Tip and tail molds cracking / splitting
Moderators: Head Monkey, kelvin, bigKam, skidesmond, chrismp
Tip and tail molds cracking / splitting
Hi there,
Like most of you guys I use an glue-up of MDF ribs to make my tip/tail molds.
I've noticed some slight cracking on my first molds, they were made out of 5/8" MDF and the cracks appreared within the MDF ribs (like when you put a screw on the edge of an MDF sheeet without pre-drilling). It was only a subtle crack and I didn't really worried about that.
On my last tip/tail molds, I used 1" MDF and had the ribs CNC cut, making less of a mess in my shop and fewer part for the assembly. Problem is yesterday I had to set up my press for another model and noticed HUGE cracking in those last molds when I took them out of the cavity (I'm even wondering is I can still use those molds) I only had about 8-10 pairs of skis made with those and there's a big crack in the middle (like if the mold would split between 2 ribs except the spliting occurs within a few ribs).
It has split during the week-end when I had the last 2 pairs made within a few hours.
Has anyone ever experienced it ? What do you guys do to prevent this (seal the mold surface?) ?
I press at 80 degC, 40 PSI and my ribs assembly is only glued together (no thru treaded rod) , the glue joints don't seem to have cracked.
I'll take some pics tonight to show what I'm talking about.
Like most of you guys I use an glue-up of MDF ribs to make my tip/tail molds.
I've noticed some slight cracking on my first molds, they were made out of 5/8" MDF and the cracks appreared within the MDF ribs (like when you put a screw on the edge of an MDF sheeet without pre-drilling). It was only a subtle crack and I didn't really worried about that.
On my last tip/tail molds, I used 1" MDF and had the ribs CNC cut, making less of a mess in my shop and fewer part for the assembly. Problem is yesterday I had to set up my press for another model and noticed HUGE cracking in those last molds when I took them out of the cavity (I'm even wondering is I can still use those molds) I only had about 8-10 pairs of skis made with those and there's a big crack in the middle (like if the mold would split between 2 ribs except the spliting occurs within a few ribs).
It has split during the week-end when I had the last 2 pairs made within a few hours.
Has anyone ever experienced it ? What do you guys do to prevent this (seal the mold surface?) ?
I press at 80 degC, 40 PSI and my ribs assembly is only glued together (no thru treaded rod) , the glue joints don't seem to have cracked.
I'll take some pics tonight to show what I'm talking about.
A bad day skiing is always better than a good one at work...
Hi Ben,
My ski tip mold were made the same way - glued and clamped. I've had a bit of cracking, but nothing too problematic. Instead of a steel threaded bar, I used a wooden dowel.
It sounds like you are wondering if it could be caused by heating and cooling and some inter-action with the moisture content of the MDF. I wouldn't be too surprised if this was the issue. I'm aware there is a green MDF, which is moisture resistant.
My ski tip mold were made the same way - glued and clamped. I've had a bit of cracking, but nothing too problematic. Instead of a steel threaded bar, I used a wooden dowel.
It sounds like you are wondering if it could be caused by heating and cooling and some inter-action with the moisture content of the MDF. I wouldn't be too surprised if this was the issue. I'm aware there is a green MDF, which is moisture resistant.
-
- Posts: 217
- Joined: Sun Jan 22, 2012 10:03 pm
- Location: The Dalles Oregon
Bolting would help a lot. Speaking of MDF, I just bought a sheet from Home Depot, 3/4" 4X8, and this sheet was twice as heavy as any MDF I have ever had before. I can carry two full sheets by myself no problem, but this sheet I had to have help just getting it off the rack! So with that said, there are so many types/ quailty of MDF out there, maybe you just have some crapy MDF?
Yes exactly I'm really thinking about sealing everything (after I've re-built the molds...). I know the MDF is basically 2 hard skins with a softer "core", and this soft core is what actually broke... If I can protect it from the elements (moisture to name it) it would be a good start.
The wooden dowel is a neat idea, problem is my molds are pretty thin in the area closer to the center of the ski so they match my 5/8" MDF used between the 2 molds, I don't think I can put a dowel in there... but maybe..
The wooden dowel is a neat idea, problem is my molds are pretty thin in the area closer to the center of the ski so they match my 5/8" MDF used between the 2 molds, I don't think I can put a dowel in there... but maybe..
A bad day skiing is always better than a good one at work...
... I think I used PVA to protect the face of the tip mold. Perhaps even some of the way round too.
