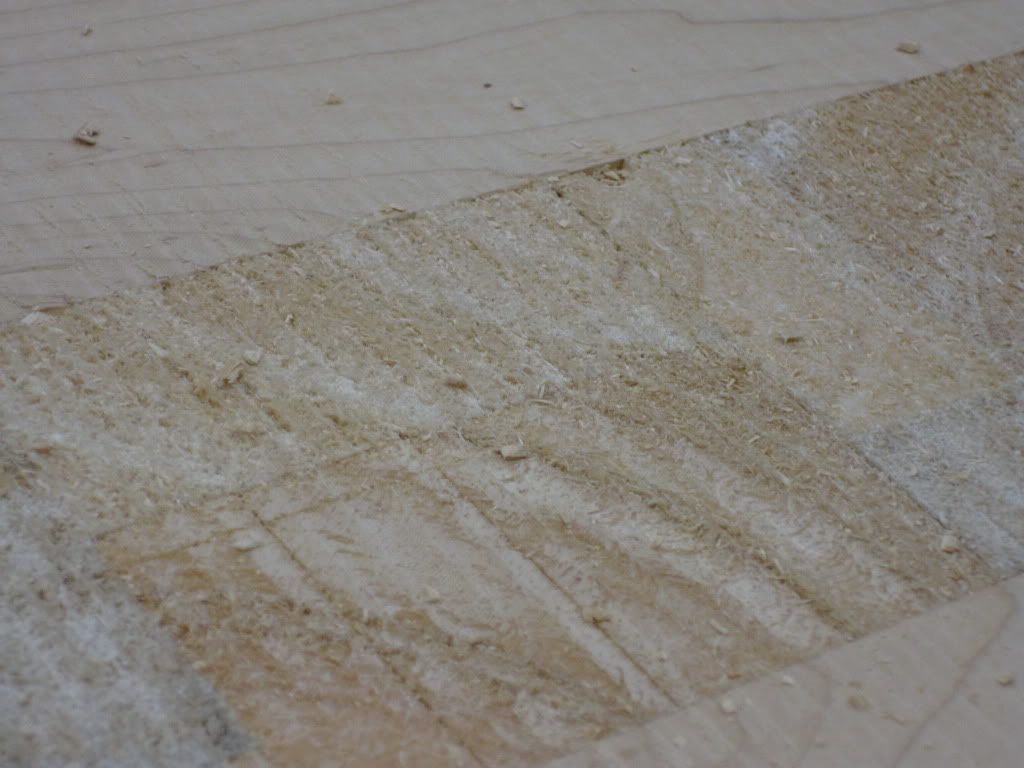
Finish Cut Detail
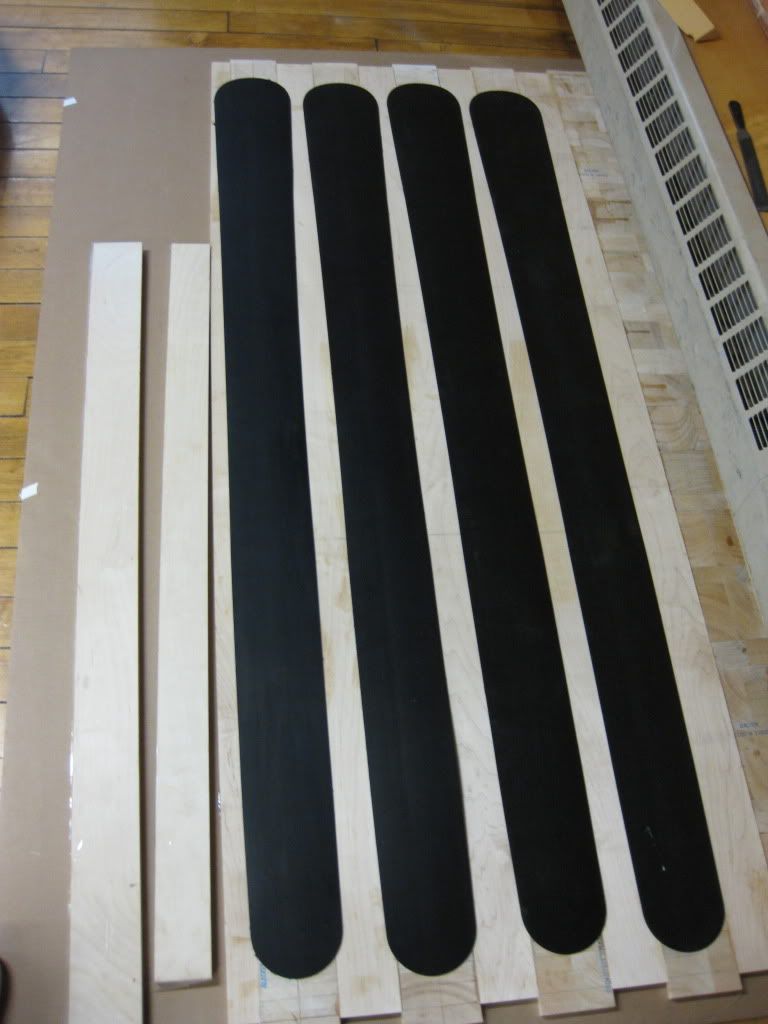
Bases were CNC'd as well, but in the future we will use a router template.

Cutting individual cores.
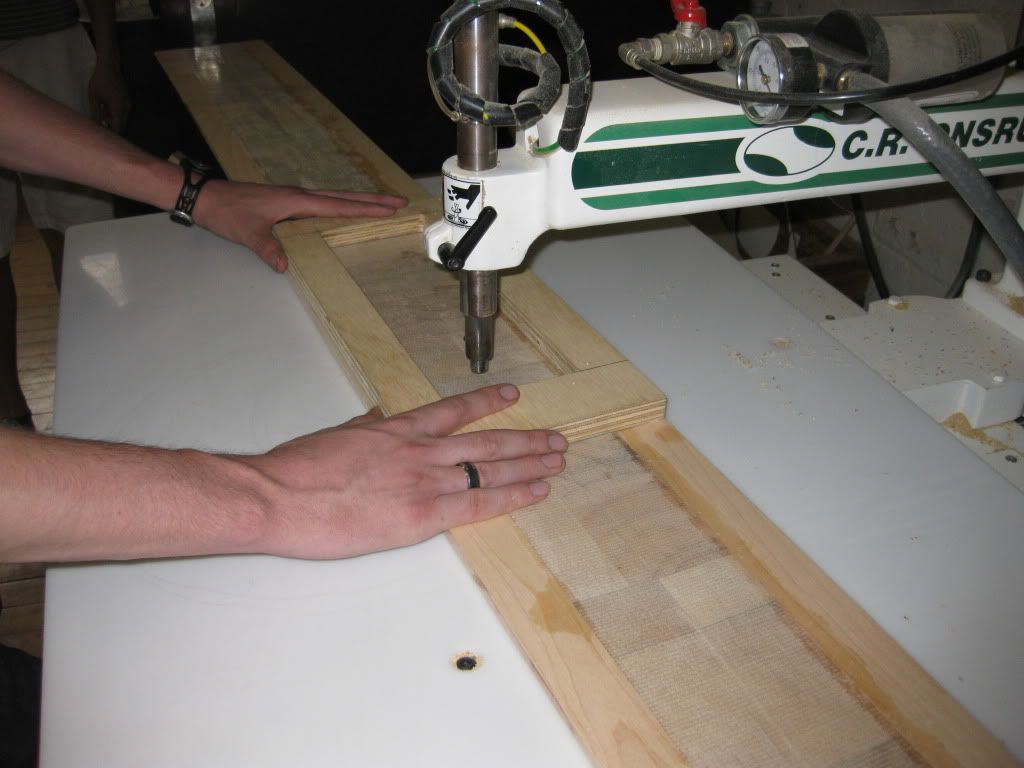
Because the Balsa has no pull out strength we had to rout out an area to place basalt fiber for the bindings to screw into.
