bamboo and routers...i want them to play nice
Moderators: Head Monkey, kelvin, bigKam, skidesmond, chrismp
-
- Posts: 146
- Joined: Mon Jun 13, 2011 9:02 am
- Location: Salt Lake
- Contact:
bamboo and routers...i want them to play nice
i have vertically laminated bamboo comes in sheets of plywood. i cut a small section off to build the core. then i place my template on top. trace with a line. then get as close to it as i can with my band saw.
i then take the template (CNC'd .75in MDF) and use interior mounting double sided tape to attach it to the bamboo. then put that on the router table. (craftsman router table, fairly nice router) i am using a 3-flute flush trim bit $28 at home-depot.
if i am EXTREMELY!!! careful i can usually get the sidecut with very little problem but as soon as i try to cut to tips all bets are off. i have destroyed 2 cores and mad 3 successfully with this method so i need to change it. i am thinking of cutting the bamboo on a CNC but i am not sure if that will solve the problem. do you guys have any ideas?
i then take the template (CNC'd .75in MDF) and use interior mounting double sided tape to attach it to the bamboo. then put that on the router table. (craftsman router table, fairly nice router) i am using a 3-flute flush trim bit $28 at home-depot.
if i am EXTREMELY!!! careful i can usually get the sidecut with very little problem but as soon as i try to cut to tips all bets are off. i have destroyed 2 cores and mad 3 successfully with this method so i need to change it. i am thinking of cutting the bamboo on a CNC but i am not sure if that will solve the problem. do you guys have any ideas?
-
- Posts: 2204
- Joined: Tue Mar 07, 2006 8:25 pm
- Location: Kenmore, Wa USA
-
- Posts: 146
- Joined: Mon Jun 13, 2011 9:02 am
- Location: Salt Lake
- Contact:
yes the bamboo is ripping apart, almost as though the router isnt sharp enough and is catching a ripping it down the grain.
i am using tip spacer but i am still cutting a round tip to fit into the tip spacer.
i was not really sure how to use the tip space to i just kind guessed. if i could just make the bases a rectangle and attach the tip spacer on the end that would be awesome, but i was thinking that would cause a major weakspot in the ski
i am using tip spacer but i am still cutting a round tip to fit into the tip spacer.
i was not really sure how to use the tip space to i just kind guessed. if i could just make the bases a rectangle and attach the tip spacer on the end that would be awesome, but i was thinking that would cause a major weakspot in the ski
It sounds like the glue used to laminate the bamboo you are using isn't doing you any favours.
Sounds like you understand how the problem is being caused, so hopefully this will make sense. To solve the problem you could use two cutters to process the core:
Bottom bearing cutter when cutting the first half of the sidecut. Top bearing cutter (flip the core over), when cutting second half. This way you are always cutting into the laminate/grain of the bamboo.
It does create a weak spot - most people create some sort of arrow head to feather the stress.
Sounds like you understand how the problem is being caused, so hopefully this will make sense. To solve the problem you could use two cutters to process the core:
Bottom bearing cutter when cutting the first half of the sidecut. Top bearing cutter (flip the core over), when cutting second half. This way you are always cutting into the laminate/grain of the bamboo.
It does create a weak spot - most people create some sort of arrow head to feather the stress.
-
- Posts: 146
- Joined: Mon Jun 13, 2011 9:02 am
- Location: Salt Lake
- Contact:
-
- Posts: 192
- Joined: Tue Mar 15, 2011 2:51 pm
A spiral fluted bit should help plus as a wood worker I run the router in the opposite direction when tear out is likely. The bit is still spinning it's normal way but you do what is called "climb milling" so if you aren't very careful the router will tend to run away on you. Try a test piece to practice.
You must be sure to "climb mill" as HP said. "Plunge milling" will want to tear the bamboo fibers apart.
This photo shows tip shaping a vert bamboo core with a cheap router bit using a Lexan template:

Actually in this photo the job is already done. But for climb milling the core would be pushed forward relative to the router bit in this orientation. (the cutter is turning counter clock wise)
I've never had an issue when climb milling.
-S
This photo shows tip shaping a vert bamboo core with a cheap router bit using a Lexan template:

Actually in this photo the job is already done. But for climb milling the core would be pushed forward relative to the router bit in this orientation. (the cutter is turning counter clock wise)
I've never had an issue when climb milling.