You're using a vertically laminated piece of MDF between the two tip molds? I was thinking hardboard, but perhaps you need sticky backed plastic, so you can continue to use the various parts inter-changeably.
You're using a vertically laminated piece of MDF between the two tip molds? I was thinking hardboard, but perhaps you need sticky backed plastic, so you can continue to use the various parts inter-changeably.
Last edited by Richuk on Mon Oct 15, 2012 9:24 am, edited 1 time in total.
I do not get cracking in my molds. i used onlg threaded rods with nuts and washers to join them this allows for some slight flex in the mold relieve the stress. I wonder since your mold is essentially a solid unit if there is some shearing due to it not being 100% perfect causing the cracks.
Fighting gravity on a daily basis
www.Whiteroomcustomskis.com
www.Whiteroomcustomskis.com
No, the part between the 2 tip molds is just a single flat piece of 5/8" MDF, this one is OK.Richuk wrote:You're using a vertically laminated piece of MDF between the two tip molds? I was thinking hardboard, but perhaps you need sticky backed plastic, so you can continue to use the various parts inter-changeably.
I think Vinman is also onto something with the stress on such a solid block of MDF... I'll add some holes to run a couple treaded rods through the block when I'll have the ribs re-cut.
A bad day skiing is always better than a good one at work...
-
- Posts: 2204
- Joined: Tue Mar 07, 2006 8:25 pm
- Location: Kenmore, Wa USA
I have to agree with the majority on this one.
Use bolts don't glue.
Mdf like everything else expands and contracts with temp difference.
Leaving the pieces to float abit will help with that.
The pieces on the ends will get hotter faster(and cool faster) causing warpage. This could lead to the center (or ends) not being properly supported and the mold cracking.
If your molds are still true you could probably fill the cracks with sawdust/glue sand back down flush.
I've used a foam roller to paint epoxy on my tip/tail molds. Once they're set up I waxed them.
Really helped to stop them coming apart when a bit of epoxy from your layup gets on them.
Also the majority of MDF on the shelves these days is the ultra light stuff.
The good dense stuff is getting harder to find
sam
Use bolts don't glue.
Mdf like everything else expands and contracts with temp difference.
Leaving the pieces to float abit will help with that.
The pieces on the ends will get hotter faster(and cool faster) causing warpage. This could lead to the center (or ends) not being properly supported and the mold cracking.
If your molds are still true you could probably fill the cracks with sawdust/glue sand back down flush.
I've used a foam roller to paint epoxy on my tip/tail molds. Once they're set up I waxed them.
Really helped to stop them coming apart when a bit of epoxy from your layup gets on them.
Also the majority of MDF on the shelves these days is the ultra light stuff.
The good dense stuff is getting harder to find

sam
You don't even have a legit signature, nothing to reveal who you are and what you do...
Best of luck to you. (uneva)
Best of luck to you. (uneva)
-
- Posts: 217
- Joined: Sun Jan 22, 2012 10:03 pm
- Location: The Dalles Oregon
Allright... back from the shop...
first, some skibuilding p0rn from last week-end :
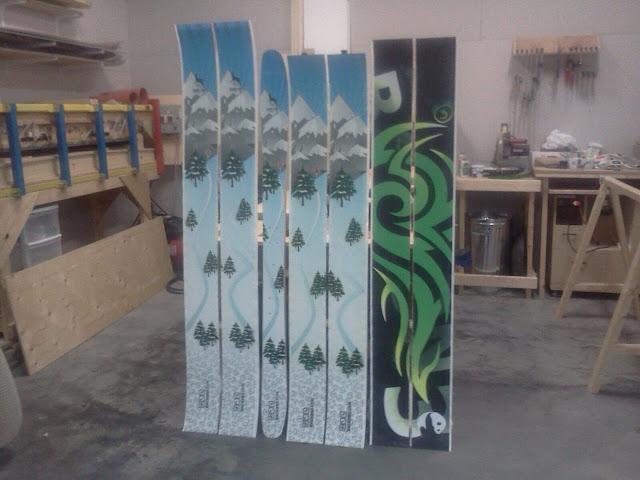
From left to right : 188cm/115underfoot - 180cm/108underfoot - 172cm/108underfoot - 176cm/108underfoot (old model), I'll post pics when those are trimmed !
