Living-room project... CNC !
Moderators: Head Monkey, kelvin, bigKam, skidesmond, chrismp
-
- Posts: 1148
- Joined: Tue Jan 08, 2008 6:02 am
- Location: NJ USA
- Contact:
my input has a 90deg elbow that you cant see, under the lid... so the chips enter and swirl around. I tested it with small bits of paper wads and you can hear them suck thru the tube and land in the bin and rattle around in the can.
Time will tell regarding its performance, but thanks for that tip anyway!
Time will tell regarding its performance, but thanks for that tip anyway!
Doug
-
- Posts: 1148
- Joined: Tue Jan 08, 2008 6:02 am
- Location: NJ USA
- Contact:
and yea i dont think it's gonna stop most of the MDF dust... but hopefully any larger chips and at least reduce the amount of bag removals.
And I agree, empty the can when it hits about the half way point, or it will just start suckin crap in.
I might put a screen on the face of the exit of the lid. I wonder how fast that would clog up.
And I agree, empty the can when it hits about the half way point, or it will just start suckin crap in.
I might put a screen on the face of the exit of the lid. I wonder how fast that would clog up.
Doug
-
- Posts: 1148
- Joined: Tue Jan 08, 2008 6:02 am
- Location: NJ USA
- Contact:
and i think i spent: portable Delta dust collector: $100.
metal can: $27
mdf lid: $free.99
2 elbows and 20' of corex: 20 bucks?
so about $150 total for my dust collection
in the future i'll probably replace the black corex with more flexible piping.
Maybe some clear so i can see if it's plugged up.
metal can: $27
mdf lid: $free.99
2 elbows and 20' of corex: 20 bucks?
so about $150 total for my dust collection
in the future i'll probably replace the black corex with more flexible piping.
Maybe some clear so i can see if it's plugged up.
Doug
You probably want a cyclonic separator on there.
http://www.floweringelbow.org/projects/ ... separator/
http://www.floweringelbow.org/projects/ ... separator/
-
- Posts: 1148
- Joined: Tue Jan 08, 2008 6:02 am
- Location: NJ USA
- Contact:
-
- Posts: 1148
- Joined: Tue Jan 08, 2008 6:02 am
- Location: NJ USA
- Contact:
Finally some progress on the CNC :
After 4+ hours of machining (1638 holes + 5 slots) : The "permanent" part of the vacuum/t-tracks table is done !
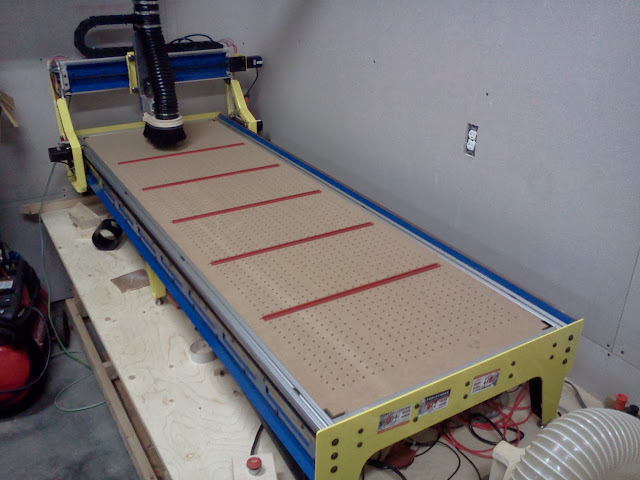
Tomorrow I'll glue the sacrificial layer on top of that and start drilling again...
The Dust Separator is being tested too, for now I'm very satisfied : after all the MDF drilling, I only have a very small quantity of dust in the dust collector bag... I would say 95% of the dust was captured in the trashcan under the separator... I have to see how I can improve the separation of very fine dust (MDF) but for now it's OK so I'm gonna work on hard-ducting the system in order to improve the suction (less elbows, less flex hose -» more efficient) .


