i would contribute back to the forum. i really appreciate everyones contributions to this site, pictures, tips, etc....
PRESS FRAME is constructed of 8X8 35lb per foot i-beams. side frames are fabricated from welded u-channel uprights and and i-beam cross members that are boxed with with steel plate. the side frames are easily
converted for a double bay press by adding more crossmembers.
LOWER MOLD has adjustable tipblocks via slotted plates, running lengths
are changed by inserting different 3/4" mdf center sections. transition from center section to tipblocks is very smooth with this design. i plan
on changing the center section to a "permanent" piece of mdf with the shortest running length i plan on building and then placing a "cattrack like"
series of mdf or hardwood blocks side by side for longer RLs. (HEAD MONKEY you should try this mod, i think it is going to work very well since you are building boards of different lengths for your customers)
UPPER MOLD is adjustable by changing the length of the center spacer section with the drilled plates. it is hung and slides on the i-beams by
aluminium angle.
CATTRACK is radiused 3/4" X .120" alum. square tubing (i went with 3/4"
instead of 1" because i plan on eventually building some snowboards with
flat nose and tail kicks and felt the smaller size would get into the tighter
initial radius a little better.) it is suspended by a series of springs that hold
it up firmly when bladders are deflated. bladders are (2) 5" lines.
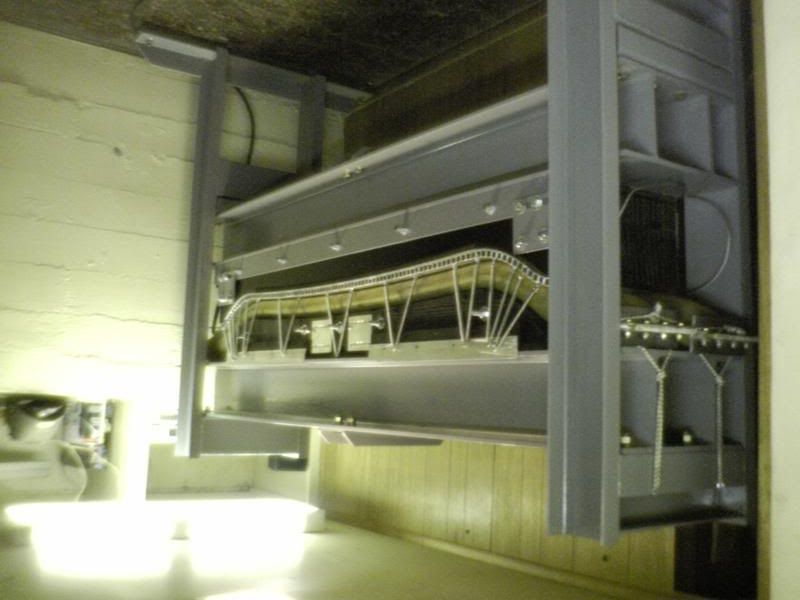
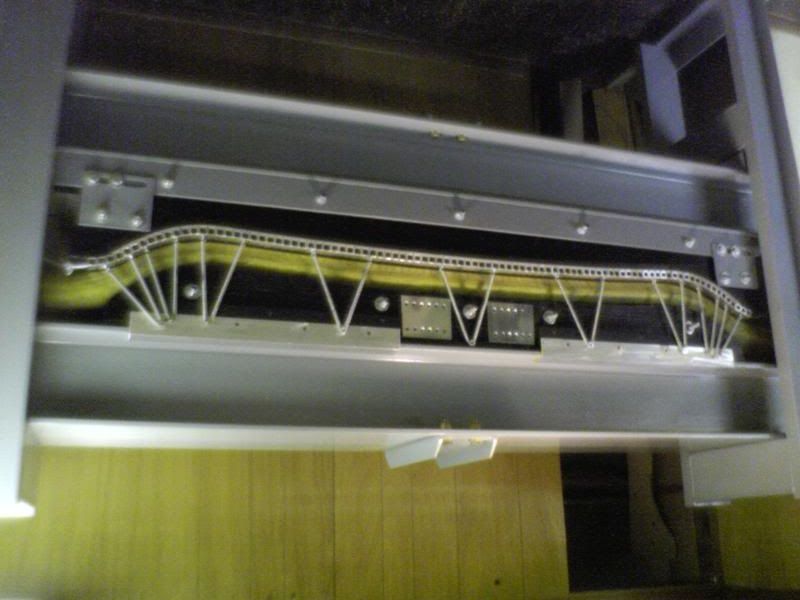
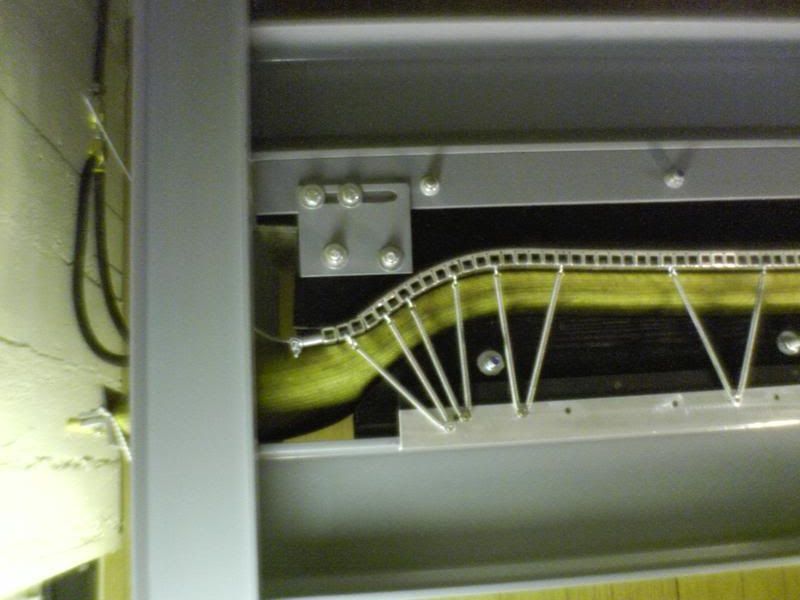
THINGS I WOULD HAVE DONE DIFFERENTLY:
-decreased the initial throat opening of the design(used steel tube spacers
under the lower i-beams to adjust to what i needed, which was easy with my design but would have been better if i calculated right the first time)
-the tip block adjustment (slotted plate) system is way overbuilt, a simple
alum. plate fastened with sheetrock screws to the tip blocks and camber block would be sufficient because the bladders hold the tip blocks in place nicely once inflated. (would have saved me lots of time)
for loads of more pictures of my pressframe, adjustable mold, laser cut
camber block router jig, tip block router jig, and other stuff, check out
http://www.flickr.com/photos/hydrant71/
long live american made skis and snowboards.
Jason