So, regarding the molds :
I was not able to take a pic of the crack because it has disappeared ! well not completely but it's very subtle and my crappy phone won't show anything... So I can say this cracking is caused by temperature : I pulled the molds just after the freshly (=still hot) pressed ski yesterday. The large cracks made the mold surface very uneven, today everything looks fine !
Regarding the center "flat" plate, I ched and a Richuk is right : it's not 100% flat anymore, I don't really notice the 2 ski shapes but it's definitely a bit concave.
While I was at checking that I checked the "flatness" of my camber base mold, the part that never leaves the press. It's a sheet of 3/4" MDF + a ribbed camber mold (everything glued together and a few treaded rods through it) and everything is covered by another 5/8" MDF flat... it's concave too even if I resurfaced it last year after I moved to a new shop.
I don't know if the MDF I'm using is a bad quality but for my different molds I used different suppliers and the result is always the same, it weights a ton though but all my tip molds have cracked at some point)... maybe we only have junk MDF here in Quebec, I wouldn't be that surprised...
So I guess I have a lot of questions now but I'll only start with one :
It seems like almost everyone is making their molds out of MDF and I don't think I have a very special setup with my "stay-in-place" camber mold + 2 tip molds that I can move + the center flat piece... I'm also no the only one to have a heated press.
What do you guy do so everything doesn't get bowed after 10 or 15 pairs of skis being pressed ? I would be very surprised to hear that ON3P machines a new mold everyday to prevent that for example...
Do you guy check the flatness of you molds very often ?
I'm all ears (or eyes) open for your experience and/or suggestions.
Thanks
Ben
first, some skibuilding p0rn from last week-end :
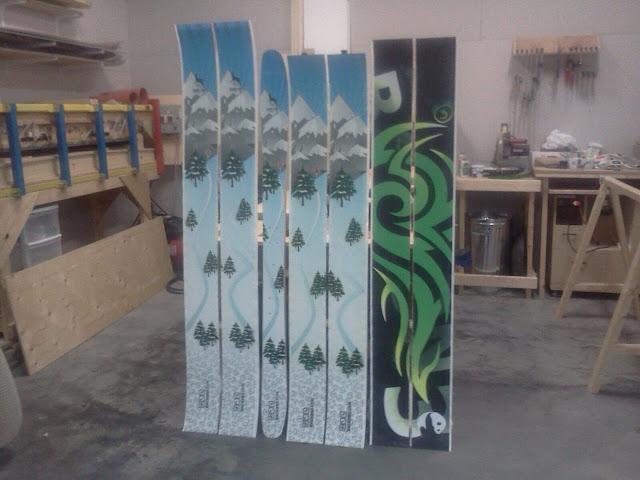
From left to right : 188cm/115underfoot - 180cm/108underfoot - 172cm/108underfoot - 176cm/108underfoot (old model), I'll post pics when those are trimmed !
So, regarding the molds :
I was not able to take a pic of the crack because it has disappeared ! well not completely but it's very subtle and my crappy phone won't show anything... So I can say this cracking is caused by temperature : I pulled the molds just after the freshly (=still hot) pressed ski yesterday. The large cracks made the mold surface very uneven, today everything looks fine !
Regarding the center "flat" plate, I ched and a Richuk is right : it's not 100% flat anymore, I don't really notice the 2 ski shapes but it's definitely a bit concave.
While I was at checking that I checked the "flatness" of my camber base mold, the part that never leaves the press. It's a sheet of 3/4" MDF + a ribbed camber mold (everything glued together and a few treaded rods through it) and everything is covered by another 5/8" MDF flat... it's concave too even if I resurfaced it last year after I moved to a new shop.
I don't know if the MDF I'm using is a bad quality but for my different molds I used different suppliers and the result is always the same, it weights a ton though but all my tip molds have cracked at some point)... maybe we only have junk MDF here in Quebec, I wouldn't be that surprised...
So I guess I have a lot of questions now but I'll only start with one :
It seems like almost everyone is making their molds out of MDF and I don't think I have a very special setup with my "stay-in-place" camber mold + 2 tip molds that I can move + the center flat piece... I'm also no the only one to have a heated press.
What do you guy do so everything doesn't get bowed after 10 or 15 pairs of skis being pressed ? I would be very surprised to hear that ON3P machines a new mold everyday to prevent that for example...
Do you guy check the flatness of you molds very often ?
I'm all ears (or eyes) open for your experience and/or suggestions.
Thanks
Ben
A bad day skiing is always better than a good one at work...