-S
-
- Posts: 30
- Joined: Mon Aug 30, 2010 7:29 pm
-
- Posts: 2204
- Joined: Tue Mar 07, 2006 8:25 pm
- Location: Kenmore, Wa USA
It is true that cutting the core straight across for the tip spacer creates a weak spot... But since I'm just making skis for myself and not selling them, I go the lazy route, and have had zero issues. Doing a point, or even better a round tip like it sounds like you're doing and in SHIF's photo would be ideal, but if you still can't find success, cut that sucker straight across and head to the press, that's what I say 

-
- Posts: 146
- Joined: Mon Jun 13, 2011 9:02 am
- Location: Salt Lake
- Contact:
thanks for all the ideas, its your advice is indispensable. i will pick up a bigger bit tomorrow. i think i have been climb milling, i pull it slowly towards me because if i push it rips out instantly then swap sides and go the same direction. i am totally new to sophisticated wood working have background in metal work. is this what you guys are talking about.
totally different topic...i was so mad earlier when i ruined my 3rd core "F@#$ ski building, but then i had a victory, figured out a really fast method to get perfectly bent edges and i feel great again.
totally different topic...i was so mad earlier when i ruined my 3rd core "F@#$ ski building, but then i had a victory, figured out a really fast method to get perfectly bent edges and i feel great again.
I have had this problem also with bamboo.
Sidecut is usually OK, except sometimes if there is a small void and the router bit tries to get between layers of the laminate. Around the tips have had problems like you with splitting.
Have generally been using a 1/4 inch diam cutter
Speaking to a friend recently he said that the larger the cutter the better you will go (reduces the angle at which the cutting edge strikes the workpiece) plus climb cutting very carefully as others have said.
I think SHIF's style of core and what you are trying to do with the curved core meeting the tip spacer is the best. Having said that I just cut them straight across and have had no breakages so far over probably 25 days on my own skis now.
I need to buy a router table and 1/2 inch shank router so I can use larger bits.
Sidecut is usually OK, except sometimes if there is a small void and the router bit tries to get between layers of the laminate. Around the tips have had problems like you with splitting.
Have generally been using a 1/4 inch diam cutter
Speaking to a friend recently he said that the larger the cutter the better you will go (reduces the angle at which the cutting edge strikes the workpiece) plus climb cutting very carefully as others have said.
I think SHIF's style of core and what you are trying to do with the curved core meeting the tip spacer is the best. Having said that I just cut them straight across and have had no breakages so far over probably 25 days on my own skis now.
I need to buy a router table and 1/2 inch shank router so I can use larger bits.
Don't wait up, I'm off to kill Summer....
-
- Posts: 146
- Joined: Mon Jun 13, 2011 9:02 am
- Location: Salt Lake
- Contact:
I too am with the down and dirty. Cut it straight across and press away. This I think is most are afraid of...
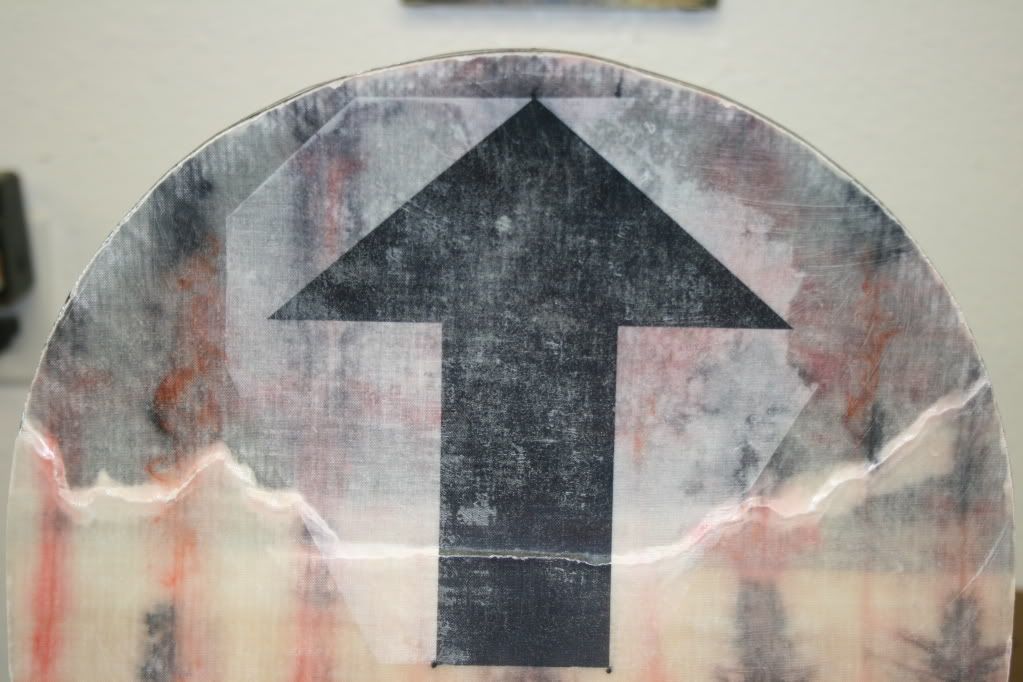
However I must say that my son pile drove into a tree stump after getting some air. One nice thing about this is we were able to peel the top off and re glass the board after pounding the edge back down. I think if we had rounded the tip and he did the same thing we would have had a harder time with the repair.