After 4+ hours of machining (1638 holes + 5 slots) : The "permanent" part of the vacuum/t-tracks table is done !
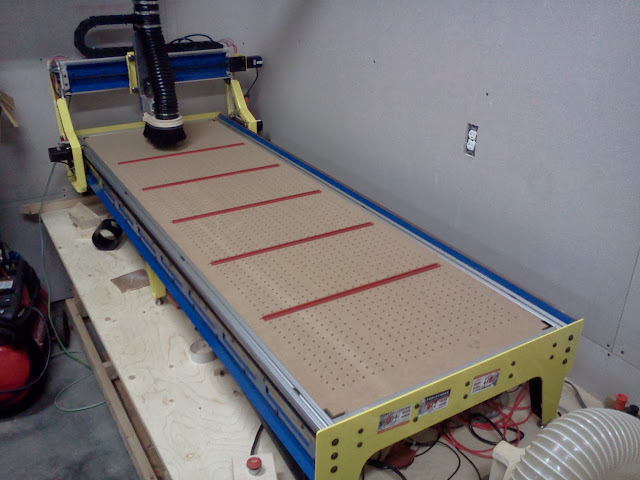
Tomorrow I'll glue the sacrificial layer on top of that and start drilling again...
The Dust Separator is being tested too, for now I'm very satisfied : after all the MDF drilling, I only have a very small quantity of dust in the dust collector bag... I would say 95% of the dust was captured in the trashcan under the separator... I have to see how I can improve the separation of very fine dust (MDF) but for now it's OK so I'm gonna work on hard-ducting the system in order to improve the suction (less elbows, less flex hose -» more efficient) .


A bad day skiing is always better than a good one at work...
-
- Posts: 1148
- Joined: Tue Jan 08, 2008 6:02 am
- Location: NJ USA
- Contact:
"decking" the platform. The top is screwed down, and i didn't sink 2 screws deep enough, so just after this shot the bit ran over 2 screws and it definitely chipped the bit, the cutting sound changed dramatically and i can feel a slight pinch in height difference
. Oh well, good enough for government work!
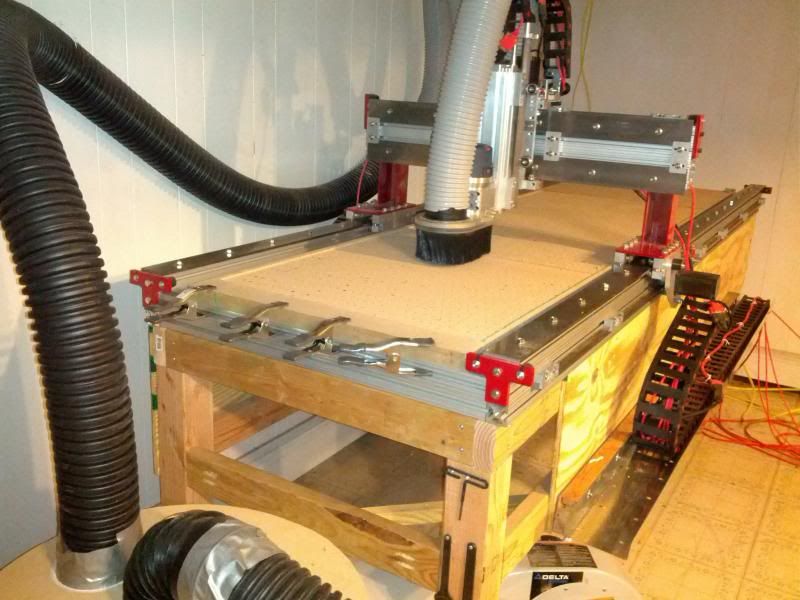