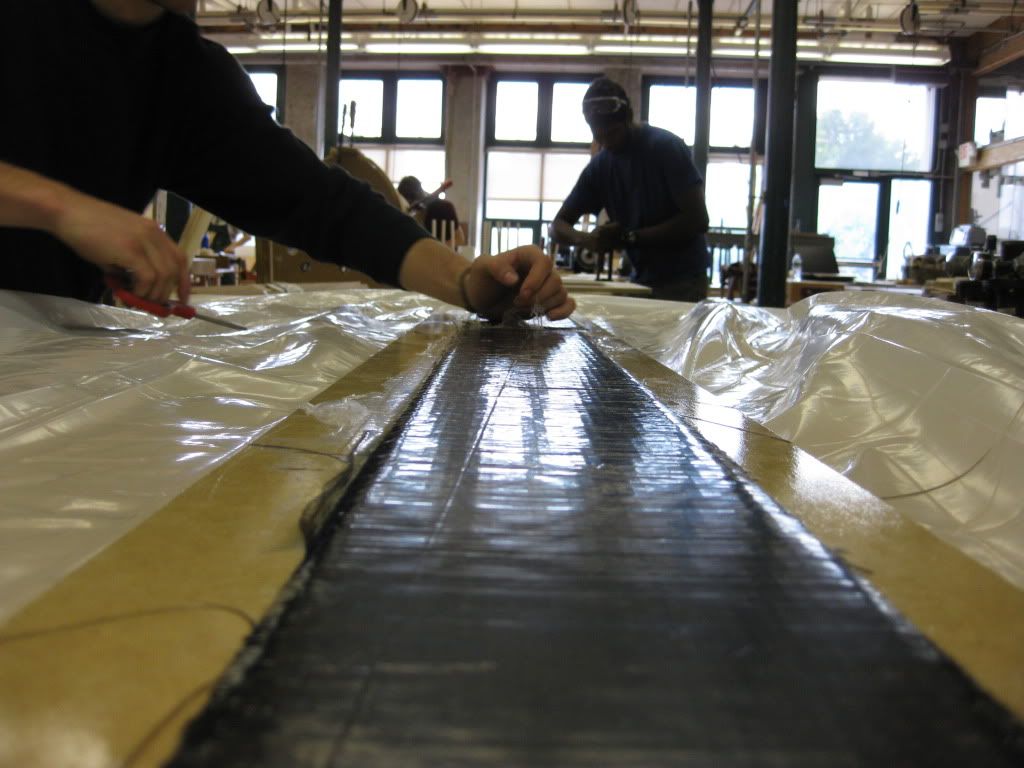
Basalt binding insert
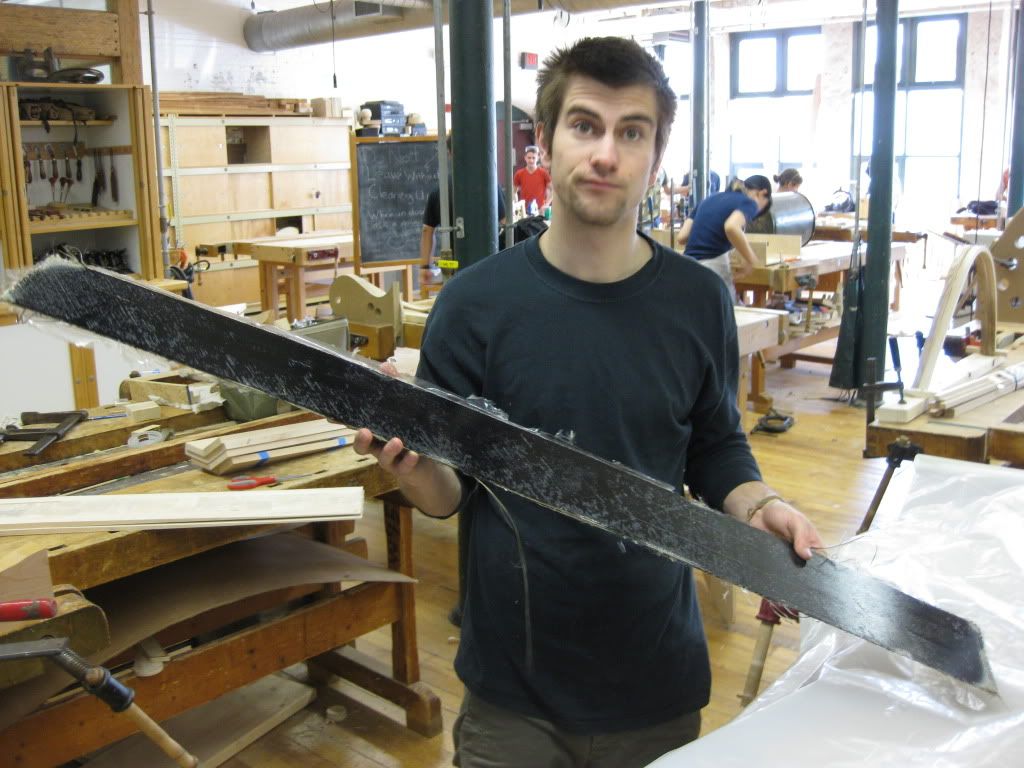
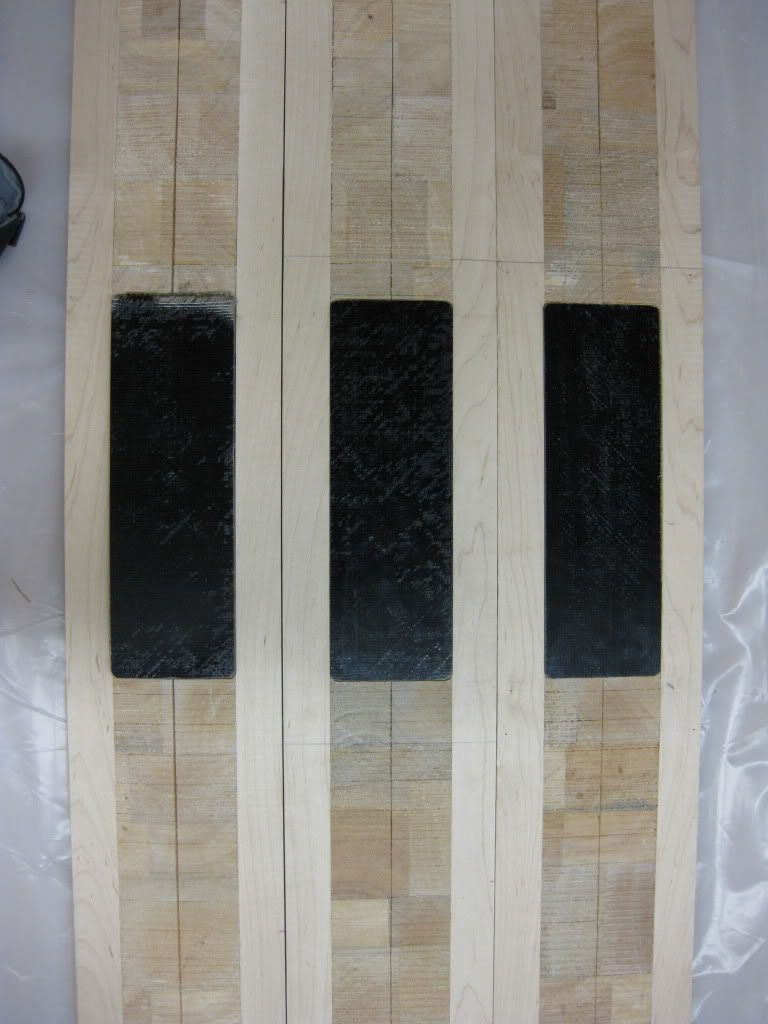
Core with Basalt insert
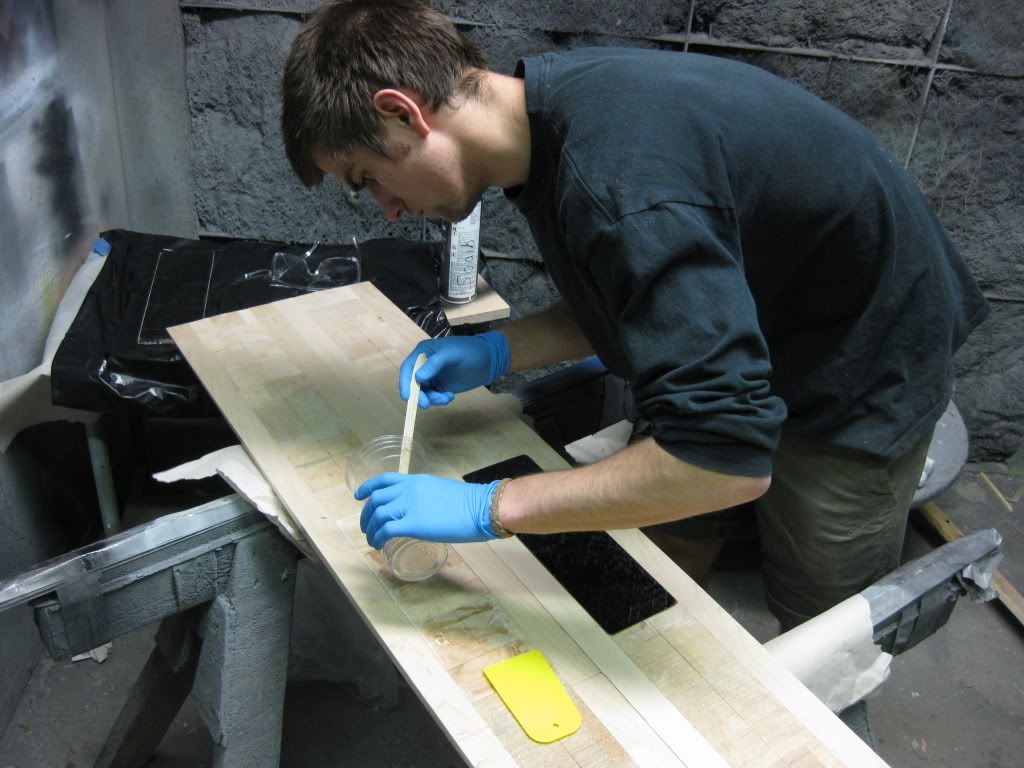
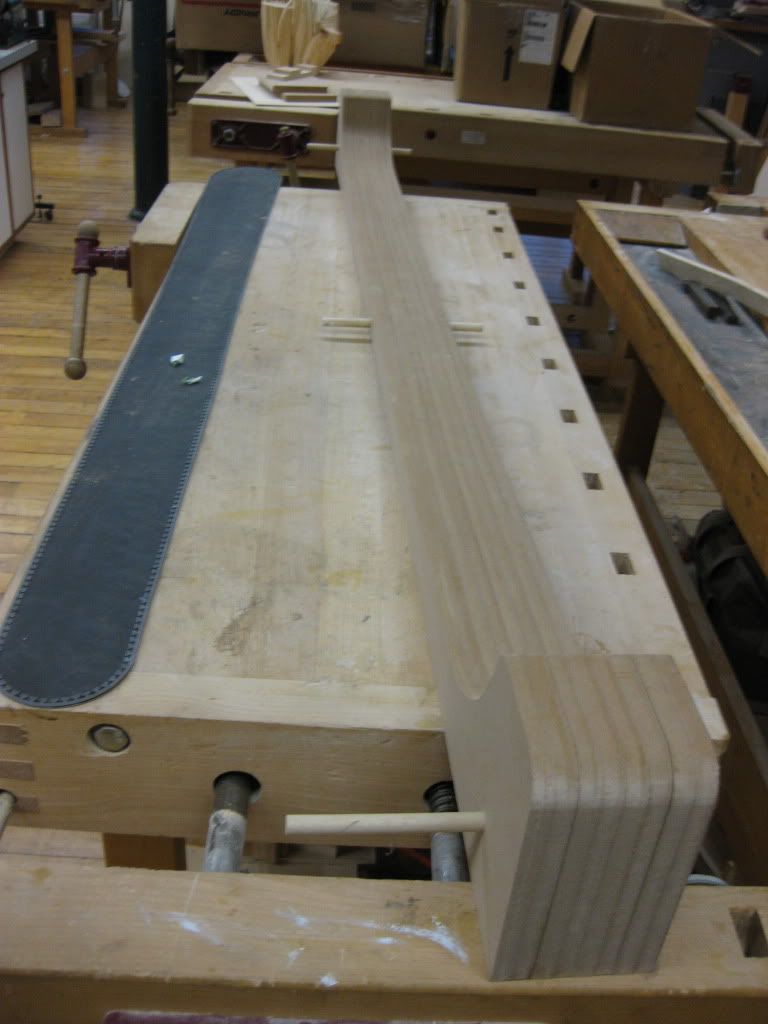
Start of the mold
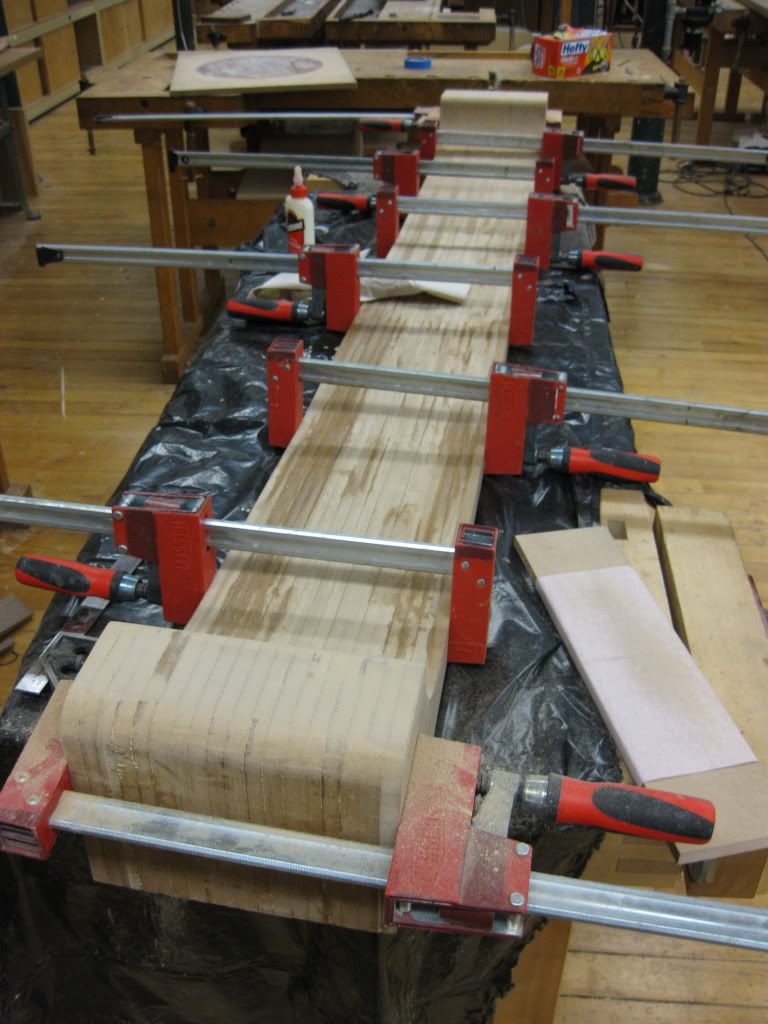
Mold Glued Up
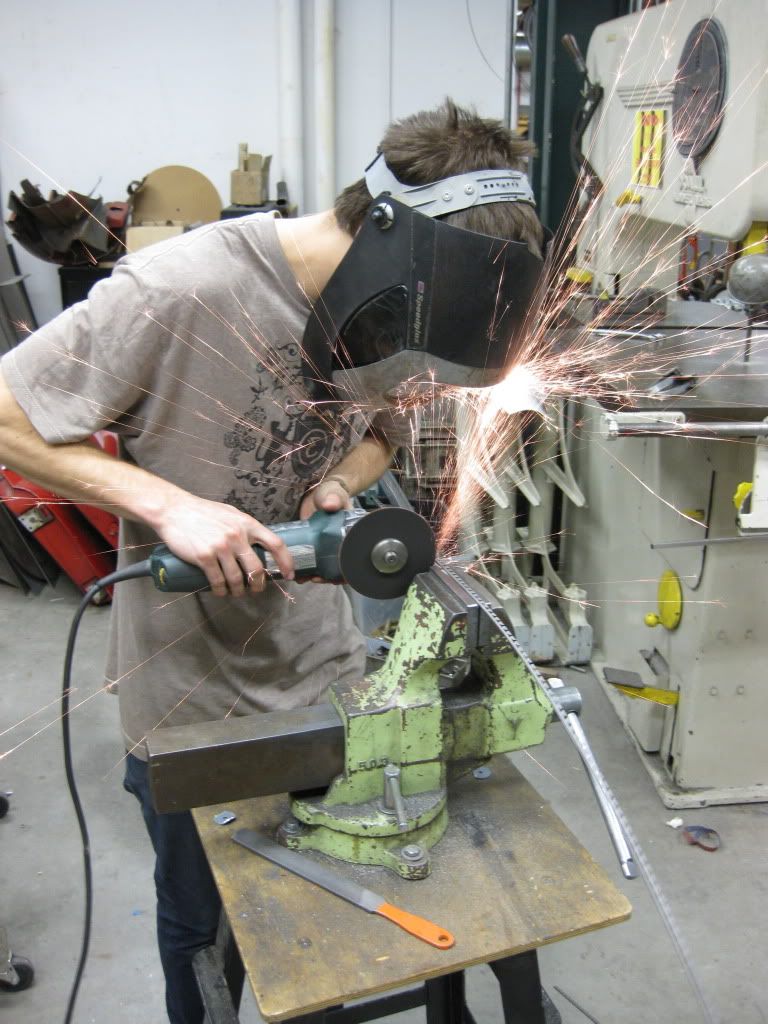
This is how not to clean up the edges
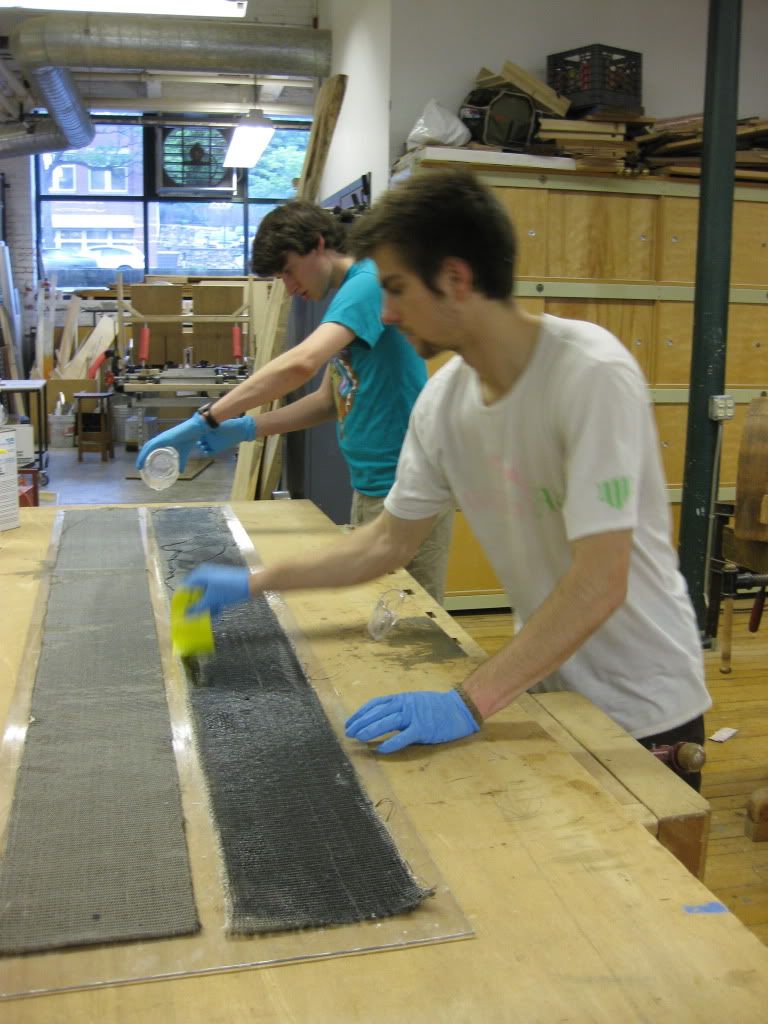
Lay up
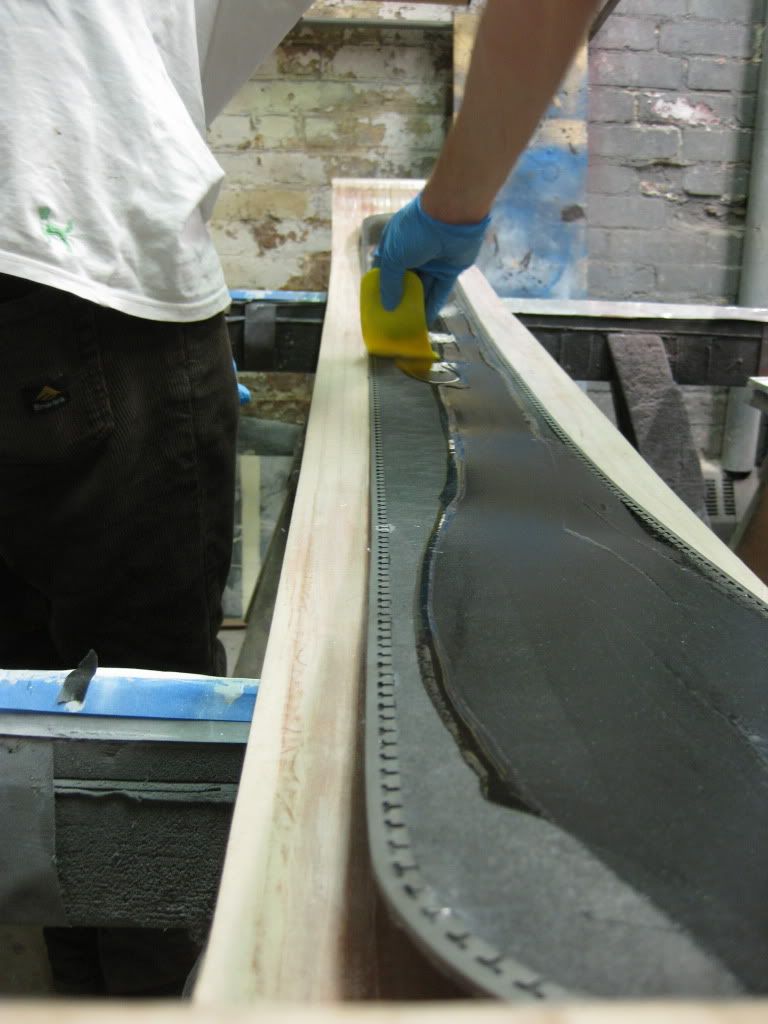
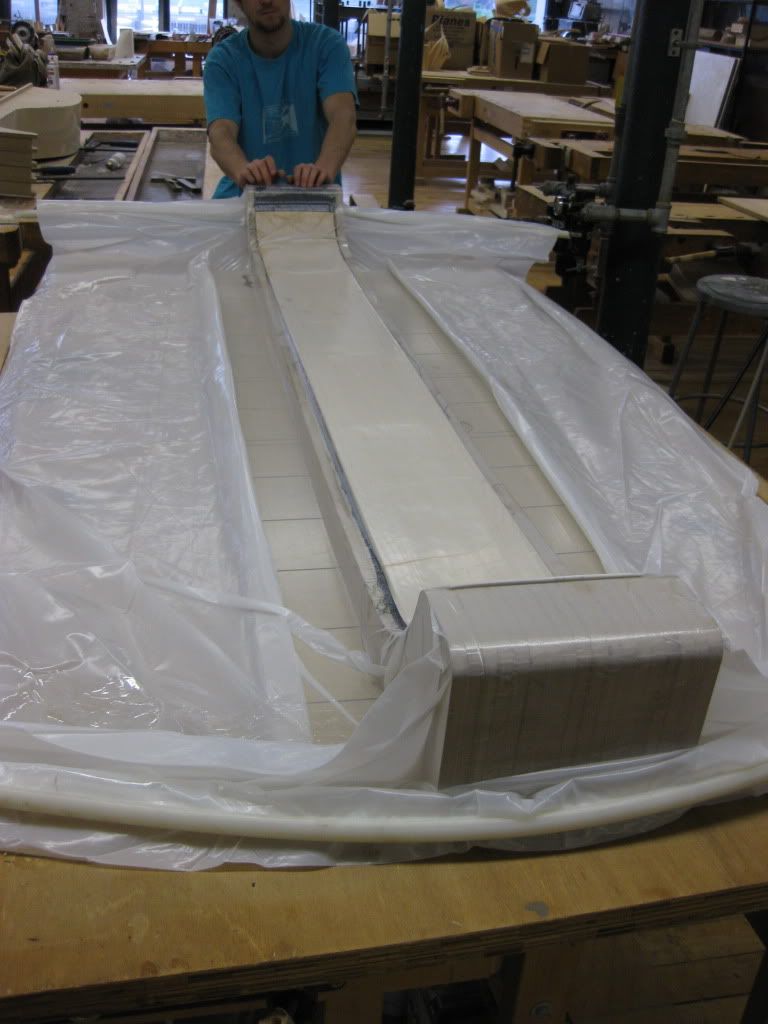