ra
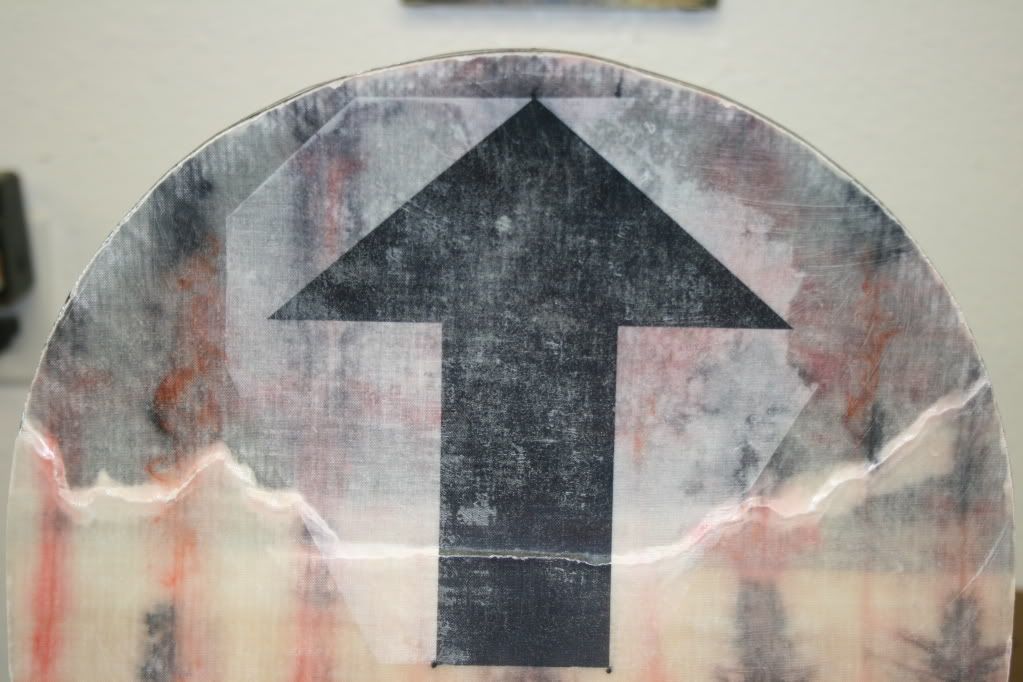
However I must say that my son pile drove into a tree stump after getting some air. One nice thing about this is we were able to peel the top off and re glass the board after pounding the edge back down. I think if we had rounded the tip and he did the same thing we would have had a harder time with the repair.
ra
-
- Posts: 192
- Joined: Tue Mar 15, 2011 2:51 pm
Yup. If you are a metal guy you know climb milling. Unless you're building 15 boards a year why not saw the blank close and hand plane or sand to a sharp line? Don't beat your head against a wall if there is another way that works.ggardner90 wrote:thanks for all the ideas, its your advice is indispensable. i will pick up a bigger bit tomorrow. i think i have been climb milling, i pull it slowly towards me because if i push it rips out instantly then swap sides and go the same direction. i am totally new to sophisticated wood working have background in metal work. is this what you guys are talking about.
totally different topic...i was so mad earlier when i ruined my 3rd core "F@#$ ski building, but then i had a victory, figured out a really fast method to get perfectly bent edges and i feel great again.