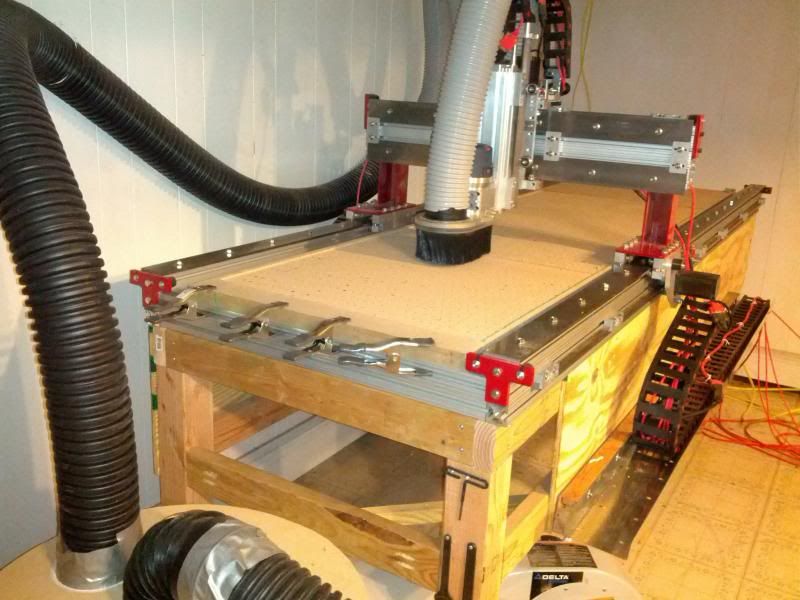
Doug
-
- Posts: 80
- Joined: Wed Dec 19, 2012 11:00 am
- Location: Kelowna BC
Hey man, I've got an almost identical setup on my rig, was the second thing I made on the machine after the first thing basically destroyed the garage with dust. There's a sweet spot for the distance the suction hose protrudes into the cyclone that works best for fines. There's a good video series on youtube of a guy that experimented quite a bit, I'll see if I can find it again. Somewhere between half way and a little over halfway, but you just have to play around with it. A quick MDF bellmouth inlet for the end of the suction hose inside there will also get a lot of your flow back. Big head loss on budget DC blowers is the only real down side to those cyclones, still definitely the most useful tool in the shop tho. I put my blower in a 3/4 thick MDF box and you can barely even hear it when its on.ben_mtl wrote:I have to see how I can improve the separation of very fine dust (MDF) but for now it's OK so I'm gonna work on hard-ducting the system in order to improve the suction (less elbows, less flex hose -» more efficient)
-
- Posts: 2204
- Joined: Tue Mar 07, 2006 8:25 pm
- Location: Kenmore, Wa USA
Funny, I did this exactly same thing when I was doing this on mine. Luckily it didn't damage the bit, but it definitely cut through a few bolt heads. Oops.knightsofnii wrote:"decking" the platform. The top is screwed down, and i didn't sink 2 screws deep enough, so just after this shot the bit ran over 2 screws and it definitely chipped the bit, the cutting sound changed dramatically and i can feel a slight pinch in height difference. Oh well, good enough for government work!
-
- Posts: 1148
- Joined: Tue Jan 08, 2008 6:02 am
- Location: NJ USA
- Contact:
yea it ruined a 40 dollar bit, that's ok, i want downcutting bits anyway so it doesnt pull anything up.
The dust collection works great as long as you have the bit set so that the brushes make contact with the work then it creates a lot of vacuum
. Even if its too high it reduces the dusting dramatically.
Reduced cleanup from 5hr to 5min hahaha.
alot of the MDf dust goes into the bag, but the can traps the bigger particles
The dust collection works great as long as you have the bit set so that the brushes make contact with the work then it creates a lot of vacuum

Reduced cleanup from 5hr to 5min hahaha.
alot of the MDf dust goes into the bag, but the can traps the bigger particles

Doug
-
- Posts: 1148
- Joined: Tue Jan 08, 2008 6:02 am
- Location: NJ USA
- Contact:
-
- Posts: 1148
- Joined: Tue Jan 08, 2008 6:02 am
- Location: NJ USA
- Contact:
so the machine was acting funny and not cutting very precise along shapes where it had to repeat its cut it was skewed by upwards of 1/8" at times, then it would go back to perfect.
It appeard one motor was "studdering", I decided to take the drive units apart, and all the setscrews for each drive gear attached to the motor shafts were all spun out, and i lost half of them.
Luckily i found some new longer setscrews with threadlocker on them, just to be sure i put more threadlocker and tightened them down alot.
The gears were chewed up on their inside diameter a pinch and i had to sand that all out. Havent run it yet, wanted to give it a day to let the threadlock cure nice and snug. but I'm hoping for far more precision
.
It appeard one motor was "studdering", I decided to take the drive units apart, and all the setscrews for each drive gear attached to the motor shafts were all spun out, and i lost half of them.
Luckily i found some new longer setscrews with threadlocker on them, just to be sure i put more threadlocker and tightened them down alot.
The gears were chewed up on their inside diameter a pinch and i had to sand that all out. Havent run it yet, wanted to give it a day to let the threadlock cure nice and snug. but I'm hoping for far more precision

Doug