In the Bag
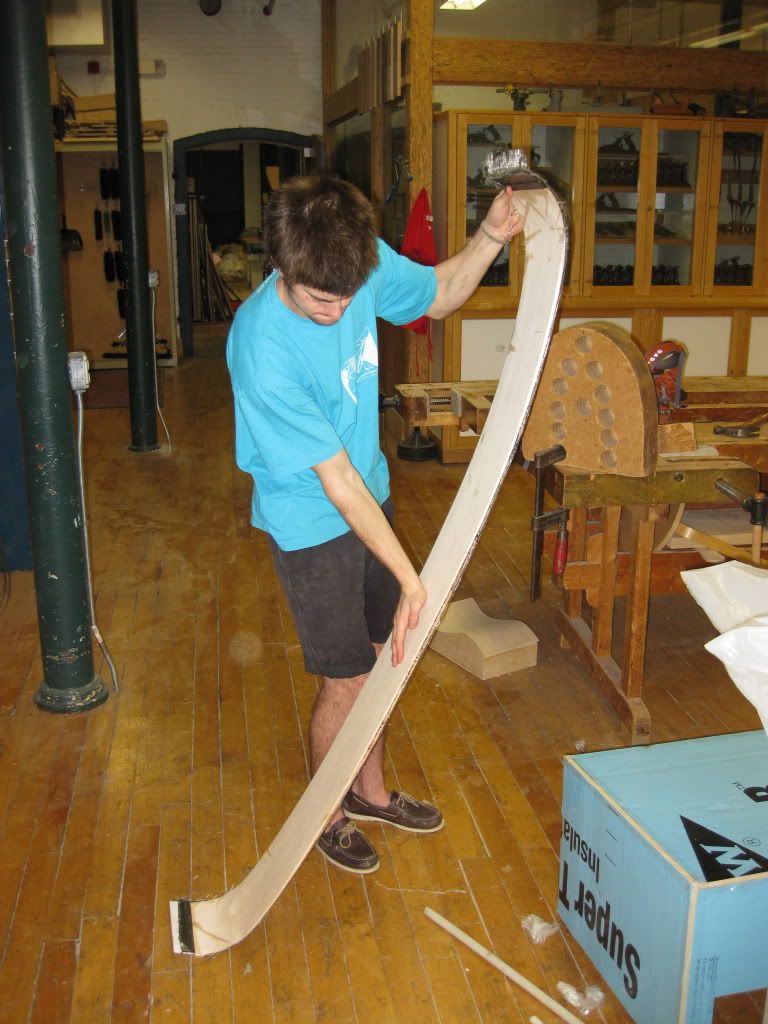
They flex pretty well
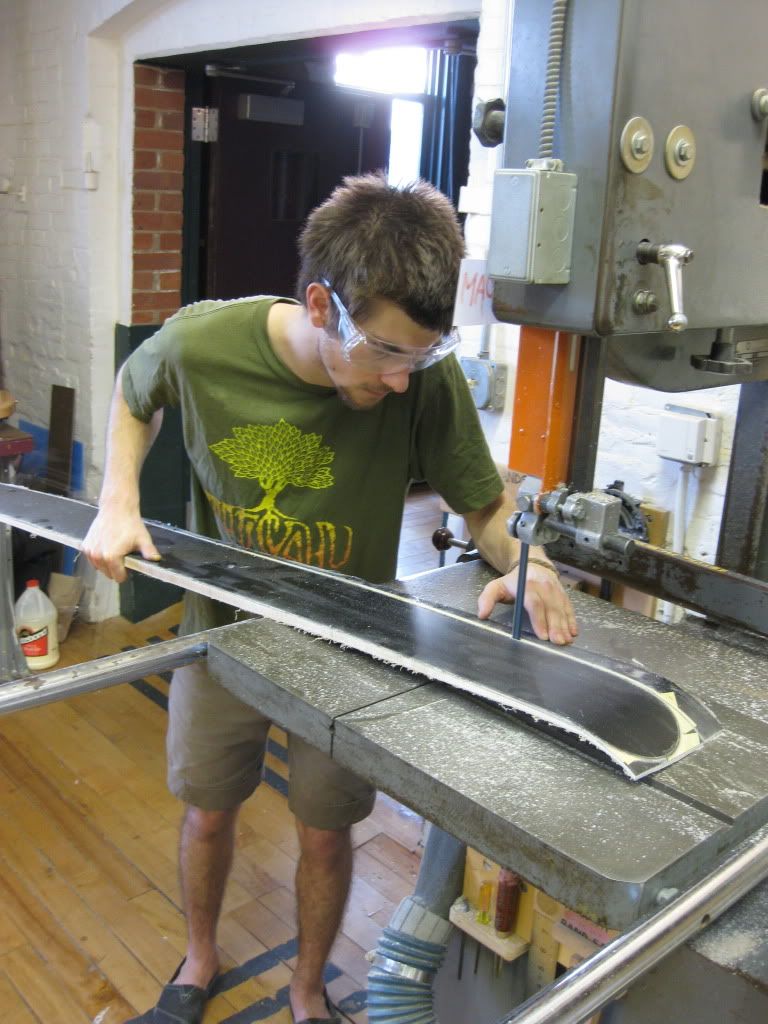
Cleaning up the skis
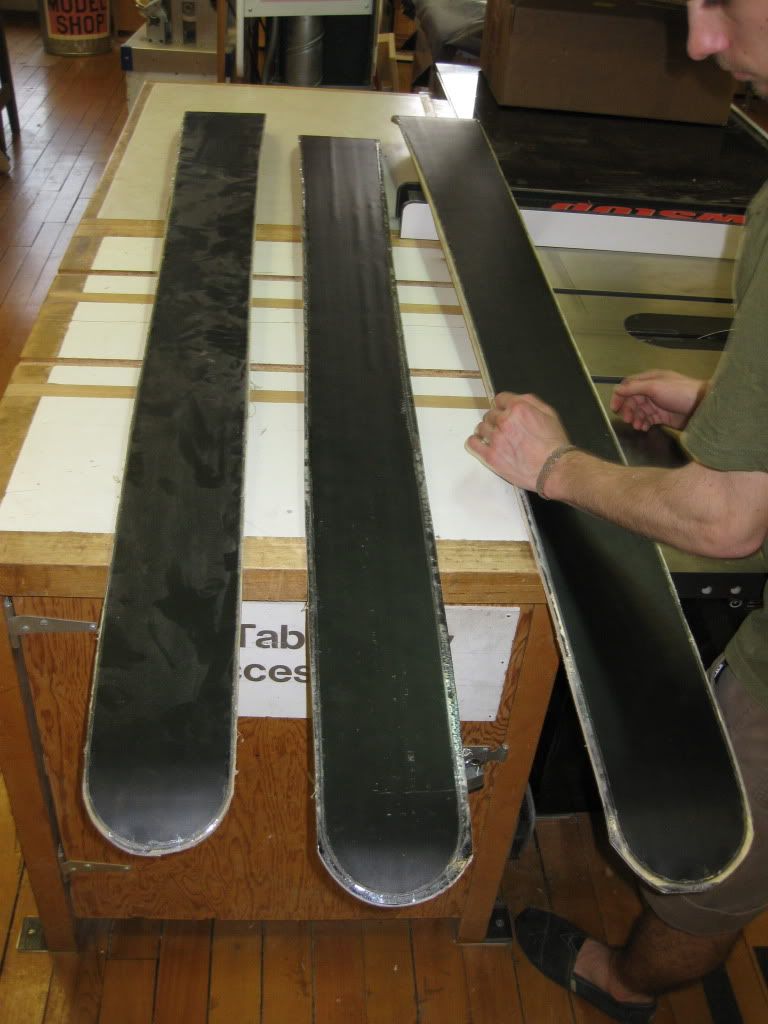
First Glimpse
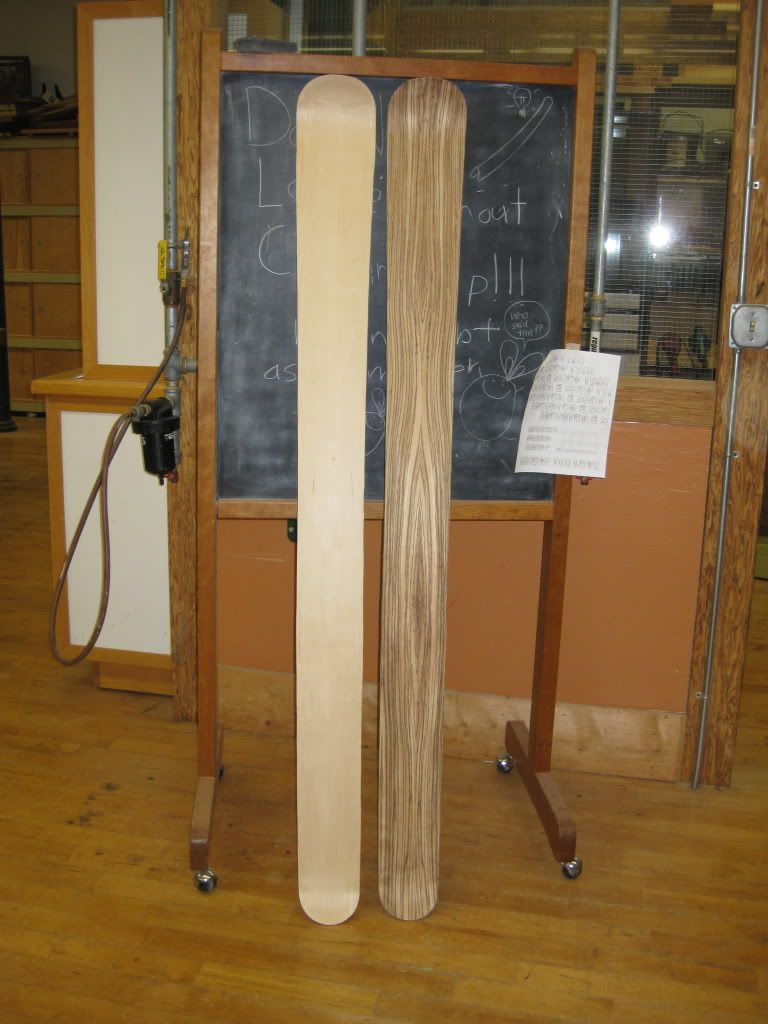
Zebra wood and Maple top sheets
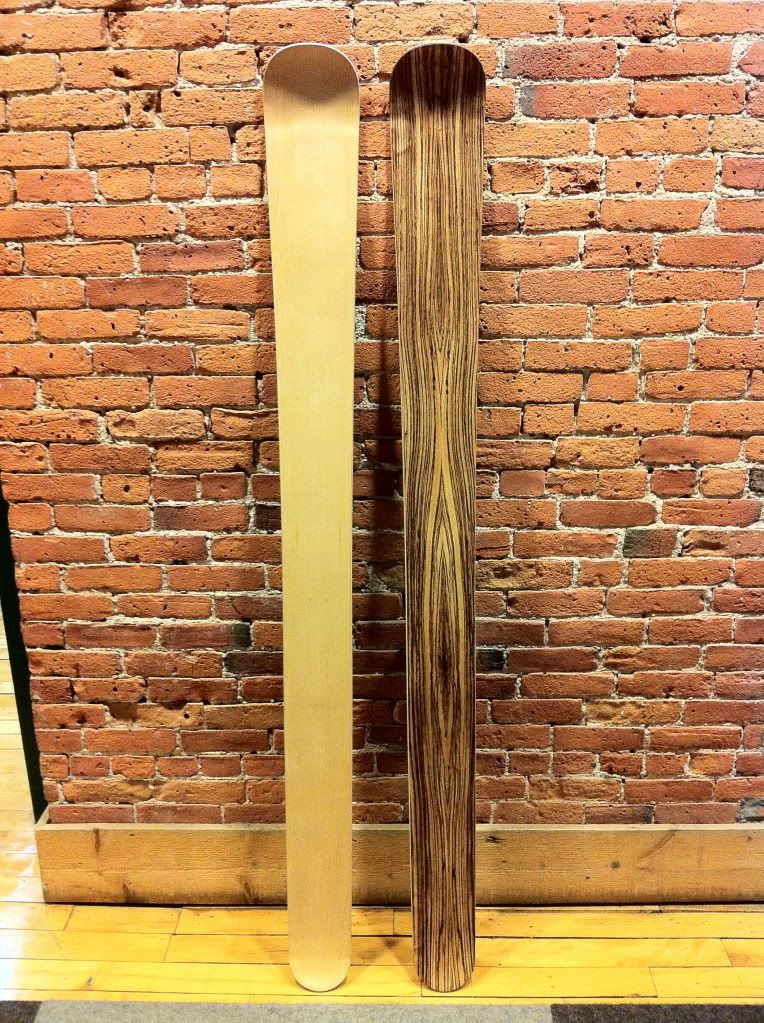
After clean up and Tung Oil application
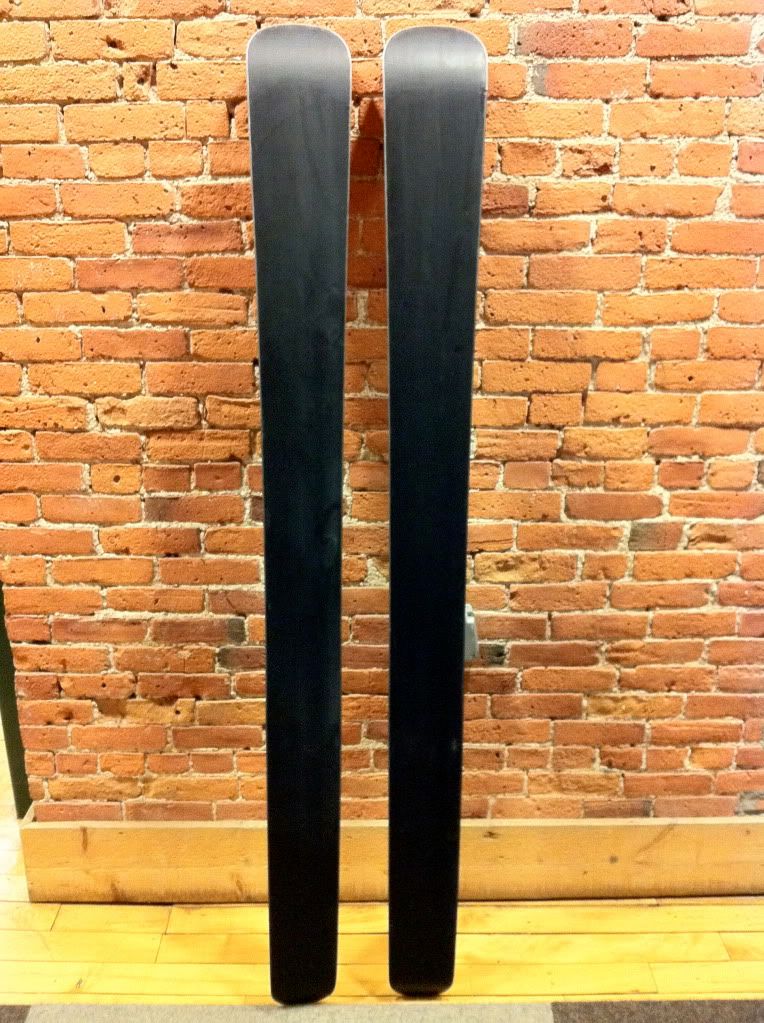
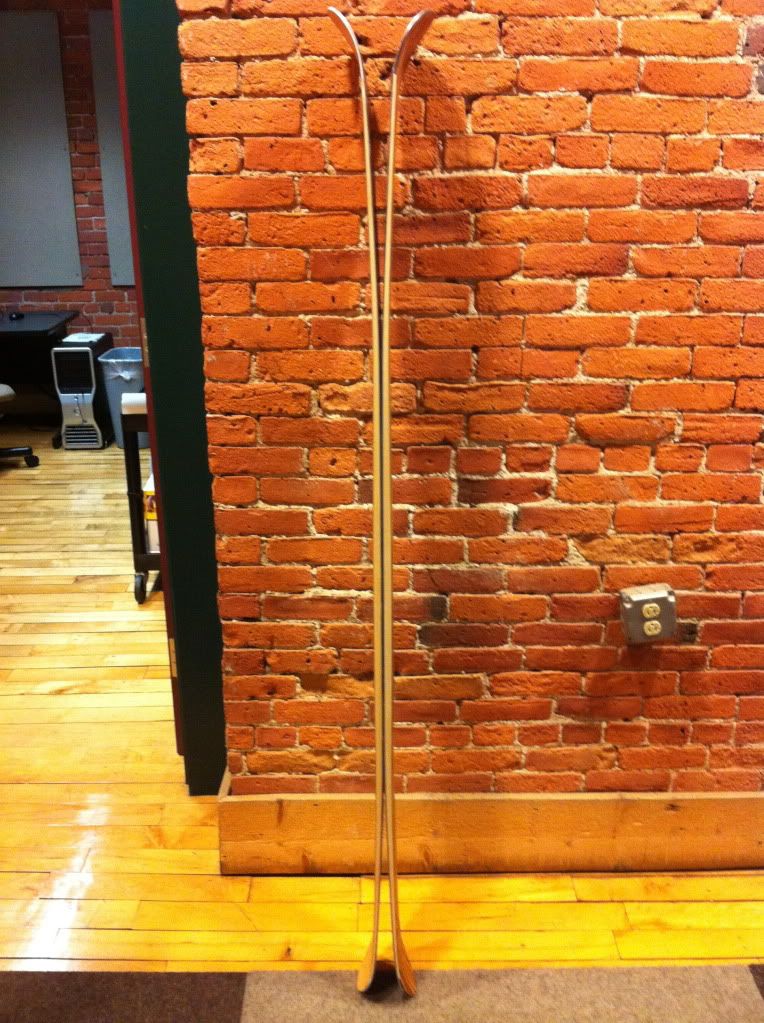
you could get rid of the tipspacers and use full woodcores and for the resin go with http://www.entropyresins.com/products like ben just recommended.