Damn ... I was hoping to hear an 'all clear'.
If you only ever use MDF when it is vertically laminated, you shouldn't have a problem (IMHO). You may need to double check you cassette - but if your bases grind OK, you should be good to use them again.
From what I can see from your album, your stay in place camber is vertically laminate. The section above this, running the length of the press is MDF - its a bit redundant and susceptible to the problem you have just discovered. I would drop it and simply replace your centre section with plywood or similar.
The good news is that you have enough room in your press to convert to adjustable camber and the final piece of good news is that you make great skis!
If you only ever use MDF when it is vertically laminated, you shouldn't have a problem (IMHO). You may need to double check you cassette - but if your bases grind OK, you should be good to use them again.
From what I can see from your album, your stay in place camber is vertically laminate. The section above this, running the length of the press is MDF - its a bit redundant and susceptible to the problem you have just discovered. I would drop it and simply replace your centre section with plywood or similar.
The good news is that you have enough room in your press to convert to adjustable camber and the final piece of good news is that you make great skis!
Thanks for the input and comments Richuk,
do you mean the deformation problem could well be just located in the sheets of MDF that are used horizontally (= not laminated) ?
It's really no big deal for me to remove this last sheet on the "stay-in-place" part and resurface it for good measure... I'll just need to shim it from underneath.... would you recommend to replace MDF by Plywood even under the ribbed part of this permanent mold ?
Thanks again, really appreciated ! I guess this topic will benefit all the community !
do you mean the deformation problem could well be just located in the sheets of MDF that are used horizontally (= not laminated) ?
It's really no big deal for me to remove this last sheet on the "stay-in-place" part and resurface it for good measure... I'll just need to shim it from underneath.... would you recommend to replace MDF by Plywood even under the ribbed part of this permanent mold ?
Thanks again, really appreciated ! I guess this topic will benefit all the community !
A bad day skiing is always better than a good one at work...
I think you have just reached the margins of what MDF can do for you when horizontally orientated.
The heat, pressure and moisture content have conspired against you. My own experience suggested that 80 degrees appears to be around the point at which things start to go South. Although, I wouldn't be surprised if others in less humid environments weren't having the same issue and I can't say whether the boards I was using had comparable density.
With your set up, I would check the sheet above and below the 'stay in place' part. If they are flat, I would still remove the sheet above the 'stay in place' mold and place it below. This will allow you to retain the same height settings. This assumes that pressure alone has not effected the sheet under the stay in place section - which is being exposed to different levels of pressure due to its interaction with the frame of the press. If there is a bit of damage to each sheet, then it is simply a matter of judgement as to the working life of these boards, given that the overall thickness of the stay in place sheet will iron out a few minor kinks.
If you use a piece of ply between the two tip molds it will start out flat, but it won't be too long before it becomes a little concave - due to one side being exposed directly to heat. At this point - flip it over and happy days! If you wanted, you could press the board without the cassette being present and accelerate this process so that loading wasn't affected on day one. The piece of ply I use is 12mm thick - I'm sure you could go a bit thinner and then mix and match using hardboard to get the height required to match your tip molds.
Apologies for all the detail - I know you get this, but like you said, it might be useful for someone else.
The heat, pressure and moisture content have conspired against you. My own experience suggested that 80 degrees appears to be around the point at which things start to go South. Although, I wouldn't be surprised if others in less humid environments weren't having the same issue and I can't say whether the boards I was using had comparable density.
With your set up, I would check the sheet above and below the 'stay in place' part. If they are flat, I would still remove the sheet above the 'stay in place' mold and place it below. This will allow you to retain the same height settings. This assumes that pressure alone has not effected the sheet under the stay in place section - which is being exposed to different levels of pressure due to its interaction with the frame of the press. If there is a bit of damage to each sheet, then it is simply a matter of judgement as to the working life of these boards, given that the overall thickness of the stay in place sheet will iron out a few minor kinks.
If you use a piece of ply between the two tip molds it will start out flat, but it won't be too long before it becomes a little concave - due to one side being exposed directly to heat. At this point - flip it over and happy days! If you wanted, you could press the board without the cassette being present and accelerate this process so that loading wasn't affected on day one. The piece of ply I use is 12mm thick - I'm sure you could go a bit thinner and then mix and match using hardboard to get the height required to match your tip molds.
Apologies for all the detail - I know you get this, but like you said, it might be useful for someone else.