-
- Posts: 2337
- Joined: Tue Apr 07, 2009 3:26 pm
- Location: Western Mass, USA
- Contact:
Nice work guys. Wondering, what is the dimensions of the wood core? Ski looks very flexible. Also you could replace the P-tex base w/ a wood veneer. I happen to be working on a project to do that. http://www.skibuilders.com/phpBB2/viewtopic.php?t=2845 if you're interested. I just ordered 1/16in veneer for my base and laminates from www.certainlywoods.com. People here have also used hemp.
-
- Posts: 2337
- Joined: Tue Apr 07, 2009 3:26 pm
- Location: Western Mass, USA
- Contact:
-
- Posts: 2204
- Joined: Tue Mar 07, 2006 8:25 pm
- Location: Kenmore, Wa USA
The center base was our practice ski and in order to meet a deadline we pressed it on our mold before we were able to smooth the mold. Other skis were after the fact.
The end grain balsa is nice for weight and compression but it comes with downfalls. CNCing the balsa core was very tough even with extremely small passes, some tear out occurred . Glueing up is tricky as we had to fill each crack and that stuff just sucks epoxy right through it. Overall an interesting core exploration.
Basalt fiber was similar to the price of glass but still a little more. Hard to come by.
The end grain balsa is nice for weight and compression but it comes with downfalls. CNCing the balsa core was very tough even with extremely small passes, some tear out occurred . Glueing up is tricky as we had to fill each crack and that stuff just sucks epoxy right through it. Overall an interesting core exploration.
Basalt fiber was similar to the price of glass but still a little more. Hard to come by.
The center base was our practice ski and in order to meet a deadline we pressed it on our mold before we were able to smooth the mold. Other skis were after the fact.
The end grain balsa is nice for weight and compression but it comes with downfalls. CNCing the balsa core was very tough even with extremely small passes, some tear out occurred . Glueing up is tricky as we had to fill each crack and that stuff just sucks epoxy right through it. Overall an interesting core exploration.
Basalt fiber was similar to the price of glass but still a little more. Hard to come by.
The end grain balsa is nice for weight and compression but it comes with downfalls. CNCing the balsa core was very tough even with extremely small passes, some tear out occurred . Glueing up is tricky as we had to fill each crack and that stuff just sucks epoxy right through it. Overall an interesting core exploration.
Basalt fiber was similar to the price of glass but still a little more. Hard to come by.